-
- News
- Books
Featured Books
- smt007 Magazine
Latest Issues
Current IssueSupply Chain Strategies
A successful brand is built on strong customer relationships—anchored by a well-orchestrated supply chain at its core. This month, we look at how managing your supply chain directly influences customer perception.
What's Your Sweet Spot?
Are you in a niche that’s growing or shrinking? Is it time to reassess and refocus? We spotlight companies thriving by redefining or reinforcing their niche. What are their insights?
Moving Forward With Confidence
In this issue, we focus on sales and quoting, workforce training, new IPC leadership in the U.S. and Canada, the effects of tariffs, CFX standards, and much more—all designed to provide perspective as you move through the cloud bank of today's shifting economic market.
- Articles
- Columns
- Links
- Media kit
||| MENU - smt007 Magazine
Sustainably Clean
June 8, 2023 | Barry Matties, I-Connect007Estimated reading time: 4 minutes
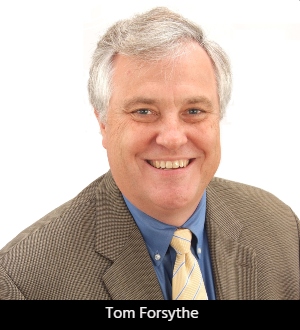
As the definition of sustainability evolves in the industry, one thing is clear: Process control plays a large role in any definition. Creating a stable process reduces the potential overuse of cleaning materials and it increases yields, thereby reducing scrap and helping the sustainability effort. I recently spoke with Tom Forsythe, executive vice president of KYZEN, about the cleaning process and automated bath control.
Barry Matties: Tom, what has my attention once again are your process control systems for the cleaning process. I’m sure you have installed hundreds of these since I first learned about it a few years ago.
Tom Forsythe: Yes, we have. Years ago, when sophisticated aqueous cleaning was born, it required the aqueous cleaning machines of the day to evolve, which meant a need to control a blend of two things—cleaning materials and water. That was a new concept. We all do it at home when we wash the dishes, but it was new for the industry. We originally developed those automated control systems because our customers were having a difficult time keeping their process operating properly.
Matties: Without automated control and the water coming in and out, it can easily go from a stable to an unstable process or outside control limits in a matter of hours.
Forsythe: It’s interesting because it shows the difference in dynamics between batch and inline cleaners. Batch systems, for the most part, are very self-contained—they wash, rinse, and dry in the same chamber—but they don't turn on the exhaust until they're doing the drying. Those tend to be much more stable. They don't drift much, and it’s a very gradual change over days.
Inline systems have air knives at the end of the wash section to “scrape off” the cleaning material for continued use. That's a value-adder and good for the customer. But now I'm pumping in a few hundred CFM of air with that air knife. What goes in must come out. It would compromise drying if all that moist air were to come out the drying end. Of course, we don't want a cloud of exhaust coming out the input end either. So, the inline system wash chamber dynamics of the spray action is somewhere between 40 and 100 PSI (actually doing the washing), and proper exhaust to balance out that air knife input gets you a very dynamic environment. You can be out of your desired constraints in less than an hour.
Those automated control systems are worth their weight in gold. More importantly, beyond the substantial chemical savings, you get a rock-solid process. If you’re supposed to be at 10% or 12%, you’re at 10, not at 11% or 14%; and the corrections are small, not large, gross adjustments. It’s kind of like driving your car down a straight highway, lightly touching the steering wheel as you move it back and forth a little bit. The adjustments are quite modest, but it's a big part of reduced consumption and a better process that delivers quality operations.
Matties: What trends do you see? Are people looking for the inline or batch process, or is it still application specific?
Forsythe: It tends to be driven by the tempo in the individual shops. What percentage of your production requires cleaning? This is not about using no-clean technology, but whether your clients require their assemblies to be cleaned. It is worth remembering that no-clean is actually the only modern technology. Barry, what is your guess about how much R&D money has gone into a solder paste that’s not named no-clean in this century?
Matties: I’m guessing it’s a fairly small number, yes?
Forsythe: Everyone, whether they clean or not, uses no-cleans because solder technology has improved this century. It performs better and has a better user experience due to the great features the solder developers have invented and brought to market. But it's a case of who chooses to clean and how much of their production requires cleaning. For example, the aerospace segment never really stopped cleaning but isn’t known as a high-volume crowd. They tend to be more batch oriented. Medical devices are changing. Many have gone mass market, such as diabetes implants and other devices employing all kinds of sensors. Those are more often high volume and inline-oriented, but they can still be cleaned in batch systems. The military tends to like inlines, but they also use many batch cleaners.
It's really a function of what you do. Contract manufacturers often use inlines because, of course, they’re about bundling business together to gain volume efficiencies. It's not really about any particular contract, but about what the “portfolio” looks like. They tend to be inline guys, but it varies depending on their basic capacity needs. On the performance side, both batch and inline can provide the same level of cleaning for most PCBs. There are particular days where one may do a better job than the other, but on average it's a fielder's choice.
Continue reading this interview in the June issue of SMT007 Magazine.
Testimonial
"The I-Connect007 team is outstanding—kind, responsive, and a true marketing partner. Their design team created fresh, eye-catching ads, and their editorial support polished our content to let our brand shine. Thank you all! "
Sweeney Ng - CEE PCBSuggested Items
Indium Corporation Promotes Two Leaders in EMEA (Europe, Middle East, and Africa) Markets
08/05/2025 | Indium CorporationWith its commitment to innovation and growth through employee development, Indium Corporation today announced the promotions of Andy Seager to Associate Director, Continental Sales (EMEA), and Karthik Vijay to Senior Technical Manager (EMEA). These advancements reflect their contributions to the company’s continued innovative efforts with customers across Europe, the Middle East, and Africa (EMEA).
MacDermid Alpha Electronics Solutions Unveils Unified Global Website to Deepen Customer, Talent, and Stakeholder Engagement
07/31/2025 | MacDermid Alpha Electronics SolutionsMacDermid Alpha Electronics Solutions, the electronics business of Elements Solutions Inc, today launched macdermidalpha.com - a unified global website built to deepen digital engagement. The launch marks a significant milestone in the business’ ongoing commitment to delivering more meaningful, interactive, and impactful experiences for its customers, talent, and stakeholders worldwide.
KOKI to Showcase Analytical Services and New HF1200 Solder Paste at SMTA Guadalajara 2025
07/31/2025 | KOKIKOKI, a global leader in advanced soldering materials and process optimization services, will exhibit at the SMTA Guadalajara Expo & Tech Forum, taking place September 17 & 18, 2025 at Expo Guadalajara, Salón Jalisco Halls D & E in Guadalajara, Mexico.
Weller Tools Supports Future Talent with Exclusive Donation to SMTA Michigan Student Soldering Competition
07/23/2025 | Weller ToolsWeller Tools, the industry leader in hand soldering solutions, is proud to announce its support of the upcoming SMTA Michigan Expo & Tech Forum by donating a limited-edition 80th Anniversary Black Soldering Set to the event’s student soldering competition.
Koh Young Appoints Tom Hattori as President of Koh Young Japan
07/21/2025 | Koh YoungKoh Young Technology, the global leader in True 3D measurement-based inspection solutions, announced the appointment of Tom Hattori as President of Koh Young Japan (JKY).