-
- News
- Books
Featured Books
- design007 Magazine
Latest Issues
Current IssueShowing Some Constraint
A strong design constraint strategy carefully balances a wide range of electrical and manufacturing trade-offs. This month, we explore the key requirements, common challenges, and best practices behind building an effective constraint strategy.
All About That Route
Most designers favor manual routing, but today's interactive autorouters may be changing designers' minds by allowing users more direct control. In this issue, our expert contributors discuss a variety of manual and autorouting strategies.
Creating the Ideal Data Package
Why is it so difficult to create the ideal data package? Many of these simple errors can be alleviated by paying attention to detail—and knowing what issues to look out for. So, this month, our experts weigh in on the best practices for creating the ideal design data package for your design.
- Articles
- Columns
- Links
- Media kit
||| MENU - design007 Magazine
An Overview of Rigid-flex Design
September 13, 2023 | I-Connect007 Editorial TeamEstimated reading time: 1 minute
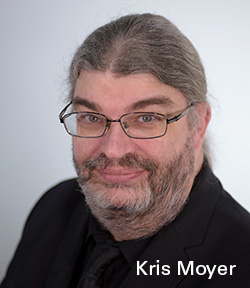
For this month’s issue on rigid-flex design, we spoke with instructor Kris Moyer, who teaches the IPC class “PCB Design for Flex and Rigid-Flex Boards.” In this wide-ranging interview, Kris breaks down the hurdles facing rigid-flex designers and offers a variety of solutions for rigid board designers taking on their first rigid-flex circuits. He also provides a few horror stories to illustrate what happens if you don’t follow sound design practices, rules, and standards. And, as Kris points out, “Your fabricator is your friend.”
Andy Shaughnessy: What are you trying to get across to the students when you’re teaching rigid-flex design? What are the biggest challenges?
Kris Moyer: One of the biggest concepts I want to get across to students is that there are a lot of untapped, unforeseen, intangible benefits to rigid-flex, both from a design point of view and a total cost of ownership point of view. Rigid boards are usually connected with wire harnesses or cables, and we know that wire harnesses and cables are the largest point of failure in the system. Wires and cables tend to break, especially at the solder joints or pins. If we can remove all those harnesses and integrate all of that into the structure of the board, we can vastly reduce the failure rate of our designs.
If you choose to go rigid-flex, there is an initial cost expenditure: added processes, time, complexity, and all of that. But let's say I have a design with three circuit boards that would need two cable harnesses, one from board one to board two, and one from board two to board three. That's a grand total of five different item numbers I would need for each board. I would have three drawing numbers: a number for the schematic, a number for the board, and a number for the assembly. For three boards, that's nine drawings I must maintain, and then another two drawings per cable, and let's assume two cables. That's a total of 13 separate drawings and part numbers I have to maintain in my system.
To read this entire conversation, which appeared in the September 2023 issue of Design007 Magazine, click here.
Suggested Items
SHENMAO Strengthens Semiconductor Capabilities with Acquisition of PMTC
07/10/2025 | SHENMAOSHENMAO America, Inc. has announced the acquisition of Profound Material Technology Co., Ltd. (PMTC), a premier Taiwan-based manufacturer of high-performance solder balls for semiconductor packaging.
KYZEN to Highlight Understencil and PCB Cleaners at SMTA Querétaro Expo and Tech Forum
07/09/2025 | KYZEN'KYZEN, the global leader in innovative environmentally responsible cleaning chemistries, will exhibit at the SMTA Querétaro Expo & Tech Forum, scheduled to take place Thursday, July 24, at Centro de Congresos y Teatro Metropolitano de Querétaro.
Driving Innovation: Direct Imaging vs. Conventional Exposure
07/01/2025 | Simon Khesin -- Column: Driving InnovationMy first camera used Kodak film. I even experimented with developing photos in the bathroom, though I usually dropped the film off at a Kodak center and received the prints two weeks later, only to discover that some images were out of focus or poorly framed. Today, every smartphone contains a high-quality camera capable of producing stunning images instantly.
Hands-On Demos Now Available for Apollo Seiko’s EF and AF Selective Soldering Lines
06/30/2025 | Apollo SeikoApollo Seiko, a leading innovator in soldering technology, is excited to spotlight its expanded lineup of EF and AF Series Selective Soldering Systems, now available for live demonstrations in its newly dedicated demo room.
Indium Corporation Expert to Present on Automotive and Industrial Solder Bonding Solutions at Global Electronics Association Workshop
06/26/2025 | IndiumIndium Corporation Principal Engineer, Advanced Materials, Andy Mackie, Ph.D., MSc, will deliver a technical presentation on innovative solder bonding solutions for automotive and industrial applications at the Global Electronics A