-
- News
- Books
Featured Books
- design007 Magazine
Latest Issues
Current IssueProper Floor Planning
Floor planning decisions can make or break performance, manufacturability, and timelines. This month’s contributors weigh in with their best practices for proper floor planning and specific strategies to get it right.
Showing Some Constraint
A strong design constraint strategy carefully balances a wide range of electrical and manufacturing trade-offs. This month, we explore the key requirements, common challenges, and best practices behind building an effective constraint strategy.
All About That Route
Most designers favor manual routing, but today's interactive autorouters may be changing designers' minds by allowing users more direct control. In this issue, our expert contributors discuss a variety of manual and autorouting strategies.
- Articles
- Columns
- Links
- Media kit
||| MENU - design007 Magazine
Estimated reading time: 8 minutes
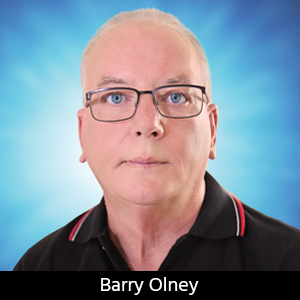
Beyond Design: Select Dielectric Material With Precision
In the past, selecting a dielectric material for PCB fabrication was a no-brainer because we all just used FR-4. Clock frequencies were low and signal rise times were slow, so substrate performance was not an issue. However, in today's multi-gigabit designs, with their extremely fast rise times and tight timing margins, precise material selection is crucial to the performance of the product. This puts the materials selection process under tighter scrutiny. Materials used for the fabrication of multilayer PCBs absorb high frequencies and reduce edge rates, which is a major cause of signal integrity issues. But we’re not all designing cutting-edge boards. Sometimes we tend to over-specify requirements, which can lead to inflated production costs.
Over the years, a huge range of materials has been developed for multilayer PCB fabrication. To give you an idea, iCD now has a choice in its dielectric materials library of more than 700 series of dielectric rigid/flex materials from more than 60 different manufacturers. When each material is used for the right target application, the resultant PCB will have the lowest possible cost, yet still satisfy the design and performance goals of the project.
Electromagnetic energy propagates in a vacuum or in air at the speed of light. But, as the field is enveloped in a dielectric material in the PCB media, it slows down. The signal trace in a PCB simply guides the wave as the electromagnetic energy propagates in the surrounding dielectric material. The signal rides on this carrier wave. It is the dielectric material that determines the velocity (v) of propagation of the electromagnetic energy:
c is the speed of light (in free space) and Dk is the dielectric constant of the material (FR-4 is ~4.0). By contrast, the Dk of air is 1. Therefore, the velocity of propagation in FR-4 is about half the speed of light, or 6 inches per nanosecond.
The electrical properties of a dielectric material can be described by two terms:
- The dielectric constant (Dk) or relative permittivity (Er) is the ratio of the amount of electromagnetic energy stored in a material by an applied voltage. It describes how the material increases the capacitance and decreases the velocity of propagation in the material.
- The dissipation factor (Df) or dielectric loss/loss tangent (tan ?) is a parameter of a dielectric material that quantifies its inherent dissipation of electromagnetic energy.
Dielectric constant and dielectric loss are not a function of the geometry of the transmission line. Rather, they are a function of the dielectric material in which the signal propagates their distribution in the PCB stackup and the applied frequency. These mechanisms contribute to the frequency-dependent loss and to degrade the speed of the signal. The signal quality transmitted through the media and picked up at the receiver will be affected by any impedance discontinuities and losses of dielectric materials. The glass epoxy material (FR-4) commonly used for PCBs has a negligible loss for digital applications below 1 GHz. But at higher frequencies, the loss is of greater concern.
If the signal has a fast rise/fall time, then the electromagnetic wave needs to propagate at a higher speed, and therefore the Dk needs to be low to enable this. If a material with a high dielectric constant is placed in an electric field, the magnitude of that field will be measurably reduced within the volume of the dielectric. Therefore, a lower Dk is desirable for high-speed design. Conversely, a high Dk material is very good at condensing electric fields, so having it between the planes increases planar capacitance.
An efficient dielectric material supports a varying charge with minimal dissipation of energy in the form of heat. There are two main forms of loss that may dissipate energy within a dielectric:
- Conduction loss is the flow of charge through the material that causes energy dissipation.
- Dielectric loss is the dissipation of energy through the movement of charges in an alternating electromagnetic field as polarization switches direction.
Dielectric loss is especially high around the resonant frequencies of the polarization mechanisms as the polarization lags behind the applied field, causing an interaction between the field and the dielectric’s polarization that results in heating (Figure 1).
There are also thermal factors to consider. The most important is the glass transition temperature (Tg), which is the point at which a glassy solid changes to an amorphous resin/epoxy. If the reflow temperature exceeds the Tg for an extended period, the material rapidly expands in the Z-axis. Plus, mechanical material properties degrade rapidly—strength and bonds in the material. A high Tg guards against barrel cracking and pad fracture during reflow. Standard FR-4 has a Tg of 135-170°C, whereas the high-speed materials are generally well over 200°C.
Decomposition temperature (Td) is the temperature at which the material chemically decomposes. This is the maximum limit or the point of no return. Most materials have a Td of 320°C, so it is not an issue. The coefficient of thermal expansion (CTE) in the Z direction is the rate of expansion as the material heats up. The CTE should be as low as possible (
With so many materials to choose from, which is the best for your specific product? Low cost generally means low quality. But the price of poor yields drives up the final material cost. Dielectric material selection is usually driven by the frequency and rise time of the digital signal, with lower values of loss most suitable for high-frequency applications. These materials generally exhibit lower values of dielectric constant, resulting in faster signal propagation. Table 1 shows the loss profile ranges of dielectric materials.
Figure 2 depicts the profile for dielectric materials with a Df < 0.005. The iCD materials planner has five default profiles ranging from basic FR-4 to ultra-low loss materials, as in Table 1. This enables the designer to compare dielectric materials based on manufacturer, fabricator, frequency, dissipation factor (loss), and dielectric constant.
Another issue is that materials available locally (vs. offshore) can vary from fabricator to fabricator. Typically, prototype boards are fabricated locally, whereas those made in Asia are a more economical option for mass production. Profiles of PCB fabricators can be set up to display the complete range of materials each fab shop stocks, enabling comparison among shops.
Figure 3 plots the loss properties of dielectric materials from an Asian fabricator. One can easily see which materials are best for high-speed applications and can choose among a few materials that are in stock. Cost-to-performance evaluations must still be done to ensure that the lowest-cost material is selected to do the job. Also, keep in mind that material costs vary with quantity.
Matching material performance numbers of the dielectric constant is also important. A small difference in the value between materials can significantly impact impedance, line widths/clearances, and thus losses. Also, the dielectric constant of a material determines the propagation velocity of the signal in the medium. So, if Dk values vary on different layers of the substrate, then bus signal timing may also become an issue. One should consider construction options that allow a drop-in material that matches the impedance, and Dk, for each layer of the stackup.
PCB designers need to quickly choose the best, most cost-effective material for their application from among the vast array of choices available. Sorting through numerous slash sheets and datasheets is very time-consuming. A direct visual comparison of dielectric materials—based not only on the manufacturer’s product lines, but, more importantly, on one’s preferred fabricator’s stock—is undoubtedly the most efficient approach for material selection.
Key Points
- Materials used for the fabrication of multilayer PCBs absorb high frequencies and reduce edge rates, which is a major cause of signal integrity issues.
- When each material is used for the right target application, the resultant PCB will have the lowest possible cost, yet still satisfy the design and performance goals of the project.
- Electromagnetic energy propagates in a vacuum or in air at the speed of light. But, as the field is enveloped in a dielectric material in the PCB media, it slows down. FR-4 is about half the speed of light, or 6 inches per nanosecond.
- The glass epoxy material (FR-4) commonly used for PCBs has a negligible loss for digital applications below 1 GHz. But at higher frequencies, the loss is of greater concern.
- A lower Dk material is desirable for high-speed design. Conversely, a high Dk material is very good at condensing electric fields, so having it between the planes increases planar capacitance.
- The dielectric constant (Dk) is the amount of electromagnetic energy stored in a material by an applied voltage.
- The dissipation factor (Df) quantifies a material’s inherent dissipation of electromagnetic energy.
- Conduction loss is the flow of charge through the material that causes energy dissipation.
- Dielectric loss is the dissipation of energy through the movement of charges in an alternating electromagnetic field as polarization switches direction.
- Dielectric loss is especially high around the resonant frequencies, causing an interaction between the field and the dielectric’s polarization that results in heating.
- A material with a low Dk has a low Df, a high Tg, and a high Td, which is required for high-speed design.
- Matching material performance numbers of the dielectric constant is important. A small difference in the value between materials can impact impedance, line widths/clearances, and thus losses, significantly.
- The Dk determines the propagation velocity of the signal in the medium. If Dk values vary on different layers of the substrate, then bus signal timing may also be an issue.
Resources
Beyond Design columns by Barry Olney:
- Material Selection for SERDES Design
- Material Selection for Digital Design
- It’s a Material World
This column originally appeared in the May 2023 issue of Design007 Magazine.
More Columns from Beyond Design
Beyond Design: Effective Floor Planning StrategiesBeyond Design: Refining Design Constraints
Beyond Design: The Metamorphosis of the PCB Router
Beyond Design: Radiation and Interference Coupling
Beyond Design: Key SI Considerations for High-speed PCB Design
Beyond Design: Electro-optical Circuit Boards
Beyond Design: AI-driven Inverse Stackup Optimization
Beyond Design: High-speed Rules of Thumb