-
- News
- Books
Featured Books
- design007 Magazine
Latest Issues
Current IssueProper Floor Planning
Floor planning decisions can make or break performance, manufacturability, and timelines. This month’s contributors weigh in with their best practices for proper floor planning and specific strategies to get it right.
Showing Some Constraint
A strong design constraint strategy carefully balances a wide range of electrical and manufacturing trade-offs. This month, we explore the key requirements, common challenges, and best practices behind building an effective constraint strategy.
All About That Route
Most designers favor manual routing, but today's interactive autorouters may be changing designers' minds by allowing users more direct control. In this issue, our expert contributors discuss a variety of manual and autorouting strategies.
- Articles
- Columns
- Links
- Media kit
||| MENU - design007 Magazine
Estimated reading time: 7 minutes
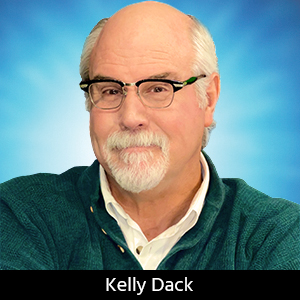
Contact Columnist Form
Target Condition: What the Heck? A PCB Tech Spec Check
In 1972, learned the adage “Measure twice, cut once” from my seventh-grade woodshop teacher, Mr. Fenoglio. To this day, I hear his voice every time I use a pencil to mark a piece of wood that I’m ready to cut. I mark it and then re-measure the edge to which it will join before sawing or drilling. Over time, I’ve saved a lot of money avoiding costly personal woodworking and building project errors.
I wish I could say that my PCB design record over the years was similarly as error free in regard to form, fit, and function. Why didn’t I hear Mr. Fenoglio’s voice when I was dimensioning that CAD drawing? How could I have overlooked that I was drafting in a different scale? What about when I imported a “metric” DXF outline into my “inches” PCB layout and thought there was still plenty of room to add more circuitry? How about that time I built that card-edge connector library part and reversed the A and B sides? I’ve lost count of how many times I didn’t catch the reversed pin numbering on some of those little three-pin SOT23 transistors.
The fact is that effective PCB design and manufacturing is not done sitting alone in a cave. Stakeholders in PCB project development must have ways of checking each other’s work before the chips are cut, so to speak. Printed circuit assemblies contain thousands of geometric points which must successfully interface with unseen “next assemblies” on a worldwide scale in order to fit together correctly while running down the manufacturing conveyors. Designing a PCB form to fit is only part of the project equation. After the design is manufactured and assembled, it must perform its function electrically. The characteristics of signal integrity are affected by the physical geometry. The form and fit of the selected materials must be calculated, measured, and adjusted for their various compositions before any material is printed, etched, pressed, bonded, drilled, plated, coated, or soldered.
Designers Must Look Outside Their Caves, But Where?
Now more than 40 years later, my woodshop teacher’s maxim seems to be drowned out by a new wave of PCB industry social media influencers who constantly remind me to “always check with my fabricator.” Some bluntly warn me, “Never trust component datasheets.” Still others will push their own recipe for the “perfect” footprint to prevent an 0201 chip capacitor from tombstoning. With all due respect, can these sources for design wisdom be trusted? Do their methodologies consider all the manufacturing process stakeholders? Does their content only show how to get their design portion of the job done with the caveat, “But check with your fabricator,” as an admission that the content you’ve been watching for the last 15 minutes may not be producible under many circumstances? Just search a few PCB design topics on social media. How can there be dozens of “perfect” tiny chip capacitor footprints when the geometries all vary, and the critical considerations of solder deposition and thermal profiling are not even mentioned? How can a PCB designer check in with a fabricator when it is unknown where the design will be produced in volume?
When it comes to a successful PCB design for production, the first step is for designers to admit that, in most cases, they do not know where the boards they design will be fabricated or assembled. The next step is realizing that for the world to stay in business, all the manufacturing process stakeholders have built their process success around the ability to meet IPC standards.
The final step is to become knowledgeable about IPC standards—not only those which apply to the PCBA design in process, but the ones which need to be appropriately specified in the manufacturing process notes.
PCB Tech Spec Check
Most every day I come across customer PCB design documentation showing severe gaps in PCB designer familiarity with outside materials and manufacturing processing. To make matters worse, the fabrication and assembly notes often reference specifications intended for design, not manufacturing. The numbers and class designations are often inappropriately assigned or non-existent. I often make the point that every other stakeholder in the PCB industry adheres to a process and checks their output to a spec. Why should the process of PCB design be any different?
PCB design must be considered a process by the PCB designer and must therefore be checked to some appropriate specifications, but which ones? Based on the wide variety of designs I review from our customers across North America, designers could use some help in this area.
I’ve recently come across a useful key to help solve this issue. IPC has published a PCB checklist guideline titled IPC Checklist for Producing Rigid Printed Board Assemblies. This document not only serves as an effective roadmap pointing designers to existing PCB design and manufacturing specifications, but who is responsible during the various stages of engineering, manufacturing, and test. After previewing this checklist, let me tell you a story about how I put it to use right away.
Our assembly line was having a challenge assembling a QFN part in which the PCB designer must have “dreamed up” a land pattern to attach the part to the PCB using a complicated window array, presumably to reduce the solder deposition. The footprint was “designed” but to what standard and with what manufacturing parameters in mind? The land pattern incorporated several “creative” technologies, including via-in-pad, solder-on-pad, and special “windows paning” features to attach the part. DFM rules appeared to be ignored for every technology addressed on this footprint. Our manufacturing engineering team exclaimed, “What the heck?” My response was to perform a PCB design “PCB tech spec check” using this newfound document. I first needed to find the category for the technology in order to check the guidelines.
I quickly found QFN in the “Demand on Assembly” column and proceeded to look up the specs relevant to issues found by our manufacturing engineers. First, I could see that this challenge had to do with a quad flat pack-style component including a large heat sink “slug” and otherwise referred to as a “bottom termination component” or quad flat no-lead (QFN). I went directly to the “Project Start Level” checklist to see how the responsible electronic designer could have easily referenced IPC-7093 to see more information on how to design this part footprint for better DFM.
I won’t address every DFM improvement here that I was able to suggest to our manufacturing engineering team. But they were appreciative for the list of detailed IPC based improvement I was able to publish to be forwarded to our customer.
I found this checklist knowledge very empowering. As a designer of QFN footprints, I must admit I didn’t know that IPC-7093 exists. But with this checklist as a guide, I am led to the IPC-based knowledge I need for help. I can read the spec and research what other well-known contributors have written on similar design challenges when dealing with these parts. I was amazed when I searched this standard and found a very helpful presentation on QFN prinicples by Vern Solberg, which will prove very effective in “selling” these IPC spec-based DFM ideas to our customer.
IPC Checklist for Producing Rigid Printed Board Assemblies
- Checklist at the Project Start Level
- Checklist at the CAD Level (map)
- Checklist at the Printed Board Ordering Level (map)
- Checklist at the Assembly Ordering Level (map)
- Checklist at the Cleaning and Conformal Coating Level (map)
- Checklist at the Quality Check Level (map)
Conclusion
The void of knowledge about how to collaboratively design within the electronics industry continues across the PCB design organizations I’ve participated in. It seems as though 12 different designers will always give you 12 different ways to approach a design challenge. That’s not necessarily a bad thing. However, when choosing to adhere or reject to any of the 12 ways, I always want to hear first about how doing so will help the project meet an industry specification. I always say that a good PCB designer needs to see a dozen different ways of solving a design problem. However, great designers—those whose eyes are set on volume production—will draw only from ways allowing them to create and specify design solutions conforming to an inspectable IPC standard or collaborate with others to create one if it doesn’t to exist.
When I think about the need to learn more about PCB industry standards—where to find them, how to access them, and how helpful the layout of this checklist has been for me—another one of Mr. Fenoglio’s woodshop sayings comes to mind. This one is about storing valuable tools: “A place for everything, everything in its place.”
This column originally appeared in the October 2023 issue of Design007 Magazine.
More Columns from Target Condition
Target Condition: Floor Planning Without a FloorTarget Condition: The 5 Ws of PCB Design Constraints
Target Condition: Are Autorouters Friend or Foe?
Target Condition: From Dream House to Drill Files
Target Condition: Designing vs. Inventing
Target Condition: ‘Boomer to Zoomer: Do You Copy?’
Target Condition: Advanced Packaging Technologies—Look Before You Leap
Target Condition: My Anti-venom to PCB Cost Adders