-
- News
- Books
Featured Books
- design007 Magazine
Latest Issues
Current IssueAll About That Route
Most designers favor manual routing, but today's interactive autorouters may be changing designers' minds by allowing users more direct control. In this issue, our expert contributors discuss a variety of manual and autorouting strategies.
Creating the Ideal Data Package
Why is it so difficult to create the ideal data package? Many of these simple errors can be alleviated by paying attention to detail—and knowing what issues to look out for. So, this month, our experts weigh in on the best practices for creating the ideal design data package for your design.
Designing Through the Noise
Our experts discuss the constantly evolving world of RF design, including the many tradeoffs, material considerations, and design tips and techniques that designers and design engineers need to know to succeed in this high-frequency realm.
- Articles
- Columns
- Links
- Media kit
||| MENU - design007 Magazine
EIPC Summer Conference 2023: Day 1 Review
June 28, 2023 | Pete Starkey, I-Connect007Estimated reading time: 14 minutes
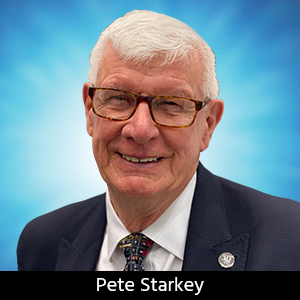
Mid-morning on June 15 in Munich, after the conclusion of an informative and thought-provoking keynote session, the EIPC Summer Conference got under way with a series of presentations on Smart manufacturing, introduced and moderated by EIPC board member Dr. Michele Stampanoni, vice president strategic sales and business development at Cicor Group.
Data Management Systems
Andre Bodegom, managing director of Adeon Technologies, discussed data management systems for real-time integration of design- and production-generated process results for yield improvement and quality control.
Typically, the PCB fabricator receives design information in Gerber plot format, an old-fashioned flat data format without much in the way of intelligence, together with a whole list of specifications the customer expects to be realised in the delivered product. From the flat data supplied, the fabricator is required to build up a lot of intelligence: stackup, material library, alignment, design rule checking, design for manufacturability, panelisation, etc. From this more intelligent database, the fabricator creates outputs for various equipment: direct imager, drilling machine, electrical tester, optical inspection system, etc. All this equipment itself generates data.
“What to do with this data?” Bodegom asked. “Basically not much, unless we have a problem, by which time it’s too late.”
AOI machines generate a large amount of data, and Adeon has cooperated with a major equipment supplier to develop a method of analysing the data and converting it to enable usable proactive correction. He described a continuous quality improvement cycle: real-time monitoring and continuous quality data collection, real-time review and analysis of quality issues, immediate corrective action on the faulty process, and implementation of preventative action to achieve long term quality improvement goals.
Bodegom went into detail about how artificial intelligence can be integrated to assist in detecting common equipment issues based on defect distribution patterns, identifying quality issues across multiple processes with complex interdependencies, and predicting the optimal process route and conditions for a specific job type.
A related development is the facility to dynamically generate an integrated data management solution from multi-stage data by pulling together quality maps from multiple vendors into one aggregated eMap, with real-time data collection and automated generation of a comprehensive standard eMap without manual data manipulation.
Bodegom illustrated the workflow as a data pipeline with unified interface communication protocols and data formats for data exchange. The new data is continuously merged with the upstream process data to update the eMap on the central database and the system offers accumulated productivity and efficiency savings along the entire process sequence.
Digital Twin in Copper Electroplating Processes
Dr. Ing. Agnieszka Franczak, specialist in electrochemical surface treatment and corrosion with Elsyca, gave a knowledgeable and detailed presentation on the digital twin concept in copper electroplating processes for better process control and superior metal finish.
She began by clarifying her terminology, defining “digital twin” as a representation of a real-world system or process, reflecting its actual physical setup and performance, using real-world reference data to predict performance outcomes and issues so that an optimized system or process can be designed in a safe and short turnaround. She identified electroplating as an electrochemical process that produces a metallic coating on a substrate material through the reduction of cations present in the electrolyte by means of a direct electric current.
Franczak discussed electroplating process performance assessment through a digital twin concept in the context of Industry 4.0 principles, where end-to-end engineering optimization was achieved through leveraging insights gained from mixed reality and data from process digital twin interactions to simulate design changes and continuously improve production quality and plant performance.
The digital twin concept enables manufacturers to connect internal processes virtually and to work simultaneously on physical and virtual models to make changes. It is easily immersed into processes across supply chains and enabled product engineers to use mixed reality to experience how products work in operation.
In the case of PCB copper electroplating, Franczak gathered comprehensive plating bath information, details of plating tank infrastructure, electrolyte attributes, process parameters and job data. It was necessary to recognise the electrochemical performance of the plating bath, as well as bath conductivity and process efficiency, so that better process control can be achieved. The electrochemical behaviour is represented by the polarization data, expressed as current density-voltage curves, gathered during lab experiments. She demonstrated graphically the influence of bath agitation on the electrochemical response, and the effect of current distribution on deposit thickness. The digital twin concept enables predictive modelling and simulation of current density distribution and consequent copper metal thickness distribution. Upfront plateability analysis facilitates the design of a fit-for-purpose mitigation plan and the validation of an improved process strategy.
Wastewater Recycling
Always an inspirational presenter at EIPC conferences, factory automation pioneer and innovator Alex Stepinski, one of whose many areas of expertise is wastewater recycling, gave a guide to converting existing European PCB fabrication facilities to 100% zero liquid discharge green processing. Recent developments in recycling system design from larger-scale green-field projects in the U.S. have created new opportunities for economical upgrade of European wastewater treatment facilities, and Stepinski is prepared to offer assistance on a not-for-profit basis with the objective of getting rid of waste.
He described the overall system, having already proven in practice that only 0.2–1.0 cubic metres of water per day is needed for up to hundreds of panels per hour of PCB production.
An advanced oxidation process is used to remove organics and break chelates, then settlers and filters remove metal hydroxides and other suspended solids. A membrane system recovers 99% of the liquid as ultra-pure de-ionised water and the remaining 1% is recovered by vacuum distillation which leaves a solid sludge. A de-watering system recovers dissolved metals and can be broken up into smaller units to also recover individual metals for higher resale value.
Stepinski explained in detail each stage of the process: The latest advanced oxidation process technology can remove all residual organics from PCB operations at an average cost per cubic metre of 50 cents to $1 when operating full closed loop production. The organics are broken down into CO2 which may also be re-captured if desired. The state-of-the-art utilises hydrogen peroxide electrolysis plus UV, with no chemicals needed. The total suspended solids removal system consists of a traditional clarifier and sand filter process. The membrane system utilises multiple-pass reverse osmosis together with electro-deionisation, a continuous, chemical-free process, and electrodialysis. Vacuum distillation is the key step that closes the loop. A sealed vessel contains an auger that converts the final concentrate to a concrete-like sludge under high-temperature vacuum, while the distillate is recovered back to the advanced oxidation process and reprocessed as a normal dirty rinse-water. Sludge de-watering can be automated with centrifuges.
He reported that systems have been deployed across four new factories in the U.S. over the past five years and have passed U.S. EPA audits. As of May 2023, the first projects in Europe and Asia are underway. He estimated that total system CAPEX and 10 years’ maintenance will be covered by three to 10 years of OPEX savings without EU funding.
Advanced Packaging
“Advanced automated systems for fine line and space requirements in HDI and package substrates” was the title of the joint presentation from Andreas Schatz and Dirk Ruess, global product managers for equipment with MKS-Atotech.
Their illustration of market trends indicates that the packaging substrate share of the PCB market will continue to grow. Ruess discussed technology trends in high density interconnect and substrate-like PCB, as lines and spaces trend to the 15-micron level from mSAP through amSAP to amSAP embedded trace, and described the MKS-Atotech equipment portfolio, classified by production technology. He listed the general benefits of continuous transport systems, particularly regarding consistency and improved uniformity.
Schatz commented in detail about horizontal equipment for advanced HDIs and ICs, which offers reliable thin-panel transportation, uniform, stable and effective fluid performance, chemistry monitoring and control, and particle avoidance. The reduced footprint minimizes consumption of resources and the intelligent usage of process and production data enabled smart production.
Ruess discussed the alternative vertical system with continuous transportation for electrolytic copper processing, which he considers the best option for advanced HDI and IC substrate production. With a high level of automation, the system offers excellent thin-panel capability with high throwing power, superior distribution, and good through-hole filling.
Atotech’s ability to supply a complete package of equipment and chemistry facilitated optimisation of the process for advanced HDI and IC substrate technologies and the new industrial digital solutions in its Digital Factory Suite provides increased operating efficiency, reduced unplanned downtime, increased quality, reduced scrap, and optimised energy consumption.
Page 1 of 3
Suggested Items
The Evolution of Picosecond Laser Drilling
06/19/2025 | Marcy LaRont, PCB007 MagazineIs it hard to imagine a single laser pulse reduced not only from nanoseconds to picoseconds in its pulse duration, but even to femtoseconds? Well, buckle up because it seems we are there. In this interview, Dr. Stefan Rung, technical director of laser machines at Schmoll Maschinen GmbH, traces the technology trajectory of the laser drill from the CO2 laser to cutting-edge picosecond and hybrid laser drilling systems, highlighting the benefits and limitations of each method, and demonstrating how laser innovations are shaping the future of PCB fabrication.
Day 2: More Cutting-edge Insights at the EIPC Summer Conference
06/18/2025 | Pete Starkey, I-Connect007The European Institute for the PCB Community (EIPC) summer conference took place this year in Edinburgh, Scotland, June 3-4. This is the third of three articles on the conference. The other two cover Day 1’s sessions and the opening keynote speech. Below is a recap of the second day’s sessions.
Day 1: Cutting Edge Insights at the EIPC Summer Conference
06/17/2025 | Pete Starkey, I-Connect007The European Institute for the PCB Community (EIPC) Summer Conference took place this year in Edinburgh, Scotland, June 3-4. This is the second of three articles on the conference. The other two cover the keynote speeches and Day 2 of the technical conference. Below is a recap of the first day’s sessions.
Preventing Surface Prep Defects and Ensuring Reliability
06/10/2025 | Marcy LaRont, PCB007 MagazineIn printed circuit board (PCB) fabrication, surface preparation is a critical process that ensures strong adhesion, reliable plating, and long-term product performance. Without proper surface treatment, manufacturers may encounter defects such as delamination, poor solder mask adhesion, and plating failures. This article examines key surface preparation techniques, common defects resulting from improper processes, and real-world case studies that illustrate best practices.
RF PCB Design Tips and Tricks
05/08/2025 | Cherie Litson, EPTAC MIT CID/CID+There are many great books, videos, and information online about designing PCBs for RF circuits. A few of my favorite RF sources are Hans Rosenberg, Stephen Chavez, and Rick Hartley, but there are many more. These PCB design engineers have a very good perspective on what it takes to take an RF design from schematic concept to PCB layout.