-
- News
- Books
Featured Books
- smt007 Magazine
Latest Issues
Current IssueIntelligent Test and Inspection
Are you ready to explore the cutting-edge advancements shaping the electronics manufacturing industry? The May 2025 issue of SMT007 Magazine is packed with insights, innovations, and expert perspectives that you won’t want to miss.
Do You Have X-ray Vision?
Has X-ray’s time finally come in electronics manufacturing? Join us in this issue of SMT007 Magazine, where we answer this question and others to bring more efficiency to your bottom line.
IPC APEX EXPO 2025: A Preview
It’s that time again. If you’re going to Anaheim for IPC APEX EXPO 2025, we’ll see you there. In the meantime, consider this issue of SMT007 Magazine to be your golden ticket to planning the show.
- Articles
- Columns
Search Console
- Links
- Media kit
||| MENU - smt007 Magazine
The Need for Real-time Measurements on the Factory Floor
April 5, 2023 | Barry Matties, I-Connect007Estimated reading time: 5 minutes
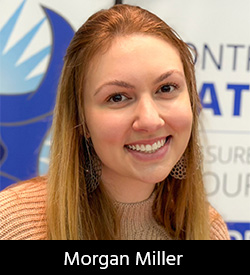
During SMTA Dallas Expo, Barry Matties speaks with Morgan Miller, field application engineer at Insituware, about the need for real-time measurements on the factory floor.
Barry Matties: Hi Morgan, would you give us a quick introduction of your company before we talk about the technology?
Morgan Miller: We have multiple products that will measure your materials. On the factory floor, you’ll be able to measure the materials instead of sending them out to a lab and it also gives you the ability for traceability of materials control. All our pieces of equipment basically have a traceability back to an SPC web app, so you’re able to export that data, keep it for yourself, give it to other customers, and so on.
Matties: So, the material you’re measuring have conformal coatings and solder paste and thickness and that sort of thing?
Miller: Yes. Depending on the product you’re working with, we measure most of the materials in the electronics industry—conformal coating, solder paste, adhesives, epoxies. We have a modular device— the handheld Vision MARK-1—and it’s part of something called an Insight. We like to think of this as a Swiss army knife tool where you can slide in different modules. If you have other materials that you want to test, we can basically build the software and hardware around that and be able to test those materials.
Matties: Why is this important for fabricators? Not all this testing is a requirement yet. Why should they be doing this?
Miller: It’s just starting to become a requirement in the aerospace world and some of the auto world where you need traceability of materials control. This is important because when we’re building these things that go in your car or things that hang from the ceiling; it’s very important to make sure that your entire process to build those things is controlled. Right now in the SMT world, we’re controlling everything except for the materials, and it’s the materials that have caused a lot of problems to begin with. We overlooked that aspect when we were building these circuit boards.
Matties: Right. So if it’s not required, why would someone want to do it?
Miller: Because if you don’t there could be issues later down the line. You may be using material that’s bad but not know it’s bad. Iit’s not necessarily manufacturers that are creating bad material, because in this day and age, everybody’s a chemist and they create great materials, especially in the solder paste world. These are great materials to begin with, but there are things in your process that cause them to change, and once they change, they’re not going to act the same as they did when they were first manufactured. What changes can they cause? Well, if the material is exposed to the atmosphere—for instance, solder paste absorbs moisture. It’s a hygroscopic material. It’s a chemical reaction that’s occurring and it’s going to affect that reaction. That can cause issues down the line if the materials, if this joint, has absorbed moisture in this case. It can cause printing issues as well as reflow issues.
Matties: Certainly people are doing some material testing out there. What makes this unique compared to what they’re already doing?
Miller: Typically people are testing the material after, so they’ll make sure it’s using SPI, that it printed the correct amount. Maybe they’ll look at AOI and they’re making sure that it’s on the correct solder mask. The point is that you’re testing the material in its raw form, and throughout the entire process, you’re able to take these quick measurements to understand, “I am testing the material the entire process. I know that it’s good when it’s being printed. I know that it’s good once it’s printed, using SPI, using AOI.”
Matties: That’s traceability right there, right?
Miller: Yes.
Matties: It’s not necessarily an inline process, but a manual process operator driven?
Miller: Yes, it is operator driven. In the case of a smart mixer, this is allowing you to measure your material while it’s mixing and during the mixing process. It has a smart capability that’s taking those measurements. With the Vision MARK-1, you can take measurements straight off your printer. You just take a two-gram sample off, put it on the Vision MARK-1, click the start measurement, and walk away. You’re able to take these quick measurements, and then you have the thickness tester for conformal coatings or basically any material that’s transparent. That’s a benchtop unit as well. They are more manual processes, but we are eventually going to make them less manual in the case of maybe creating a stencil printer probe or with having an inline thickness tester. It’s manual right now, but it may not always be manual.
Matties: It will evolve.
Miller: Yes, like everything.
Matties: Now, obviously our world is becoming data driven. How does the data get collected, how is it interpreted, and how does it help them?
Miller: With all our equipment, we have control limits and thresholds that can be set up. We have an SPC web app where you’re able to create those thresholds, these pass or fail limits, so that when you take a measurement with any one of our devices, it can pass or fail and give you a result from that. So, in situ in our lab, we create some initial control limits with all our processes for you by doing some lab tests. In that case, when you go to take a measurement, you have some starting grounds where you can basically adjust the control limits that we give you to fit your process. Every measurement you take will automatically upload. Since all our units can be connected to Wi-Fi, they’ll automatically upload the measurement to our SPC web app for traceability. You can easily just click one button and export that data.
Matties: Nice. Do you have any final thoughts you’d like to share with the industry? Any advice you’d like to share?
Miller: Control your materials.
Matties: That’s great. Well, Morgan, thank you so much.
Miller: You’re welcome, Barry.
Suggested Items
Koh Young Installs 24,000th Inspection System at Top 20 EMS
05/14/2025 | Koh YoungKoh Young, the global leader in True 3D measurement-based inspection and metrology solutions, proudly announces the installation of its 24,000th inspection system at a Top 20 Global EMS in Thailand.
Indium’s Karthik Vijay to Present on Dual Alloy Solder Paste Systems at SMTA’s Electronics in Harsh Environments Conference
05/06/2025 | Indium CorporationIndium Corporation Technical Manager, Europe, Africa, and the Middle East Karthik Vijay will deliver a technical presentation on dual alloy solder paste systems at SMTA’s Electronics in Harsh Environments Conference, May 20-22 in Amsterdam, Netherlands.
SolderKing Achieves the Prestigious King’s Award for Enterprise in International Trade
05/06/2025 | SolderKingSolderKing Assembly Materials Ltd, a leading British manufacturer of high-performance soldering materials and consumables, has been honoured with a King’s Award for Enterprise, one of the UK’s most respected business honours.
Knocking Down the Bone Pile: Gold Mitigation for Class 2 Electronics
05/07/2025 | Nash Bell -- Column: Knocking Down the Bone PileIn electronic assemblies, the integrity of connections between components is paramount for ensuring reliability and performance. Gold embrittlement and dissolution are two critical phenomena that can compromise this integrity. Gold embrittlement occurs when gold diffuses into solder joints or alloys, resulting in mechanical brittleness and an increased susceptibility to cracking. Conversely, gold dissolution involves the melting away of gold into solder or metal matrices, potentially altering the electrical and mechanical properties of the joint.
'Chill Out' with TopLine’s President Martin Hart to Discuss Cold Electronics at SPWG 2025
05/02/2025 | TopLineBraided Solder Columns can withstand the rigors of deep space cold and cryogenic environments, and represent a robust new solution to challenges facing next generation large packages in electronics assembly.