-
- News
- Books
Featured Books
- design007 Magazine
Latest Issues
Current IssueAll About That Route
Most designers favor manual routing, but today's interactive autorouters may be changing designers' minds by allowing users more direct control. In this issue, our expert contributors discuss a variety of manual and autorouting strategies.
Creating the Ideal Data Package
Why is it so difficult to create the ideal data package? Many of these simple errors can be alleviated by paying attention to detail—and knowing what issues to look out for. So, this month, our experts weigh in on the best practices for creating the ideal design data package for your design.
Designing Through the Noise
Our experts discuss the constantly evolving world of RF design, including the many tradeoffs, material considerations, and design tips and techniques that designers and design engineers need to know to succeed in this high-frequency realm.
- Articles
- Columns
- Links
- Media kit
||| MENU - design007 Magazine
Sustainably Clean
June 8, 2023 | Barry Matties, I-Connect007Estimated reading time: 4 minutes
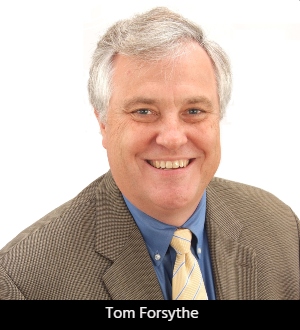
As the definition of sustainability evolves in the industry, one thing is clear: Process control plays a large role in any definition. Creating a stable process reduces the potential overuse of cleaning materials and it increases yields, thereby reducing scrap and helping the sustainability effort. I recently spoke with Tom Forsythe, executive vice president of KYZEN, about the cleaning process and automated bath control.
Barry Matties: Tom, what has my attention once again are your process control systems for the cleaning process. I’m sure you have installed hundreds of these since I first learned about it a few years ago.
Tom Forsythe: Yes, we have. Years ago, when sophisticated aqueous cleaning was born, it required the aqueous cleaning machines of the day to evolve, which meant a need to control a blend of two things—cleaning materials and water. That was a new concept. We all do it at home when we wash the dishes, but it was new for the industry. We originally developed those automated control systems because our customers were having a difficult time keeping their process operating properly.
Matties: Without automated control and the water coming in and out, it can easily go from a stable to an unstable process or outside control limits in a matter of hours.
Forsythe: It’s interesting because it shows the difference in dynamics between batch and inline cleaners. Batch systems, for the most part, are very self-contained—they wash, rinse, and dry in the same chamber—but they don't turn on the exhaust until they're doing the drying. Those tend to be much more stable. They don't drift much, and it’s a very gradual change over days.
Inline systems have air knives at the end of the wash section to “scrape off” the cleaning material for continued use. That's a value-adder and good for the customer. But now I'm pumping in a few hundred CFM of air with that air knife. What goes in must come out. It would compromise drying if all that moist air were to come out the drying end. Of course, we don't want a cloud of exhaust coming out the input end either. So, the inline system wash chamber dynamics of the spray action is somewhere between 40 and 100 PSI (actually doing the washing), and proper exhaust to balance out that air knife input gets you a very dynamic environment. You can be out of your desired constraints in less than an hour.
Those automated control systems are worth their weight in gold. More importantly, beyond the substantial chemical savings, you get a rock-solid process. If you’re supposed to be at 10% or 12%, you’re at 10, not at 11% or 14%; and the corrections are small, not large, gross adjustments. It’s kind of like driving your car down a straight highway, lightly touching the steering wheel as you move it back and forth a little bit. The adjustments are quite modest, but it's a big part of reduced consumption and a better process that delivers quality operations.
Matties: What trends do you see? Are people looking for the inline or batch process, or is it still application specific?
Forsythe: It tends to be driven by the tempo in the individual shops. What percentage of your production requires cleaning? This is not about using no-clean technology, but whether your clients require their assemblies to be cleaned. It is worth remembering that no-clean is actually the only modern technology. Barry, what is your guess about how much R&D money has gone into a solder paste that’s not named no-clean in this century?
Matties: I’m guessing it’s a fairly small number, yes?
Forsythe: Everyone, whether they clean or not, uses no-cleans because solder technology has improved this century. It performs better and has a better user experience due to the great features the solder developers have invented and brought to market. But it's a case of who chooses to clean and how much of their production requires cleaning. For example, the aerospace segment never really stopped cleaning but isn’t known as a high-volume crowd. They tend to be more batch oriented. Medical devices are changing. Many have gone mass market, such as diabetes implants and other devices employing all kinds of sensors. Those are more often high volume and inline-oriented, but they can still be cleaned in batch systems. The military tends to like inlines, but they also use many batch cleaners.
It's really a function of what you do. Contract manufacturers often use inlines because, of course, they’re about bundling business together to gain volume efficiencies. It's not really about any particular contract, but about what the “portfolio” looks like. They tend to be inline guys, but it varies depending on their basic capacity needs. On the performance side, both batch and inline can provide the same level of cleaning for most PCBs. There are particular days where one may do a better job than the other, but on average it's a fielder's choice.
Continue reading this interview in the June issue of SMT007 Magazine.
Suggested Items
Driving Innovation: Direct Imaging vs. Conventional Exposure
07/01/2025 | Simon Khesin -- Column: Driving InnovationMy first camera used Kodak film. I even experimented with developing photos in the bathroom, though I usually dropped the film off at a Kodak center and received the prints two weeks later, only to discover that some images were out of focus or poorly framed. Today, every smartphone contains a high-quality camera capable of producing stunning images instantly.
Hands-On Demos Now Available for Apollo Seiko’s EF and AF Selective Soldering Lines
06/30/2025 | Apollo SeikoApollo Seiko, a leading innovator in soldering technology, is excited to spotlight its expanded lineup of EF and AF Series Selective Soldering Systems, now available for live demonstrations in its newly dedicated demo room.
Indium Corporation Expert to Present on Automotive and Industrial Solder Bonding Solutions at Global Electronics Association Workshop
06/26/2025 | IndiumIndium Corporation Principal Engineer, Advanced Materials, Andy Mackie, Ph.D., MSc, will deliver a technical presentation on innovative solder bonding solutions for automotive and industrial applications at the Global Electronics A
Fresh PCB Concepts: Assembly Challenges with Micro Components and Standard Solder Mask Practices
06/26/2025 | Team NCAB -- Column: Fresh PCB ConceptsMicro components have redefined what is possible in PCB design. With package sizes like 01005 and 0201 becoming more common in high-density layouts, designers are now expected to pack more performance into smaller spaces than ever before. While these advancements support miniaturization and functionality, they introduce new assembly challenges, particularly with traditional solder mask and legend application processes.
Knocking Down the Bone Pile: Tin Whisker Mitigation in Aerospace Applications, Part 3
06/25/2025 | Nash Bell -- Column: Knocking Down the Bone PileTin whiskers are slender, hair-like metallic growths that can develop on the surface of tin-plated electronic components. Typically measuring a few micrometers in diameter and growing several millimeters in length, they form through an electrochemical process influenced by environmental factors such as temperature variations, mechanical or compressive stress, and the aging of solder alloys.