-
-
News
News Highlights
- Books
Featured Books
- design007 Magazine
Latest Issues
Current IssueAll About That Route
Most designers favor manual routing, but today's interactive autorouters may be changing designers' minds by allowing users more direct control. In this issue, our expert contributors discuss a variety of manual and autorouting strategies.
Creating the Ideal Data Package
Why is it so difficult to create the ideal data package? Many of these simple errors can be alleviated by paying attention to detail—and knowing what issues to look out for. So, this month, our experts weigh in on the best practices for creating the ideal design data package for your design.
Designing Through the Noise
Our experts discuss the constantly evolving world of RF design, including the many tradeoffs, material considerations, and design tips and techniques that designers and design engineers need to know to succeed in this high-frequency realm.
- Articles
- Columns
- Links
- Media kit
||| MENU - design007 Magazine
Estimated reading time: 6 minutes
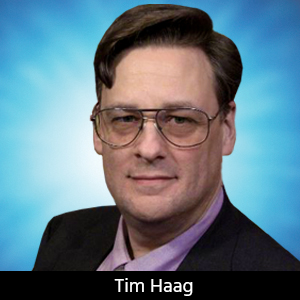
Tim’s Takeaways: How I Learned Advanced Design Strategies
If there’s one thing that helped my career in printed circuit board design more than anything else, it would be my time working at a service bureau. Don’t get me wrong, I’m delighted with the different captive shops I’ve worked for in larger companies throughout my career. Over the years, these organizations have provided the opportunity to lay out boards for computer systems, test equipment, display hardware, and much more. But in all those captive shops, the board types have usually been pretty much the same, which stands to reason when you consider the type and range of products sold by each parent corporation. The service bureau, however, was a different story.
Back in the Day
It is important to note: Working at the service bureau was a long time ago. CAD systems were in their adolescent phase, and designers were transitioning from light tables, X-Acto knives, dollies, and tape. At the same time, new types of electronics were growing at an accelerated rate, which went hand-in-hand with all the new CAD tools and designers—like me. On any given day, you would find yourself working on a standard board type for a garden-variety computer, and then switch over to a one-off power control board for an industrial application. While at the service bureau, I worked on boards ranging from an inch square to over three feet. I saw everything from single-sided boards to 16 layers, which wasn’t nearly as commonplace then as it is now.
Learning as you go was the name of the game, and there was a lot to learn. The technology wasn’t nearly as demanding as it is now, but for the CAD and manufacturing technologies available at the time, it was fairly tight. There were other boards, like the power control board I mentioned earlier, that had “traces” several inches wide to absorb huge amounts of energy, if necessary. We ended up using dumb graphics to design portions of that one because the CAD systems we were using couldn’t handle the width requirements.
I rarely worked with the same board shape twice except for the standard computer cards we would do from time to time; some of the outlines given to me were really bizarre. I remember one that had the shape of a skull, and we actually had a lot of fun with it until it was time to settle down and get to work. The parts placement and routing could be just as wild, and I worked on some boards with radial placement and routing. Due to the limitations of the CAD system, I would have to use a 1-mil grid for parts placement with a series of drawn circles on a graphics layer behind the parts serving as a placement guide.
Beyond PCB Design
Interestingly enough, circuit board types and technologies weren’t the only unusual variations in work that the service bureau introduced me to. I got to know different sorts of people too. Some folks would drop off their data and trust us to design the board just as you would expect. However, others would stay with us and monitor the layout throughout the entire process. There’s nothing more “helpful” than having a backseat driver while you are laying out a circuit board (and some of you will know exactly what I mean). One guy sitting behind me would try to “steer” while I routed his board, making a clicking noise whenever I changed directions or dropped a via. I can still hear him in my nightmares: “That should go left… click, ah that’s good… no I wouldn’t do that… click, straight down now… good… click!” To be fair, though, others made it all worthwhile. One of my backseat drivers bought me dinner while “we” were working. The next night he mentioned dinner again, and my boss joined us in hopes of a free meal, only to have the guy give my boss the bill instead. To this day, I can still see the sour expression on my boss’s face. Dinner and entertainment; life just didn’t get much better at the service bureau.
My time at the service bureau also exposed me to some other unique situations. For example, that little one-inch board I mentioned earlier took more than two weeks to design, even though it only had two connectors and maybe 75 connections. They took their time getting us the information we needed, then needed several days to examine my work. After some design changes, we had to drive out to their facility for a large-scale design review. Really? For a one-inch board? Meanwhile, back at the shop, I had laid out a standard computer card while waiting for them. That engineer had all his data neatly organized and packaged, and the design went like clockwork
Then there was the time a group of guys from a large aerospace corporation commandeered our conference room for a month while we designed a series of PCBs for their project. I don’t think that any of us spoke more than a dozen words to them; it was all very mysterious. White shirts, red power ties, and copious amounts of coffee, only then to emerge from their isolation to ask a question, request a correction, or grab another pot of coffee. It was pretty creepy in a “Scooby-Doo vs. the CIA” way.
New Technologies to Explore
One of the most fascinating things about working at the service bureau was learning about the new technologies in the projects we were designing for our customers. I’ve already mentioned some of them, like the power board that could take a lightning strike. Of course, there were plenty of computer cards and other standard electronics applications, but there were also some really interesting ones too. I worked on some projects where I wasn’t allowed to know their purpose. One engineer even hinted at a military application, which seemed unlikely since none of us had any security clearances at the time. But hey, it was the ’90s, so I guess anything is possible. I also worked on one of the first touchscreen systems designed for a CRT (I never knew if it ever worked) and a biosensor wristwatch before anyone had even considered the catchphrases “human interfaces” and “wearable technology.”
While this month’s contributors will have plenty to say on how to approach unique design situations, my intent was to highlight how starting out with all of these unusual design scenarios helped me be better prepared for the bulk of the work I encountered later on. Certainly, I learned how to coax the most out of a CAD system while being educated by some of the most talented designers I’ve ever known. Learning about many different board shapes, sizes, and technologies was invaluable later on, as was the exposure to multiple manufacturing processes, dimensioning etiquette, and design standards. I know things have changed over the years, and maybe my experience isn’t as easy to replicate anymore. It’s been a while since I’ve poked my nose into a service bureau, and it would be interesting to see what’s different and what hasn’t changed.
At any rate, if you ever get a chance to be part of a fast-moving, take-your-breath-away business like a service bureau, I recommend embracing the opportunity. You will be amazed at the education that you will come away with. Until next time, my friends, keep on designing.
This column originally appeared in the July 2023 issue of Design007 Magazine.
More Columns from Tim's Takeaways
Tim’s Takeaways: One for the ArchivesTim’s Takeaways: The Art of Technical Instruction
Tim’s Takeaways: PCB Design and Manufacturing—Let’s Work Together
Tim’s Takeaways: Take It From Scotty, Simple Really is Better
Tim’s Takeaways: Human Ingenuity and the Rigid-flex PCB
Tim’s Takeaways: Batter Up—Stepping Up to the Substrate
Tim’s Takeaways: Tribal Knowledge—Not the Villain You Thought
Tim’s Takeaways: Threading the Needle Through Advanced Packaging