-
- News
- Books
Featured Books
- smt007 Magazine
Latest Issues
Current IssueSpotlight on India
We invite you on a virtual tour of India’s thriving ecosystem, guided by the Global Electronics Association’s India office staff, who share their insights into the region’s growth and opportunities.
Supply Chain Strategies
A successful brand is built on strong customer relationships—anchored by a well-orchestrated supply chain at its core. This month, we look at how managing your supply chain directly influences customer perception.
What's Your Sweet Spot?
Are you in a niche that’s growing or shrinking? Is it time to reassess and refocus? We spotlight companies thriving by redefining or reinforcing their niche. What are their insights?
- Articles
- Columns
- Links
- Media kit
||| MENU - smt007 Magazine
Estimated reading time: 7 minutes
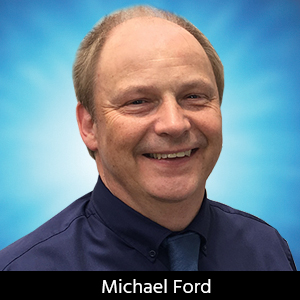
Smart Factory Insights: Today’s Manufacturing Jobs Require a New Skill Set
Manufacturing encompasses a great number of roles, each requiring different strengths, skills, and personalities. Now, each of these roles is being transformed and elevated by computerization, software, and AI. It is natural then, that to attract people to take on these roles, we must include those who are strong in the application and use of modern software, and which complements their incumbent skills and experience.
My own interest in manufacturing came from the excitement of seeing new and innovative consumer products, which as a student, I knew I couldn’t afford. Thus it was compelling to have the opportunity to be involved in how they were made—and perhaps pick up some staff discount. At the time, having only sufficient manual dexterity to handle a keyboard and mouse, the emergence of software development for manufacturing seemed to be the right place for me. In that role, I quickly realized the profound change that software would make in manufacturing as a microcosm of the world at large.
It's been as I predicted: Changes to the varied roles in manufacturing have been evolutional, each on a journey, from the analog “people and machines” world to a digital world. While core manufacturing knowledge remains important, best practices around the ways that things are done have changed drastically. This has made roles in manufacturing far more enjoyable and fulfilling than ever before. Let’s look at some examples.
Production Operators
Being a production operator once meant doing a series of repetitive operations, powered by muscle memory, and the mental ability to survive the tedium and monotony that high volume mass production entailed. As lot sizes reduced, changeovers in products became more frequent, requiring more thought and effort to avoid mistakes. Assembly work was both boring and stressful, something the human skill set can find impossible to perfect.
In the Smart factory, the assembly role has become a far more immersive experience and a key part of the engineering and manufacturing value chain. Interactive work instructions have made assembly operations, no matter how complex or changeable, more dynamic because of their easy-to-follow instruction and reference information. Using software, the composed operator environment fits exactly with the operations to be performed, eliminating the need for specialist, inflexible, product-centric skills. Feedback of completions, results, and interaction with engineering and managers elevates assembly operators into an active part of the manufacturing operation, with all the stress factors relieved or removed.
Manual assembly in the Smart factory need no longer be monotonous or boring. Operators are now flexible and dynamic enough to meet agile targets across a variety of tasks, and are the most flexible and reliable Smart asset in the factory.
Production Engineering
Engineers who were entering the world of manufacturing also found themselves unexpectedly having monotonous work assignments. Within an operational factory, and with established production configurations and engineering practices, production engineers had little chance for creativity. The ongoing need to process design and bill of materials (BOM) data, re-engineer it to gain consistency and make sense, then split it out across the various processes within the designated configuration (creating all the different formats of data and work instructions, often using little more than magic markers to color code prints), became overwhelming and frustrating. Even as their engineering degrees hung on the walls of their cubicles, they realized they had little time for the consideration of real engineering improvements, despite changing production requirements that addressed the need for agility.
Initial engineering software tools sought out to help process, mistake-proof, and merge product data from various sources, almost all of which came in the form of independently unstructured data. Engineering point-solutions reduced engineering lead times, the savings of which were quickly negated by the increase in product numbers and mix that needed to be processed. The potential for mistakes, both in the format and presentation of the source data, as well as forcing assumptions to be made without having complete information, did nothing to relieve the stress and burden on engineering, making it impossible to give up the old practices of manual checks and balances that had been put into place.
In today’s Smart factory, design data is available in an intelligent single-file standard format, such as IPC-2581, rather than as a copy of an output data stream to a plotter. The BOM data is available through software APIs, rather than as a translation of a format destined for a dot-matrix printer. The creation of the digital product model is now automated, ready for immediate application using composable interfaces for work instructions and machine data. Removing the potential for mistakes and eliminating needlessly repetitive workload allows engineers to embrace agility and make decisions dynamically to select the best configurations for the job based on live availability, capability, through-rates, and quality performance.
Manufacturing engineering now becomes dynamic and exciting, using software tools that allow creativity without the stresses and tedium of manual data manipulation and processing.
Production Management
The production management effort once consisted predominantly of a series of meetings, each with a siloed group within manufacturing, including quality, materials, line supervision, and planning. Each group brought different, yet conflicting views and goals that confused and delayed management decisions that would directly affect overall factory performance. Ironically, the more information management sought out to make decisions, the more time lost by production operators because they had to record everything they did. This created a negative spiral of motivation all around.
In the modern, Smart factory, operational information comes automatically in two parts. Using software interfaces, the data collection from both machines and human operations improves timeliness, quality, detail, and consistency. The important, but often overlooked second step, is the contextualization of that data to build a meaningful visibility of performance, based on the knowledge of the product and production configuration. The use of modern MES software tools constructs and brings this visibility consistently to all manufacturing groups, which are now all on the same page. Decision making is done rapidly and through teamwork, rather than arguments. Production management are now orchestrators of efficient, rapid transitions, aided by execution management software tools—a far more enjoyable and added-value role.
Materials
Managing the flow of materials in production was once a near impossible mission. Creating kits of materials, often several work-orders in advance across every production configuration, was a lot of work, leading to stress caused by often missing or insufficient materials. With spoilage and attrition causing differences between ERP-based inventory stock levels and the physical stock, frequent unexpected shortcuts, planning changes, and un-kitting and re-kitting were necessary. Knowing that a single mistake in such an environment would likely have a catastrophic impact on product quality, as well as the cost to the business of excess material investment, meant that anyone with a materials responsibility was continuously under extreme pressure.
In the modern, Smart factory, material consumption and spoilage are automatically monitored, and physical quantities are synchronized with ERP. Kits are no longer required, with automated “just in time” material selection, delivery, and setup verification at each stage of transport and use. Unexpected material shortages, logistics bottlenecks, lost components, and uneven work-load issues are avoided, allowing flexible, stress-free materials management that follows information generated dynamically to meet exact production needs. All this is driven, managed, and monitored by the modern MES solution.
Quality Team
In many cases the most stressful of all roles in manufacturing is as a member of the quality team. Defects disturb the production flow, creating unexpected work, and potentially delaying delivery. The goal of zero defects, solely through manual effort has always been elusive, with QA checks and controls, testing and inspection all detracting from added-value operations. This serves only to reduce the number of defects, not eliminate them.
In the Smart factory, the role of the quality team is elevated to focus on analysis of operational data captured automatically from assembly, inspection, and test equipment as well as manual operations. Exposed deviations and variation in manufacturing are the root causes of defects. Creativity to modify processes and put into place corrective and preventative action plans has now become a major part of the quality role. Avoidance of quality risk represents a far more positive and exciting contribution to manufacturing as compared to the triage of defective products.
Summary
These examples are just a few illustrations of how manufacturing roles have evolved from being specialist, hands-on, repetitive, and often boring work within an inflexible organization, to being data-driven, creative, and dynamic. Similar transitions could be illustrated for other roles, including maintenance, IT, warehouse management, and the plethora of data collection and entry roles, which often go unfulfilled due to more pressing priorities. The use of software to automate routine work frees up human intelligence in the manufacturing organization, avoiding conflicts and establishing multi-discipline teamwork, all coordinated through the intelligence within software.
The use of software has become a natural ability for the next generation of the workforce, which complements existing manufacturing skills and experience, creating a 1 + 1 = 3 value. This represents the scope for intelligence, insight, and creativity for young people entering manufacturing today. The challenge, however, is for the existing production team to be open to, and in fact, drive this combination of know-how, enabled by using modern manufacturing software tools.
This column originally appeared in the November 2023 issue of SMT007 Magazine.
More Columns from Smart Factory Insights
Smart Factory Insights: Making Rework a Smart Business OpportunitySmart Factory Insights: The Sustainability Gold Rush
Smart Factory Insights: Compose Yourself, Mr. Ford
Smart Factory Insights: The Smart Business Case for Local PCB Manufacturing
Smart Factory Insights: Manufacturing Digital Twin—Spanners in the Works
Smart Factory Insights: Machines, People, and AI
Smart Factory Insights: Is Sustainability in Manufacturing a Benefit or Burden?
Smart Factory Insights: Manufacturing Meets the Flintstones