-
- News
- Books
Featured Books
- design007 Magazine
Latest Issues
Current IssueAll About That Route
Most designers favor manual routing, but today's interactive autorouters may be changing designers' minds by allowing users more direct control. In this issue, our expert contributors discuss a variety of manual and autorouting strategies.
Creating the Ideal Data Package
Why is it so difficult to create the ideal data package? Many of these simple errors can be alleviated by paying attention to detail—and knowing what issues to look out for. So, this month, our experts weigh in on the best practices for creating the ideal design data package for your design.
Designing Through the Noise
Our experts discuss the constantly evolving world of RF design, including the many tradeoffs, material considerations, and design tips and techniques that designers and design engineers need to know to succeed in this high-frequency realm.
- Articles
- Columns
- Links
- Media kit
||| MENU - design007 Magazine
Mark Thompson's Biggest Problems With PCB Designs
July 6, 2023 | Mark Thompson, Out of the Box ManufacturingEstimated reading time: 1 minute
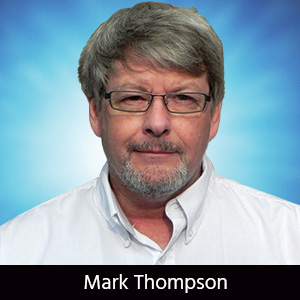
What are the top problems I see with PCB design? From where I sit now on the assembly side, one of my biggest concerns related to PCB design is the lack of uniform part markings on the Gerber or ODB++ data, specifically the way customers reference diodes. We would prefer either an “A” depicting the anode side or a “C” or “K” for the cathode side. Many customers simply use either a line or a dot, which requires us to contact them to clarify which side is the cathode and which side is the anode.
If a line is used to denote the cathode side, many times the silkscreen clip using the mask clearance by the fabricator wipes out most of the line, making it difficult or impossible to determine the location of the cathode side. Using a dot doesn’t really help; does a dot depict an anode or cathode? Besides, dots are typically used to denote Pin 1 designators. Please use an “A” for the anode side and a “C” or “K” for the cathode side.
Controlling Controlled Impedances
Another area that concerns me is controlled impedances. Don’t make assumptions about controlled impedances. Your goal as a PCB designer is to simulate impedance to within 10% of your goal. The fabricator should be able to take it the rest of the way since the fabricator knows its press parameters, press values, and effective Dk. Trust your chosen fabricator and use the numbers they provide you.
If you simply go online and check material PDFs for the purpose of establishing impedances yourself be aware that many of the generic spec sheets are for very thick dielectrics (.014" core and sometimes even .028" core) the Dk associated with the thicker dielectrics are higher which, if used for trace widths .005" and below will create a mismatch and the fabricator will come back with a line size that your space may not support.
Also, consider the speed. If the literature is showing 4.5 Dk at 1 Mhz, and you know this product will be running at higher speeds, such as 5,10 or even 20 Ghz, understand the Dk will be driven way down. You may be looking at something closer to 3.8 Dk at 5 Ghz and the mismatch will affect the impedance.
Mark Thompson is an engineering manager with Out of the Box Manufacturing and a longtime CAM expert.
This article appeared in the June 2023 issue of Design007 Magazine.
Suggested Items
Happy’s Tech Talk #38: Novel Metallization for UHDI
05/07/2025 | Happy Holden -- Column: Happy’s Tech TalkI have been involved in high-density electronics substrates since 1970 when I joined Hewlett-Packard’s RF semiconductor group after college. Figure 1 shows the difference between trace/space lithography for substrates and silicon starting in 1970. My projects involved sapphire circuits for RF devices, but the figure displays the state of PCBs and integrated CMOS circuits and their packaging, not discreet RF devices. Even then, semiconductors were 50X higher density.
New Database of Materials Accelerates Electronics Innovation
05/05/2025 | ACN NewswireIn a collaboration between Murata Manufacturing Co., Ltd., and the National Institute for Materials Science (NIMS), researchers have built a comprehensive new database of dielectric material properties curated from thousands of scientific papers.
New Database of Materials Accelerates Electronics Innovation
05/02/2025 | ACN NewswireIn a collaboration between Murata Manufacturing Co., Ltd., and the National Institute for Materials Science (NIMS), researchers have built a comprehensive new database of dielectric material properties curated from thousands of scientific papers.
Micron Announces Business Unit Reorganization to Capitalize on AI Growth Across All Market Segments
04/23/2025 | MicronMicron Technology, Inc., a leader in innovative memory and storage solutions, announced a market segment-based reorganization of its business units to capitalize on the transformative growth driven by AI, from data centers to edge devices.
Connected Commercial Drone Market to Reach $37.3 Billion Worldwide by 2029
04/04/2025 | Berg InsightBerg Insight, a leading IoT market research provider, today released a new report covering connected commercial drones used for industrial and governmental purposes.