Estimated reading time: 7 minutes
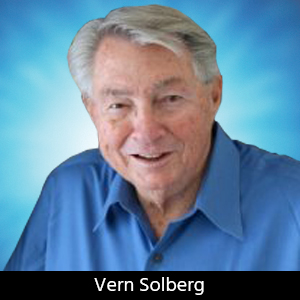
Designer’s Notebook: DFM Principles for Flexible Circuits
Flexible circuit applications can be as basic as furnishing electrical interconnect between two conventional circuit board assemblies, or to provide a platform for placing and interconnecting electronic components. During the planning and pre-design phase of the flexible circuit, there will be several material and process related questions that need to be addressed.
Most flexible circuit fabricators welcome the opportunity to discuss their customers’ flexible circuit objectives prior to beginning the actual design process. The flexible circuit manufacturer will often furnish guidance that can avoid potential delays in beginning the fabrication process and ensuring satisfaction in the end product. The flexible and rigid-flex circuit development will follow a sequence of events that include timely review cycles, both internally and with the fabrication company selected:
- Determine physical constraints
- Prepare a 2D flat outline
- Develop a model (mechanical mock-up)
- Component layout and circuit routing
The design guidelines for flexible circuits, although similar to rigid circuits, have distinctive differences that are influenced by specific applications, material selection, and the intended operating use environments. The fundamental issues to be defined before beginning the flexible circuit design include several primary elements:
- Quantity of signal traces required across the flexible area
- Conductor widths required for current-carrying capacity
- Spacing required for voltage isolation
- EMI shielding and impedance control requirement
- Determine the surface area required for routing the circuit
Flexible circuit complexity can have a significant impact on manufacturing lead-time and unit cost. Designers commonly create rigid boards with a more uniform rectangle outline, but flexible circuits or the flexible portions of the rigid-flex circuit outline are more likely to be profiled to meet specific application. But before finalizing the outline for the circuit, the designer is advised to prepare a physical model to confirm the dimensions initially established meets expectation. The example shown in Figure 1 represents a flexible circuit outline with holes, slots and openings, and circuit extensions for connectivity with other assemblies.
If the circuit will include surface mount components and/or interface connectors, these areas must be defined on the model as well. To ensure the finished part will hold up to the various stages of assembly and use, the designer must include attributes that will minimize physical damage: inside corners, narrow slots and slits, or in areas accommodating connectors or areas reserved for component mounting.
Corner and Slot Feature Development
Avoid sharp corners in all recesses of the flexible circuit. The designer must specify a radius at these locations in order to lessen the potential for cracking or tearing of the flexible material. Providing a radius on the inside corner (Figure 2a) will resist the propagation of tearing. When the inside corner must provide an unobstructed corner profile, the designer can position the radius beyond the corner (Figure 2b).
Manufacturers recommend providing a large radius on all inside corners. This can contribute to increasing part reliability, one that will be more resistant to tearing when twisted.
Regarding “slit” and “slot” features, flexible circuit fabricators recommend that these features be furnished with a hole or full radii where they terminate. For the “slit” features, a 1.5 mm (~0.06") diameter hole at the end of the “slit” typical of the example furnished in Figure 3a, will provide a barrier to minimize tearing when the flexible circuit is physically stressed. When a wider slot feature resembling that shown in Figure 3b is included in the flexible circuit, fabricators recommend a full radius at its end.
To further minimize tear and cracking of the material at the inside corner areas, a narrow pattern of copper foil can be retained that follows the profile of the radii. If the corner or slot is subjected to excessive strain during use, include an additional thickness of the base dielectric in the area to further reinforce the site.
Holes and cutouts in the flexible circuit should maintain a minimum distance of 1.3 mm between the exterior edge of the flex circuit outline and edges of interior located holes and cutouts. In addition, cutouts should always maintain a minimum radius of 0.75 mm in each corner, typical of that illustrated in Figure 4.
Circuit Conductor Density
Determining conductor density and the routing area requirement on the flexible portion of the circuit will depend on the number and width established for signal conductors. For both single and two metal flex, the overall width of the base material must also provide adequate surface area for cover-layer film bonding. The general rule for a conductor to the dielectric material’s outer edge is a minimum of 0.70 mm (~0.030") but, where possible, the copper-to-edge distance should be maximized. Additionally, the minimum distance between the exterior edge of the flex circuit and the edges of interior located holes and cutouts should not be less than 1.30 mm (~0.050"). But, typical of the conductor-to-edge spacing noted above, this provides a greater distance where possible. The examples in Figure 5 furnish general guidance for providing clearance between key features of the flexible circuit.
When the conductor path on the flexible circuit must change direction, the designer must avoid sharp, 90-degree turns. Ideally, these conductor paths should be routed with a nested chamfer or generous radii. Multiple conductor paths routed in parallel should also maintain uniform spacing with progressively larger radii from the center axis.
Bend Area Consideration
The flexible circuit should not be bent or formed in areas where there is a discontinuity in the cover-layer, termination of plating, or any other stress-concentrating feature. The acceptability of this condition is determined by the thickness of materials, the radius of the bend, and the severity of the operating environment. Flexible circuits designed for dynamic applications may be more susceptible to conductor failure than the bend-to-install or mechanically formed application.
Circuit fabricators recommend that designers avoid unnecessary circuit thickness in the bend zone because it can hinder flexible capabilities. If a portion of the flex circuit needs to be thicker for supporting components or connectors, add a stiffener. Suppliers further note that calculating bend-cycles over the projected life of the product is crucial to your design. When the circuit is flexed beyond the limit ratios established, the copper foil may elongate, become brittle, and generate micro-cracks in the bend zone. Guidelines for minimum bending radius for 90-degree “bend-to-install” for fully bonded circuits:
- Single sided, 10:1
- Double sided, 10:1
- Multilayer, 20:1
A rule of thumb for estimating minimum bend radii is 10x material thickness for single-metal layer circuits and 12x for double-metal layer circuits.
For maximum dynamic flex life and reliability, conductors in the bend area should be routed perpendicular to and evenly spaced across the bend area. Furthermore, the designer should not specify additional plating thickness in areas requiring bending or flexibility. Likewise, conductors should maintain a uniform width in the bend area and, when possible, the neutral bend axis should be at the center of the conductor pattern.
For dynamic flex applications that require repeated bending up to 90-degree from flat, the recommended minimum bending radius (R) is:
- For single-sided flex, 100:1
- For double-sided flex, 150:1
- Multilayer dynamic flexing is not recommended
A rule of thumb for estimating minimum bend radii is 10x material thickness for single-metal layer circuits and 12x for two-metal layer circuits.
In summary, for maximum dynamic flex life and reliability, conductors in the bend area should adhere to the following considerations:
- Conductors should be routed perpendicular to the bend area
- Conductors should be uniformly spaced across the bend area
- Do not apply or plate additional metals in the bend area
- Conductors should maintain a uniform width in the bend area
- Do not place SMT components or plated-through via holes in the bend area
Supplier Capability Assessment
In preparation for developing the flexible circuit, the designer must gain a general understanding of the flexible circuit fabrication process variations and review design guidelines furnished by the potential supplier(s). You will find that the capabilities and process methods can vary significantly from one supplier to another. Flexible circuit suppliers, for example, may publish their capability in two classifications: standard and advanced. While their standard level of product will typically use an image, print, and etch process, fabricators with more advanced imaging and pattern-plating capability are able to reduce conductor geometries. For controlling product cost and maximizing process yield, however, the designer may consider the more conservative approach for conductor routing.
Appearance
Vern Solberg will conduct a half-day tutorial course on “Flexible Circuit Design for Manufacturing Principles,” Oct. 10, at the SMTA International Conference 2023 in Minneapolis, Minnesota. This course addresses the design, fabrication, and assembly criteria for developing and implementing both flexible and rigid-flex circuits. To register and participate in this timely tutorial event, visit smta.org.
This column originally appeared in the September 2023 issue of Design007 Magazine.
More Columns from Designer's Notebook
Designers Notebook: Layer Stackup Planning for RF Circuit BoardsDesigners Notebook: Addressing Future Challenges for Designers
Designers Notebook: Impact of Advanced Semiconductor Packaging on PCB Stackup
Designers Notebook: Implementing HDI and UHDI Circuit Board Technology
Designer's Notebook: Heterogeneous Integration and High-density SiP Technologies
Designers Notebook: PCB Design and IPC-CFX for Assembly Automation
Designer’s Notebook: What Designers Need to Know About Manufacturing, Part 2
Designers Notebook: What Designers Need to Know About Manufacturing, Part 1