The Drive Toward UHDI and Substrates
September 20, 2023 | I-Connect007 Editorial TeamEstimated reading time: 3 minutes
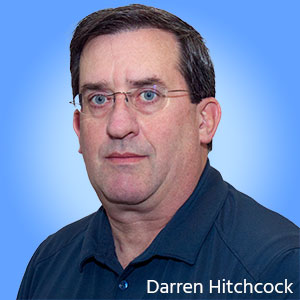
Panasonic’s Darren Hitchcock spoke with the I-Connect007 Editorial Team on the complexities of moving toward ultra HDI manufacturing. As we learn in this conversation, the number of shifting constraints relative to traditional PCB fabrication is quite large and can sometimes conflict with each other.
Barry Matties: Darren, I recently had watched your presentation about the demands on material—resin, weave, surface, etc.—to meet the demands of higher density, finer features. What was your message to your audience regarding the state of the industry for materials in HDI and UHDI?
Darren Hitchcock: In that presentation1, I covered some of the changes like glass style and the composition of the glass. For the longest time, we've had E-glass, which is, of course, the cost-effective option. But as electrical performance requirements have increased, we've seen more demand for low-Dk and ultra-low Dk glass. The increased trends toward that glass mean better availability and cost; as the electrical performance benefits are also decision factors.
I also drilled down on copper. The demand for smoother copper is increasing, which affects the industry standards. I'm involved in the IPC committee for copper and the committee for glass reinforcements. I chair IPC-4101, the IPC committee for PCB laminates. I'm engaged in the industry consortia with OEMs, fabricators, and raw material suppliers.
Nolan Johnson: What's really happening in the industry around those groups?
Hitchcock: In my SMTA presentation, I talked about the North American market, how the book-to-bill has been doing lately, and then I shifted quickly into talking about density.
At a high level, packaging density drives both PCB density and substrate density. As your packages get more stuff packed in—10 pounds of stuff in a five-pound bag, for example—everything gets smaller and more compact, and there's more I/O. That drives the packaging technology, which in turn, drives the PCB technology.
Johnson: Which then drives the materials?
Hitchcock: Yes. From a materials perspective, they're getting thinner. The electrical drivers are making for a lower dielectric constant, but that's not the primary driver. The primary driver is the desire to get lower dissipation factor, or loss tangent. The next driver is to get the copper smoother.
The copper challenge is adhesion; as your resin systems become lower and lower loss, it's difficult to get them to stick to anything. At the same time, copper is getting smoother, which makes it harder to adhere to resin systems. Those are some of the emerging challenges for both copper and the resin system. As you continue to add filler, you have increasingly lower percentages of the resin in that system, which challenges adhesion. Glass transition temperatures in newer materials are getting higher, which makes them more brittle. The fillers make them brittle, too.
At the same time, the packaging is adding I/O, and the sizes of the packages are getting larger, especially in infrastructure, but also in the mobile space. The XY dimensions are growing to accommodate the I/O, plus the pad sizes are getting smaller. This means the surface area with the volume of your solder—the surface area to your BGA pads, both on the package side and on the PCB side—are getting smaller. Meanwhile the adhesion is getting more challenging and the materials more rigid. Suddenly, CTE mismatch becomes a much bigger challenge.
Johnson: And you might be talking about ball grid arrays for most of the packages that have thousands of potential solder failures per package.
Hitchcock: Yes, the array packages and their increasing density is a challenge on materials. There are some creative things to be done on the material side to either absorb the strain between the package and the PCB, or to make them more robust to the stresses that they encounter.
Happy Holden: Electric vehicles are challenging. They're using the latest chip technology, but they want subassemblies which are low-cost but high reliability for a longer life. There are the mobile phone requirements for small form factors and power efficiency; that's a real dilemma.
Hitchcock: That's where substrate—like or near—substrate technology comes into play. It’s the space between a substrate or packaging; they’re circuit boards but located on the packaging side vs. the traditional PCB side. The line is blurring, and within that blurring is the desire for the density of a substrate but at the cost of a PCB.
Continue reading the rest of this conversation in the September 2023 issue of PCB007 Magazine.
Reference
- ‘Advanced Technologies for Printed Circuit Board Fabrication and Raw Materials’, SMTA Oregon Expo 2023 keynote presentation.
Testimonial
"The I-Connect007 team is outstanding—kind, responsive, and a true marketing partner. Their design team created fresh, eye-catching ads, and their editorial support polished our content to let our brand shine. Thank you all! "
Sweeney Ng - CEE PCBSuggested Items
Rules of Thumb: Design007 Magazine, November 2024
11/11/2024 | I-Connect007 Editorial TeamRules of thumb are everywhere, but there may be hundreds of rules of thumb for PCB design. They’re built on design formulas, fabricators’ limitations, and tribal knowledge. And unfortunately, some longtime rules of thumb should be avoided at all costs. How do we separate the wheat from the chaff, so to speak?
Connect the Dots: Best Practices for Prototyping
09/21/2023 | Matt Stevenson -- Column: Connect the DotsPCB prototyping is a critical juncture during an electronic device’s journey from concept to reality. Regardless of a project’s complexity, the process of transforming a design into a working board is often enlightening in terms of how a design can be improved before a PCB is ready for full production.
Asia/Pacific AI Spending Surge to Reach a Projected $78 Billion by 2027
09/19/2023 | IDCAsia/Pacific spending on Artificial Intelligence (AI) ), including software, services, and hardware for AI-centric systems will grow to $78.4 billion in 2027, according to International Data Corporation's latest Worldwide Artificial Intelligence Spending Guide.
Intel to Sell Minority Stake in IMS Nanofabrication Business to TSMC
09/13/2023 | IntelIntel Corporation announced that it has agreed to sell an approximately 10% stake in the IMS Nanofabrication business to TSMC. TSMC’s investment values IMS at approximately $4.3 billion, consistent with the valuation of the recent stake sale to Bain Capital Special Situations.
RAF Invests in BAE Systems’ Most Advanced Fighter Pilot Helmet
09/13/2023 | BAE SystemsThe UK Ministry of Defence (MOD) has awarded BAE Systems a contract to develop its Striker II Helmet Mounted Display (HMD) for the Royal Air Force (RAF) Typhoon fleet. The contract, valued at £40m, will create and sustain more than 200 highly-skilled jobs at BAE Systems’ sites in Kent and Lancashire working directly on the Striker II programme. In total, the Typhoon programme sustains more than 20,800 jobs across the UK.