-
- News
- Books
Featured Books
- smt007 Magazine
Latest Issues
Current IssueSupply Chain Strategies
A successful brand is built on strong customer relationships—anchored by a well-orchestrated supply chain at its core. This month, we look at how managing your supply chain directly influences customer perception.
What's Your Sweet Spot?
Are you in a niche that’s growing or shrinking? Is it time to reassess and refocus? We spotlight companies thriving by redefining or reinforcing their niche. What are their insights?
Moving Forward With Confidence
In this issue, we focus on sales and quoting, workforce training, new IPC leadership in the U.S. and Canada, the effects of tariffs, CFX standards, and much more—all designed to provide perspective as you move through the cloud bank of today's shifting economic market.
- Articles
- Columns
- Links
- Media kit
||| MENU - smt007 Magazine
Estimated reading time: 4 minutes
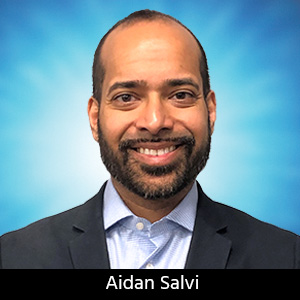
Facing the Future: Looking Ahead at Factory 5.0
Last month, I addressed the need for a change in PCB and electronics manufacturing and discussed the concept of Factory 4.0 and the business case for implementing the next iteration in American manufacturing: Factory 5.0™.
Factory 5.0 is the next evolutionary stage in the manufacturing industry. While Factory 4.0 was all about robotics, Factory 5.0 builds on the principles of Industry 4.0 by emphasizing human-centric collaboration, flexibility, and adaptability. It envisions a highly integrated and intelligent production environment where humans and machines work side-by-side, leveraging each other's strengths to achieve maximum efficiency, productivity, and innovation. What we now call “cobots” are collaborative robots, working in tandem with humans.
Changing market conditions, customer demand for increasingly personalized products, quicker delivery times, and high-quality standards necessitate the need for improved manufacturing processes and technologies. Factory 5.0 facilitates customization, enables rapid response to market changes, and ensures consistent quality through human and machine collaboration.
The need for Factory 5.0 originated as a response to the increasing demand for personalized products, rapid technological advancements, and the need for a more sustainable and adaptable manufacturing model. It signifies a shift from a purely technology-driven approach toward a more balanced combination of human ingenuity and advanced automation.
To understand Factory 5.0, we must first discuss Factory 4.0.
The advent of Factory 4.0, also called Industry 4.0, revolutionized manufacturing with the integration of digital technologies and automation such as artificial intelligence (AI) and the Internet of Things (IoT). Building on this foundation, Factory 5.0 represents the next phases of industrial innovation.
What is Factory 5.0?
Factory 5.0 is a new paradigm that fuses advanced technologies like AI, IoT, big data, robotics, and cloud computing with human expertise in the manufacturing process. This is significant, as these technologies work in partnership with humans. It’s a key advances to go from Factory 4.0, which significantly lessened the need for the human element. The Factory 5.0 paradigm centers on robots cooperating with humans, and humans learning how to work with robots. Additionally, it embraces the convergence of physical systems and digital technologies to create smart, interconnected, and highly flexible factories.
What is the Origin of Factory 5.0?
Factory 5.0 an evolution of Industry 4.0 which originated in Germany in 2011. The term “Factory 5.0” gained prominence later, highlighting the transition from purely automated factories to human-centric and highly connected production environments.
The Future of Manufacturing
Factory 5.0 represents a paradigm shift in manufacturing, enabling a more efficient, agile, and adaptable production system. It offers the potential for personalized mass production, decentralized manufacturing, improved sustainability, and enhanced customer-centricity.
The Enhanced Role of the Employee
In Factory 5.0, the role of the employee becomes pivotal. Rather than being replaced by automation, workers collaborate with smart machines, leveraging their creativity, problem-solving abilities, and domain expertise. Employees act as facilitators overseeing and optimizing the overall manufacturing process, while intelligent machines handle repetitive or hazardous tasks.
Advantages of Factory 5.0
Factory 5.0 benefits include flexibility that allows for rapid reconfiguration of production lines, thus facilitating the customization of products to meet individual customer demands. Factory 5.0 provides greater efficiency through the seamless integration of digital technologies and automation. Smart factories also respond rapidly to market changes, adapting production volumes, product variants, and delivery times accordingly. By leveraging AI and IoT, workers can collaborate more closely with machines resulting in higher productivity and improved safety.
What Factory 5.0 Means for Future Companies
Factory 5.0 enables companies to become more competitive in a rapidly evolving market. It fosters innovation, increases responsiveness to customer needs, lowers production costs, and enhances overall productivity, ultimately making companies more efficient, customer-responsive, and profitable. Companies that embrace Factory 5.0 are poised to thrive in an era of hyperconnectivity and digitalization.
What Factory 5.0 means for U.S. Manufacturing
Factory 5.0 has significant implications for U.S. manufacturing companies. By adopting these advanced technologies, companies can gain a competitive edge, improve productivity, and create high-value jobs. Increased automation and integration of digital technologies in manufacturing processes can help revitalize domestic manufacturing capabilities, boost exports, and reduce dependence on foreign production. Factory 5.0 will help American manufacturers become more competitive in the global market.
Ultimately, Factory 5.0 represents a significant transformative shift in American manufacturing capabilities. By combining human expertise with advanced technologies, we thus create intelligent, adaptable, connected factories.
Our manufacturers can for the first time in decades look forward to experiencing increased efficiencies, flexibility, and responsiveness, empowering both employees and companies to thrive in the digital age. Factory 5.0 has the potential to revolutionize U.S. manufacturing, enhancing competitiveness, driving economic growth, and shaping the future of the electronics manufacturing industry.
In next month’s column, we will discuss how Factory 5.0 will encourage, attract, and engage the next generation of talent to join our ranks. Later in this series, I’ll discuss how synergistic cooperation with our suppliers, customers, and even our competitors will help all manufacturers to rise to a new level of success. I hope you will continue to join me in this adventure.
Aidan Salvi is the chief transformation officer for Amitron Corporation.
More Columns from Facing the Future
Facing the Future: Engaging a New GenerationFacing the Future: American Manufacturing on the Rise