-
- News
- Books
Featured Books
- pcb007 Magazine
Latest Issues
Current IssueSales: From Pitch to PO
From the first cold call to finally receiving that first purchase order, the July PCB007 Magazine breaks down some critical parts of the sales stack. To up your sales game, read on!
The Hole Truth: Via Integrity in an HDI World
From the drilled hole to registration across multiple sequential lamination cycles, to the quality of your copper plating, via reliability in an HDI world is becoming an ever-greater challenge. This month we look at “The Hole Truth,” from creating the “perfect” via to how you can assure via quality and reliability, the first time, every time.
In Pursuit of Perfection: Defect Reduction
For bare PCB board fabrication, defect reduction is a critical aspect of a company's bottom line profitability. In this issue, we examine how imaging, etching, and plating processes can provide information and insight into reducing defects and increasing yields.
- Articles
- Columns
- Links
- Media kit
||| MENU - pcb007 Magazine
Estimated reading time: 3 minutes
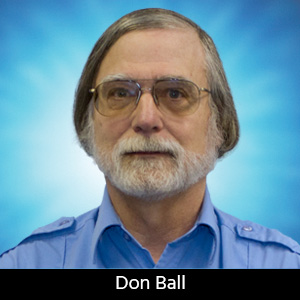
The Chemical Connection: The Challenges of Thin Material Transport
In wet processing, the transport of thin materials and substrates (less than 1 mil thick) can be a rather tricky process. These materials are vital in manufacturing flexible circuits, but often this flexibility adds new challenges. Most of these materials are easily damaged, and in some cases require well-trained personnel to handle them. You would think that this could be easily remedied with conveyorized equipment, but it is not entirely the case. Transporting thin materials through a conveyor aids the process to a degree, but once you get to the wet-processing stages—cleaning, developing, etching, and stripping—there are risks for error if you do not have the right tools or equipment.
Thin material transport in wet processing is challenging because, for it to perform, the conveyor needs to have open spaces. In PCB fabrication, the goal of all wet processes is to have a liquid interact with the surface of your product. Most often, this is done with spraying. If you want interaction from both top and bottom sides of the PCB, there must be gaps for that spray to come through and reach the product. If the conveyor were a simple, flat conveyor belt that pulled the board through, you could make the product go from one end of the conveyor to the other, but it would receive no etching on the bottom side. Even if the belt were porous, this would still leave shadow marks behind, because the point of contact between the board and the conveyor would remain the same throughout the process. The conveyor needs enough gaps in the bottom side, and it also needs to change points where it touches the board. That is why wet-processing conveyors are designed this way today (Figure 1).
Gaps are required to conduct normal wet processing, which creates some difficulties. Any gap in the conveyor provides a chance for a corner to dip downward. The thinner the material, the more likely this will happen, especially when a liquid is sprayed onto the top of it. When this happens, it can cause that edge or corner to fold or “crinkle.” This happens because of the uneven movement among all parts of the panel. Once a corner drops down into a gap, that part of the board loses velocity in the forward direction, while the rest of the board keeps a consistent forward velocity as the conveyor moves along.
The Leader Method
Although these complications can be a significant obstacle, they do not stop flex PCB manufacturers from using wet processes. The leader method has been commonly used for many years. With it, a rigid board is taped (using chemically resistant tape) to the leading edge of the thin material that needs to undergo a wet process. This ensures that the leading edges of the flexible circuit do not drop into a gap and thus form an error. Since this drooping issue is the main problem of thin material transport, the method tends to provide consistent results. Despite this, most manufacturers of flexible circuits want to get away from using leaders because of the manual labor needed to apply and remove the tape. The process takes time and is prone to human error, which creates further potential for panels to get damaged.
The Leaderless Approach
If leaders are not desired, the next solution must come from the conveyor design. Frequently, the solution is to provide greater conveyor density—meaning fewer gaps in the conveyor and less likelihood for an error to occur. The main downside is that the etch rate on the bottom side can be inhibited by the conveyor since it is harder for spray to reach the panel.
Surface tension is another issue that comes with leaderless transport of thin materials. Often in wet processing equipment, rollers ensure the chemicals in each wet processing section are contained within their modules and don’t leak into other modules. Sometimes with thin material, the liquid on the panel creates enough surface tension to cause the panel to stick to the rollers and wrap around it. To avoid this, use either lightweight rollers or rollers with reduced surface area.
Conclusion
If you wish to move away from using the leader method, know that wet processing of thin materials and substrates is a complex process that requires specialized equipment. While specialized equipment can aid in the transportation of these materials, it is not enough to guarantee error-free wet processing. Although there are some restrictions, I foresee leaderless thin material transport soon becoming an issue of the past.
This column originally appeared in the May 2023 issue of PCB007 Magazine.
More Columns from The Chemical Connection
The Chemical Connection: Through-glass Vias in Glass SubstratesThe Chemical Connection: Reducing Defects in Circuit Board Production
The Chemical Connection: Common Misconceptions in Wet Processing
The Chemical Connection: Surface Finishes for PCBs
The Chemical Connection: Earthquakes, Astronauts, and Aquatics—A Lighter Look at the Past
The Chemical Connection: Better Fabs Attract a Better Workforce
The Chemical Connection: Can Changing Spray Nozzles Improve My Etch Quality?
The Chemical Connection: Getting the Best from Your Cupric Chloride Etchant