-
- News
- Books
Featured Books
- design007 Magazine
Latest Issues
Current IssueShowing Some Constraint
A strong design constraint strategy carefully balances a wide range of electrical and manufacturing trade-offs. This month, we explore the key requirements, common challenges, and best practices behind building an effective constraint strategy.
All About That Route
Most designers favor manual routing, but today's interactive autorouters may be changing designers' minds by allowing users more direct control. In this issue, our expert contributors discuss a variety of manual and autorouting strategies.
Creating the Ideal Data Package
Why is it so difficult to create the ideal data package? Many of these simple errors can be alleviated by paying attention to detail—and knowing what issues to look out for. So, this month, our experts weigh in on the best practices for creating the ideal design data package for your design.
- Articles
- Columns
- Links
- Media kit
||| MENU - design007 Magazine
Book Excerpt: 'The Printed Circuit Designer's Guide to... Manufacturing Driven Design', Chapter 3
August 29, 2023 | I-Connect007 Editorial TeamEstimated reading time: 2 minutes
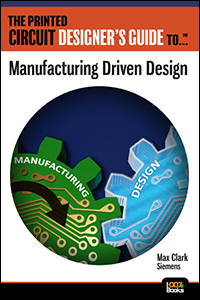
Excerpt from: The Printed Circuit Designer's Guide to... Manufacturing Driven Design, Chapter 3: Why a Change is Needed
What Is Manufacturing Driven Design?
Manufacturing Driven Design is the process of providing full manufacturing awareness within the design process in a manner that allows designers to optimize a design for manufacturing with the first release.
MDD begins at the incarnation of the design idea. In the context of manufacturing, the initial step involves defining the material requirements for the stackup based on the desired electrical requirements. Once the material stackup has been established, the design layout can then be carried out. This simultaneously considers a manufacturer’s process capabilities as well as the traditional design rule check (DRC). A traditional DRC is mainly focused on copper or electrical spacing requirements and does not consider manufacturing needs.
Currently what we call DFM is not necessarily Design for Manufacturing; it’s Manufacturing in spite of Design.
This improved approach of MDD is already implemented in silicon wafer production, where the foundry’s production capabilities are taken into consideration right from the placement of the first pattern during design. This approach resulted from the skyrocketing cost of missing an assignment to a wafer production schedule and having to wait for the next opportunity. Imagine a PCB DFM release process that behaved in the same manner. Consider the financial and environmental savings if PCB manufacturers and design organizations took the same approach. The opportunity for overall PCB manufacturing and environmental improvement would be staggering. The environmental impact of excessive PCB production cannot be measured in the recovery of unneeded bare PCBs alone, but also in the extra board edge trim, wastewater—which contains copper, any number of stripping materials, tin, lead, and much, much more. Analyzing the environmental impact of PCB manufacturing is outside of this book's scope but should not be overlooked.
How Is MDD Different From DFM?
Design for Manufacturing today is seen as a step performed after the design is completed but before it is tooled for manufacturing. Often it is done with limited visibility of the applicable manufacturing partners’ process capabilities for that design technology.
Manufacturing Driven Design facilitates a more advanced level of collaboration, automation, and intelligence to achieve complete manufacturing awareness, surpassing the capabilities of DFM. In its ideal form, MDD covers all manufacturing details that can impact the yield, cost, or reliability of the PCB. It should include the following at a minimum:
- Fabrication process constraints
- Assembly process constraints
- Test process constraints
- Actual PCB material stackup to be used
- Assembly array and fabrication panel configurations
Very few manufacturers today provide their manufacturing process capabilities in a systematic, comprehensive manner to their design customers. Information is conveyed as requested, and only on the specific topic(s) at hand. Even then, it is communicated via email or a PDF of their manufacturing process capabilities specification—nothing that can be automatically acted upon within the design process. MDD provides the infrastructure to share all the necessary manufacturing process capabilities in an automated, synchronized method.
Carrying Capabilities Forward
Understanding the importance of MDD within electronics begins with the end. Ideally, manufacturing processes (fabrication, assembly, test) would be completed with the highest yield and reliability for the lowest cost possible. As the phrase “Manufacturing Driven Design” implies, the manufacturing process capabilities would be introduced at the beginning of the design process, which is carried forward throughout the process. Stated another way, a PCB design is constrained by not only the electrical requirements, but also by the manufacturing process capabilities.
Suggested Items
I-Connect007 Editor’s Choice: Five Must-Reads for the Week
07/18/2025 | Nolan Johnson, I-Connect007It may be the middle of the summer, but the news doesn’t quit, and there’s plenty to talk about this week, whether you’re talking technical or on a global scale. When I have to choose six items instead of my regular five, you know it’s good. I start by highlighting my interview with Martyn Gaudion on his latest book, share some concerning tariff news, follow that up with some promising (and not-so-promising) investments, and feature a paper from last January’s inaugural Pan-European Design Conference.
Elephantech Launches World’s Smallest-Class Copper Nanofiller
07/17/2025 | ElephantechJapanese deep-tech startup Elephantech has launched its cutting-edge 15 nm class copper nanofiller – the smallest class available globally. This breakthrough makes Elephantech one of the first companies in the world to provide such advanced material for commercial use.
Copper Price Surge Raises Alarms for Electronics
07/15/2025 | Global Electronics Association Advocacy and Government Relations TeamThe copper market is experiencing major turbulence in the wake of U.S. President Donald Trump’s announcement of a 50% tariff on imported copper effective Aug. 1. Recent news reports, including from the New York Times, sent U.S. copper futures soaring to record highs, climbing nearly 13% in a single day as manufacturers braced for supply shocks and surging costs.
I-Connect007 Editor’s Choice: Five Must-Reads for the Week
07/11/2025 | Andy Shaughnessy, Design007 MagazineThis week, we have quite a variety of news items and articles for you. News continues to stream out of Washington, D.C., with tariffs rearing their controversial head again. Because these tariffs are targeted at overseas copper manufacturers, this news has a direct effect on our industry.I-Connect007 Editor’s Choice: Five Must-Reads for the Week
Digital Twin Concept in Copper Electroplating Process Performance
07/11/2025 | Aga Franczak, Robrecht Belis, Elsyca N.V.PCB manufacturing involves transforming a design into a physical board while meeting specific requirements. Understanding these design specifications is crucial, as they directly impact the PCB's fabrication process, performance, and yield rate. One key design specification is copper thieving—the addition of “dummy” pads across the surface that are plated along with the features designed on the outer layers. The purpose of the process is to provide a uniform distribution of copper across the outer layers to make the plating current density and plating in the holes more uniform.