-
- News
- Books
Featured Books
- smt007 Magazine
Latest Issues
Current IssueSupply Chain Strategies
A successful brand is built on strong customer relationships—anchored by a well-orchestrated supply chain at its core. This month, we look at how managing your supply chain directly influences customer perception.
What's Your Sweet Spot?
Are you in a niche that’s growing or shrinking? Is it time to reassess and refocus? We spotlight companies thriving by redefining or reinforcing their niche. What are their insights?
Moving Forward With Confidence
In this issue, we focus on sales and quoting, workforce training, new IPC leadership in the U.S. and Canada, the effects of tariffs, CFX standards, and much more—all designed to provide perspective as you move through the cloud bank of today's shifting economic market.
- Articles
- Columns
- Links
- Media kit
||| MENU - smt007 Magazine
PCB West: Coating Services at HZO
October 4, 2023 | Nolan Johnson, I-Connect007Estimated reading time: 3 minutes
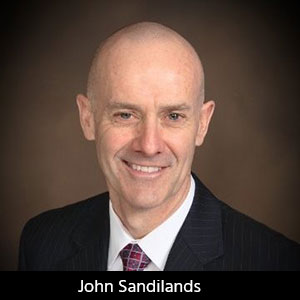
John Sandilands, director of sales at HZO, explains his company’s approach to the coating process, and how it stands out for companies wanting to protect their electronics products from harsh conditions. The secret is in the process itself, John says.
Nolan Johnson: John, tell me about HZO.
John Sandilands: HZO is the technology leader in solutions for protecting electronics from harsh environments. We’re involved from design inception all the way to mass production. We work with customers across all markets to help protect their electronics against environmental ingress challenges, especially when their products are outdoors, where rain, salt, fog, and other chemicals can cause corrosion. These could be consumer electronics or mission critical products in aerospace, automotive, and medical; we have multiple offerings in the thin film and nanocoating areas.
Johnson: These are the coatings themselves? Or is HZO developing the machinery as well?
Sandilands: Correct. We provide a turnkey solution to our customers by supplying the coating, specialized equipment and engineering services. We can work with customers to meet their manufacturing needs from providing coating as a service to embed coating systems inside their plants, or at a contract manufacturer’s facilities. We’re very flexible in that respect. We work with customers that have tens or hundreds of pieces a year, to customers who do tens of millions of pieces a year.
Johnson: Ten or 15 years ago, coating was regarded as very specialized, something of a boutique area; not so much anymore. Just look at who's driving the market: automotive, electric vehicles, medical, wearables, those sorts of applications. The products in these arenas need this.
Sandilands: Absolutely. Traditional methods of coating include liquid dip or spray-on, which goes on bulky (in the millimeters of thickness) to overcome some of the deficiencies for the application process. With our solutions being in the nanometer and micron ranges, you're eliminating weight along with bulk. That gives us a real advantage, especially when you look at the many markets where miniaturization is a priority.
Johnson: What is the impact on repairability? A coating that is millimeters thick is hard to get off if you need to do any rework. It sounds like your approach might be much more accessible.
Sandilands: Yes, our processes are done prior to final testing. One of the advantages of our process is that it can be reworked. Because they're so thin, they can be abraded off with a tool for spot-work. If you're looking to access a larger re-work area than you can accomplish with an abrasive material, then we could do a recoating as required. There are many advantages in that respect.
Johnson: What is the application technology to get something that thin?
Sandilands: To get down to nano and micrometer levels of thickness, we utilized chemical vapor deposition (CVD for short) to apply our coatings. Simply put, the coatings are applied in a coating chamber, under vacuum to maximize conformality and unformity. For example, our Guardian Series Parylene coatings start off as a powdered solid which is heated in a furnace, and it changes into a gas. That gas enters our chamber under vacuum. Those gas molecules then adhere to every surface of whatever we put in there. Masking, of course, is a critical aspect of what we do. We don't want to coat connectors or ports because it will make them electrically nonfunctional. This can be a positive however if customers are looking for dielectric benefits.
We also have a nano coating process that uses plasma as an application catalyst. Ultimately, the exact coating material depends on what final result the project calls for. For example, if the customer doesn't require submersion—maybe just splash protection—then they might not need a solution like Parylene. In that case, our plasma-based process may be a better fit as it has great splash resistance properties in high humidity or wet environments.
Johnson: It sounds like the trend for environmental protection continues going broader and deeper, in general.
Sandilands: One of the other aspects is to transition away from more traditional materials found in “forever chemicals”. We have solutions that do not have halogenated or fluorinated compounds in them. This is a win for both our customers and the environment.
Johnson: Thanks for taking the time to talk with us, John.
Sandilands: My pleasure.
Testimonial
"In a year when every marketing dollar mattered, I chose to keep I-Connect007 in our 2025 plan. Their commitment to high-quality, insightful content aligns with Koh Young’s values and helps readers navigate a changing industry. "
Brent Fischthal - Koh YoungSuggested Items
MacDermid Alpha Electronics Solutions Unveils Unified Global Website to Deepen Customer, Talent, and Stakeholder Engagement
07/31/2025 | MacDermid Alpha Electronics SolutionsMacDermid Alpha Electronics Solutions, the electronics business of Elements Solutions Inc, today launched macdermidalpha.com - a unified global website built to deepen digital engagement. The launch marks a significant milestone in the business’ ongoing commitment to delivering more meaningful, interactive, and impactful experiences for its customers, talent, and stakeholders worldwide.
SCS Launches New G4 Spin Coater and Upgrades 6800 Series with Improved Design Features
07/23/2025 | SCSSpecialty Coating Systems (SCS) is pleased to announce the launch of its next-generation G4 Spin Coater, delivering enhanced control, connectivity and usability for research, development and small-scale production environments.
The Knowledge Base: A Conference for Cleaning and Coating of Mission-critical Electronics
07/08/2025 | Mike Konrad -- Column: The Knowledge BaseIn electronics manufacturing, there’s a dangerous misconception that cleaning and coating are standalone options, that they operate in different lanes, and that one can compensate for the other. Let’s clear that up now. Cleaning and conformal coating are not separate decisions. They are two chapters in the same story—the story of reliability.
Scanfil Signs New Customer and Starts Manufacturing Control Units for Emerson
06/19/2025 | ScanfilScanfil and Emerson signed an agreement concerning the Rosemount Tank Radar for Advanced Level Measurement Solutions. Emerson is a global technology, software and engineering company domiciled in the USA.
Specialty Coating Systems (SCS) Relocates to New Custom-Built Site in Switzerland
06/19/2025 | Specialty Coating Systems (SCS)Specialty Coating Systems (SCS) is pleased to announce the relocation of its Switzerland operations to a new custom-built facility. The approximately 2,200 square-meter coating operation, which is located at Rue du Collège 43, 2300 La Chaux-de-Fonds, is ISO 9001:2015 certified and specifically designed to optimize quality and provide excellent service for customers across the medical device, electronics, aerospace and automotive markets.