-
- News
- Books
Featured Books
- design007 Magazine
Latest Issues
Current IssueAll About That Route
Most designers favor manual routing, but today's interactive autorouters may be changing designers' minds by allowing users more direct control. In this issue, our expert contributors discuss a variety of manual and autorouting strategies.
Creating the Ideal Data Package
Why is it so difficult to create the ideal data package? Many of these simple errors can be alleviated by paying attention to detail—and knowing what issues to look out for. So, this month, our experts weigh in on the best practices for creating the ideal design data package for your design.
Designing Through the Noise
Our experts discuss the constantly evolving world of RF design, including the many tradeoffs, material considerations, and design tips and techniques that designers and design engineers need to know to succeed in this high-frequency realm.
- Articles
- Columns
- Links
- Media kit
||| MENU - design007 Magazine
DFM Analysis for Flex and Rigid-flex Design, Part 1
April 17, 2023 | Mark Gallant, DownStream TechnologiesEstimated reading time: 3 minutes
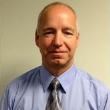
Introduction
Flex and rigid-flex PCB constructions are not new concepts. It has become commonplace as engineers look for alternative circuit packaging for ever-shrinking electronic products. A flat, one-sheet schematic for a straight ribbon cable is analogous to its physical flat substrate. A flat, multi-sheet schematic that details circuitry for a rigid-flex design bears little visual resemblance to its three-dimensional, variable material rigid-flex assembly. However, in both schematic examples, schematic-based analysis tools are applied equally. This same truth also applies to common FR-4-based two-layer or multilayer PCBs.
Today’s PCB analysis tools are applicable across all combinations of rigid PCBs regardless of layer count or size. However, due to the unique properties of flexible substrates and combined flexible and rigid substrates, flexible designs require a specific collection of analysis both functional and manufacture oriented.
Signal integrity analysis such as impedance, coupling, crosstalk and noise is complicated by variable stackups across flexible designs. A single transmission line can be stripline in a rigid-flex area and microstrip in a flex area. Material types and dielectric constants above or below a trace as it traverses a design also vary. While the challenges for signal integrity analysis for flexible designs is worthy of conversation, this article will focus on the current challenges to design-for-manufacture analysis of flex and rigid-flex designs.
Contrasting Rigid PCBs With Flex and Rigid-flex
Some designers design flexible PCBs as simple bendable circuit boards, but there are vast differences between rigid and flexible. Both technologies produce an electrical interconnect function, but are manufactured using different types of materials and processes. They also have varying applications. No need to design a rigid-flexible PCB for the motherboard of a desktop PC, but rigid-flex is required for most medically implanted devices.
A typical rigid PCB is comprised of electrodeposited copper-clad fiberglass substrates bonded together. While there are variations on materials used to bond substrates, it is commonly sheets of cloth pre-impregnated with uncured epoxy. This bonding material composition is not engineered to be flexible. The copper is chemically etched to create a circuit pattern. The hardness of the bonded substrates requires mechanical routing to trim the raw PCBs. All layers of the PCB are commonly identical in size and shape unless cavities, embedded components, or other such exotic construction is present. The rigid PCB layer stackup is identical across the entire PCB area. Solder mask and legend are almost always applied.
Flexible PCBs are comprised of rolled annealed copper over flexible polyimide substrates. Flexible layers or cores are produced with or without adhesives. Adhesiveless flex is prevalent in applications requiring higher performance, while those with adhesives are often found in low layer-count applications. The most common usage is copper foil laminated to a substrate with epoxy or acrylic adhesive. Both substrate material and adhesive are engineered for bending to minimize trace fracture. Like rigid PCBs, a chemical etching process is used to create a circuit pattern. The flexible nature of the materials requires die cutting or “blanking” rather than mechanical routing. Each layer of a flexible double-sided core has an identical shape.
However, multilayer flex is likely to have variations in shape for each layer or core. Flexible PCBs require a thin film insulator over the conductors know as a coverlay. Unlike rigid PCB solder masks, coverlays are die cut much like the flexible layers they insulate. The stackup of a multi-layer flexible PCB can vary across the PCB area. This is especially true with multilayer flex where layer shape varies among the collection of layers or cores. A flexible ground or power plane area is typically crosshatched versus solid for rigid PCBs. The crosshatch reduces potential for fracture of conductors. Alternatively, flexible layers can be shielded with a layer of copper or silver foil. Masking and screening over flexible layers is not rare, but uncommon.
To read this entire article, which appeared in the April 2023 issue of Design007 Magazine, click here.
Suggested Items
Driving Innovation: Direct Imaging vs. Conventional Exposure
07/01/2025 | Simon Khesin -- Column: Driving InnovationMy first camera used Kodak film. I even experimented with developing photos in the bathroom, though I usually dropped the film off at a Kodak center and received the prints two weeks later, only to discover that some images were out of focus or poorly framed. Today, every smartphone contains a high-quality camera capable of producing stunning images instantly.
Hands-On Demos Now Available for Apollo Seiko’s EF and AF Selective Soldering Lines
06/30/2025 | Apollo SeikoApollo Seiko, a leading innovator in soldering technology, is excited to spotlight its expanded lineup of EF and AF Series Selective Soldering Systems, now available for live demonstrations in its newly dedicated demo room.
Indium Corporation Expert to Present on Automotive and Industrial Solder Bonding Solutions at Global Electronics Association Workshop
06/26/2025 | IndiumIndium Corporation Principal Engineer, Advanced Materials, Andy Mackie, Ph.D., MSc, will deliver a technical presentation on innovative solder bonding solutions for automotive and industrial applications at the Global Electronics A
Fresh PCB Concepts: Assembly Challenges with Micro Components and Standard Solder Mask Practices
06/26/2025 | Team NCAB -- Column: Fresh PCB ConceptsMicro components have redefined what is possible in PCB design. With package sizes like 01005 and 0201 becoming more common in high-density layouts, designers are now expected to pack more performance into smaller spaces than ever before. While these advancements support miniaturization and functionality, they introduce new assembly challenges, particularly with traditional solder mask and legend application processes.
Knocking Down the Bone Pile: Tin Whisker Mitigation in Aerospace Applications, Part 3
06/25/2025 | Nash Bell -- Column: Knocking Down the Bone PileTin whiskers are slender, hair-like metallic growths that can develop on the surface of tin-plated electronic components. Typically measuring a few micrometers in diameter and growing several millimeters in length, they form through an electrochemical process influenced by environmental factors such as temperature variations, mechanical or compressive stress, and the aging of solder alloys.