-
- News
- Books
Featured Books
- smt007 Magazine
Latest Issues
Current IssueMoving Forward With Confidence
In this issue, we focus on sales and quoting, workforce training, new IPC leadership in the U.S. and Canada, the effects of tariffs, CFX standards, and much more—all designed to provide perspective as you move through the cloud bank of today's shifting economic market.
Intelligent Test and Inspection
Are you ready to explore the cutting-edge advancements shaping the electronics manufacturing industry? The May 2025 issue of SMT007 Magazine is packed with insights, innovations, and expert perspectives that you won’t want to miss.
Do You Have X-ray Vision?
Has X-ray’s time finally come in electronics manufacturing? Join us in this issue of SMT007 Magazine, where we answer this question and others to bring more efficiency to your bottom line.
- Articles
- Columns
- Links
- Media kit
||| MENU - smt007 Magazine
Estimated reading time: 7 minutes
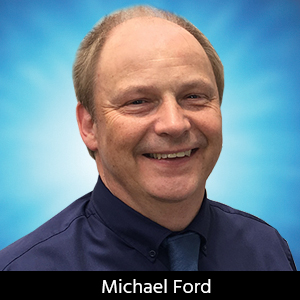
Smart Factory Insights: Machines, People, and AI
Aspiring Smart factories seem to care, perhaps a little too much, about the differential effects of automation vs. people vs. AI. Rather than obsessing over the differences, let’s focus on what they all share, since our Smart manufacturing operations require all three to work together in harmony, combining their strengths as they support our business goals.
It seems ironic that since automation was first introduced for mass production, we have since been trying to create machines and supervisory software solutions that work more like the people that it replaced. The “people model” has endured because it has been more adept to the needs of modern manufacturing profiles of lower volume and higher mix of production. Both manual and automated production approaches share many common core principles and requirements in the Smart factory. In respecting this commonality as part of a holistic manufacturing execution software (MES) solution, we create a new level of flexibility and agility, and avoid accruing losses related to continuous change.
A key but little discussed principle of Smart manufacturing is to break down the assumption that we need separate “islands” of automated and manual assembly. Using production storage space and resources to manage sub-assembly work-in-progress, “thrown over the wall” between islands of processing, is not conducive to agility, optimization, or efficient factory utilization.
If you are not convinced, simply look at the value of materials in your typical buffer-stock locations, as well as the costs of how that space and content needs to be managed, complexities of revision control, first-in/first-out management, and how product quality deteriorates with additional handling and the gathering of dust. Also consider the delay in feedback should any prior process or material that has been used end up contributing to defects. This creates performing very significant re-work overhead without notice. Balancing costs of shift work vs. asset utilization has always been approached through the simplification of segregation without really thinking through the associated consequences and difficulties. This waste becomes more significant today as we embrace the need for efficiencies in low-volume/high-mix environments where such hidden losses, once tolerable, are now crippling the business.
Supporting the Change
This need for change in perspective is being supported by advances in manufacturing technology. We are already familiar with the integration of manual, automated, and semi-automated operations, such as the use of cobots and production stations where data from tools and measurement devices is automatically collected. Digital integration across manufacturing has become a reality, requiring an end-to-end approach that does not discriminate among people, automation, and AI.
There is a required confidence in deciding how to bring separated manufacturing operations together—those that have been perceived to work with different technologies or simply exist on a different level of an ERP bill of materials (BOM). Today, this is much easier to realize. Information in the right digital format fuels changes that go far beyond the simple automation of manual processes. The use of CAD data, digital product models, digital twins—or whatever the buzzword of the day is—now levels the playing field in terms of manufacturing operation data preparation, work assignment, operational visibility, control, and coordination across all production stations. This could be people-driven, automated, or somewhere in between. Let’s break it down.
Prepare the Relevant Production Information
The first step in getting a production work-order going is to prepare the relevant product information. This comes mainly from design and the BOM. Traditionally, engineering makes the key decision as to which production configuration will be used. Then, depending on the chosen configuration capabilities, the product data is divided up among the separate engineering teams. The assignment is then fixed, as each engineering team prepares their data for either machine programming or manual assembly. This process involves a great deal of manual data manipulation and very little opportunity for flexibility. Data must be combined, separated, and converted into the various formats required for each production station. This often requires bespoke data formatting to depend on the machine vendor, or documentation tools that create drawings and work instructions for operators. Each team independently assesses the most efficient sequence of work. This leads to unbalanced production rates and sub-assembly storage requirements. You then need a very significant amount of work, including depending on specialist knowledge within each team.
How a Smart Factory Differs
Achieving the same result in a Smart factory is significantly different. All production operations are driven by information that comes from the design digitally, potentially comprised of a PCB layout, a 3D CAD model of the product for discrete assembly, 3D representations of materials used, and BOM data derived from ERP and/or PLM solutions—all in an electronic format.
Automation within the modern digital manufacturing engineering (DME) tool is a crucial part of a modern Smart manufacturing software solution. The combination of CAD and BOM data allows automated allocation of work, and creation of the specific types of data required for each manufacturing station. For machines, specific data formats and sequences are prepared automatically with the knowledge and know-how of each machine requirement. For manual assembly and semi-automated stations, a complex set of interactive electronic work instructions is created through operational steps following pre-composed templates.
From the user perspective, this is a simple and almost totally automated process (where suitable source data is available), as there are complex AI algorithms working within the software that replace critical dependencies on engineering “deep dive” niche skills. The whole engineering process becomes much more flexible. Rather than having to fix a product allocation to a target production configuration, such decisions can now happen as a reaction to real production demand using configurations that best fit the end-to-end balance of production capabilities and prior work-order progress.
Operations planned adaptively in this way far exceed the efficiency of those planned by traditional methods. The use of DME in a Smart factory reduces lead-time, eliminates mistakes, and provides an unprecedented ability for the flexibility and agility needed for high-mix production, all the way up to the automation of single pieces.
Once information has been prepared for the production station, setup and preparation can start. For both manual and automated stations, verification of materials, tools, and incoming product is essential for production to execute correctly. In the traditional factory, this is done by manual confirmation, which ironically introduces the potential for mistakes. In our Smart factory, all the data is prepared such that verification can be automated using, for example, Smart feeders or semi-automatically using bar codes. Setup times can be greatly reduced through this automation, which significantly reduces the productivity impact of high-mix manufacturing.
Once the work order is started, automation should rigorously follow its programming. Exceptions often happen, so it’s essential to have a real-time connection with the station to provide visibility and control of the operation. To understand the root causes of issues, there is traditionally a dependency on manual measurements and data recording. But this is almost impossible for an operator or engineer running a machine at high speed. In the Smart factory, key facts and data points related to run-time progress or issues are analyzed in context with the prepared “digital twin” of the verified product and setup. This reveals a wide variety of information used to further refine productivity, quality, and maintenance. The IPC-CFX standard has become the popular solution of choice, as a “plug and play” IIoT connection for such communication purposes. Smart factory AIs collect and contextualize data. This provides information which engineers can use to orchestrate any supporting or corrective actions that may be required.
A Different Kind of ‘Interface’
The same paradigms I’ve detailed are used for automation and are relevant for manual assembly operations which represent a different kind of “interface” to gather data. Rather than using traditional work instructions as a reference, electronic work instructions are interactive, conduct the active operation, and detail step-by-step activities throughout. Data is collected and confirmed, such as the start and end times of each task and activity, as well as exceptions that may occur, all in a way that the operator can qualify and contextualize. One example is the consumption and spoilage data of materials, which allows for Lean material management and quality data for analysis. Smart tools, such as torque wrenches, electronic rulers, scales, etc., that are being integrated into the operation then automate that collection of measurement data. Manual assembly operations become as “smart” as automated processes. AI-based analytics gain the same qualified information from manual assembly stations as from automated.
Use and analysis of contextualized Smart factory data becomes common across the whole manufacturing floor. Functionalities and benefits of Lean material management, active quality, and adaptive planning are applied in a comparable and interoperable way. Advanced AI-based analytics have the same opportunity to provide insight and assessment of opportunities for improvement, and reaction to challenges, be they restrictive or opportunistic.
The de facto rule of manufacturing quality has always been that if a human “touch” is involved, there will be defects. This rule applies ubiquitously around manufacturing. With the automation of data collection, there is uniformity in contextualization, treating all stations as equals, visibility, reaction, and control; the human touch is taken out of situation assessment and focused on actions and outcomes. Manufacturing becomes more dynamic and controllable, with reduced dependencies on deep-dive skills. This reduces downtime and increases productivity and quality.
Machines, people, and AI have, for some time and will always now be, elements in our manufacturing equation. Let’s have them work together in harmony, to deliver our best business results.
This column originally appeared in the July 2023 issue of SMT007 Magazine.
More Columns from Smart Factory Insights
Smart Factory Insights: Making Rework a Smart Business OpportunitySmart Factory Insights: The Sustainability Gold Rush
Smart Factory Insights: Today’s Manufacturing Jobs Require a New Skill Set
Smart Factory Insights: Compose Yourself, Mr. Ford
Smart Factory Insights: The Smart Business Case for Local PCB Manufacturing
Smart Factory Insights: Manufacturing Digital Twin—Spanners in the Works
Smart Factory Insights: Is Sustainability in Manufacturing a Benefit or Burden?
Smart Factory Insights: Manufacturing Meets the Flintstones