-
- News
- Books
Featured Books
- smt007 Magazine
Latest Issues
Current IssueSupply Chain Strategies
A successful brand is built on strong customer relationships—anchored by a well-orchestrated supply chain at its core. This month, we look at how managing your supply chain directly influences customer perception.
What's Your Sweet Spot?
Are you in a niche that’s growing or shrinking? Is it time to reassess and refocus? We spotlight companies thriving by redefining or reinforcing their niche. What are their insights?
Moving Forward With Confidence
In this issue, we focus on sales and quoting, workforce training, new IPC leadership in the U.S. and Canada, the effects of tariffs, CFX standards, and much more—all designed to provide perspective as you move through the cloud bank of today's shifting economic market.
- Articles
- Columns
- Links
- Media kit
||| MENU - smt007 Magazine
Estimated reading time: 12 minutes
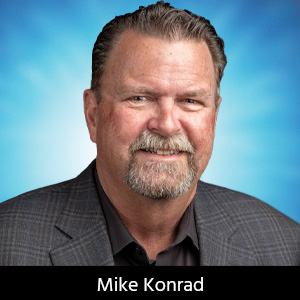
The Knowledge Base: The Pivotal Role of Optimization
In the fast-paced realm of electronics production, where innovation is relentless and competition is fierce, the pursuit of optimization and efficiency has become the cornerstone of success. As technology evolves at an unprecedented pace, manufacturers face the dual challenge of meeting increasing demands while maintaining high quality standards. This month, I delve into the intricate landscape of electronics production and explore the pivotal role that optimization plays in driving efficiency across the entire manufacturing process.
I invited Patrick Stimpert, vice president of operations at Matric Group, to share his view on, and experience with, optimization and efficiency within the electronics manufacturing space. We navigate through the complexities of optimizing supply chain management, enhancing production workflows, and implementing cutting-edge technologies to minimize waste and maximize output.
Can you describe your experience with electronics assembly processes, including any specific projects or achievements related to process optimization?
Patrick Stimpert: I have been directly involved in the electronics industry for 10-plus years, from the conceptual design phase to manufacturing, go-to-market strategy, and delivering finished products to the customer. I’ve learned that the electronics industry is widely diverse and evolving at a lightning-fast pace. How fast is that change? In the time it takes to declare that a process or design is perfect, the industry has already moved past you. The industry can have long days that spill into quick weeks and create very short years, so why would a person want to be part of this? Because it's short-fused problem-solving with creative, intelligent people who only need to be pointed toward success.
One day, you may find yourself at a lunch, sitting across from C-suite executives at one of the world's largest transportation manufacturers and they need a problem solved. As they explain the issue, the scheduling department is giving you a few text messages to update and expedite one of the channels of the products you offer. Because you have the team focused on the importance of the voice of the customer, they can expedite it through the shop, change the BOM, update the router, reset the controls package, and even powder-coat the assembly to the customer's needs. By the time lunch with the customer ends, your team enters the room and tells the customer about the performance of the sample they just produced for them.
When that happened to me, it was the moment I knew I could effectively vertically stack flexible manufacturing, leaving room to inspire creative problem-solving for the customer.
What methods and tools do you typically use to analyze and identify inefficiencies in an assembly process?
Stimpert: My fundamentals are based on the Toyota Production System, grounded in a realistic understanding that results matter, and everyone reports to the P&L. I have always embraced process guardrails in safety, quality, and reliability operations. All three need layered checks and balances, with Gemba1 visual management boards in each department or critical process step. Accountability at all levels starts with the “Up and to the Right” program that each integral operator or leader completes daily. The daily emails tell the good, bad, and ugly to all key stakeholders. The magic is that everyone knows that the program only remains credible if you do something with what you learned. This is the foundation of opportunities for improvement (OFI), or rapid improvement program (RIP), a tremendous continuous improvement program. The next steps are the weekly, monthly, quarterly, and yearly KPIs used to track our fundamentals. The most important parts of this process are the daily stand-ups and GEMBA walks. Remember, the associates are always watching and taking note of your actions or, worse, remembering the non-action.
Could you provide an example of a situation where you successfully improved the efficiency of an electronics assembly process? What specific steps did you take and what were the results?
Stimpert: Five years ago, we set a goal to improve SMT line yields to improve throughput. This project started with not accepting the industry standards which said that for parts placed per hour in a contract manufacturer with a high mix, low volume, 19–21% overall line up-time is excellent. Do you realize that's like the Mendoza Line in baseball where you get sent back to the minors?
We identified vital waste problems that needed a fix: line change-over time, line stall time, parts reel change validation, human intervention, exception calls requiring validation after the final AOI, and standardizing all go/no-go calls the same across all AOIs. Let me describe these in more detail.
Line changeover time: Do you have the correct pit crew to win the race? The industry is first coming to grips that high mix can be overcome with family set-ups to maximize feeder positions, a screen print that could host several screens that will conduct an auto change-over to the new screen with the new job, so now we have a 4.0 standard started to make line changes automatically up and down the line.
Line stall time: Someone needs to coin a catchphrase for this one. You can't achieve a placement time percentage if every occasional fault stops the line. After each optical inspection, we installed inline stackers to push the fault to the side and keep the line moving.
Parts reel change validation: Humans make mistakes. We have installed pre-flow AOI to check rotations and 100% compliant placements. This was a simple ROI measure of your rework on double-sided high, populated small-size parts when you apply an iron to fix something. I can wipe a board, reclaim the expensive parts, and re-run it cheaper than the rework adventure.
Human interventions: The new package sizes leave little room for errors, and the operators/process technicians always modify programs with good intentions, but the programs have very open-ended subjective inspection parameters. Here's a good example: A 1% contrast adjustment on a standard X-ray camera can swing the voiding scale more than 10%. Sleep well, quality engineers, now that you know.
Exception calls: These are the calls that the AOI has been programmed to ignore or bypass because the AOI and 3D camera remodeling can't produce a predictably correct result. In these situations, the industry does one of two things: Whistle through the graveyard and give it a false call pass or flag the PCB as a failure to have a manual visual conducted offline; when that's done, you need to run it through a final go validation. We decided to partner with Koh Young and have them stop the PCB before the post-AOI to inspect and capture the validation of the exception in the Koh Young database. Now, a post-AOI good call needs nothing else but to have the job moved on to the next manufacturing step. Go/no-go makes the calls the same across all AOIs. I joke that something is wrong if you have a chair in front of an AOI. To fix this problem, we deployed KSMART Solutions. We now have one person monitor all 15 AOIs in the war room, and they make all the calls. If it needs further review, an alert is sent out to the process technician or QA to expedite the call.
How do you approach balancing the need for process efficiency with the requirement for maintaining high-quality standards in electronics assembly?
Stimpert: Ask these two questions often: “Why?” and “Does this process add value that we get paid for?” A good rule is to never be confused for a nonprofit. Process efficiencies always start with fundamentals; this should be monitored with any safety-associated costs recognized or, worse, the unrecognized hidden costs.
Quality (QMS) is next, with a foundation that uses the voice of the customer program or, as we call it, "escapes." Listen to what the CAR and SCAR tell you; this should match the MRR logs used by production.
New production review (NPR) should demand engineering design for full-functional testing that includes sign-of-life testing and uses this testing to produce a COC that reduces in-field risk. The third and final approach is reliability. The guardrail here: If safety or quality is not world-class, why talk about going faster? The cost of rework always outweighs the increase in speed. I always turn the reliability conversation into this: Hold up your promise to internal and external customers; we will maintain margin if we are safe, build with excellent quality, and keep our promises.
In your opinion, what are the most common challenges in optimizing electronics assembly processes, and how do you address them?
Stimpert: Waste is the most common challenge. My favorite rule in manufacturing is, “Stop rearranging deck chairs on the Titanic. Just fix the problem.” How do you stop this from happening and focus your team? The first question in every meeting should be, “What problem are we here to solve?” The second is, “What do we know about this problem?” Stop the meeting if you don't have a problem to solve, and politely ask people to leave if they can't add value to the discussion. Optimization requires risk from leadership and overcoming fear of the unknown of changes. It's faster to make 100 small changes than one significant, preplanned change. Why? It's the upfront emotional investment and pride. You must be willing to try and fail, but fail quickly and cheaply, adjust, and try again. That's how humans learn.
Have you worked with automated equipment or robotics in electronics assembly? If so, can you share your experience and any successful implementations?
Stimpert: One of the first undertakings here at Matric Group was to solve the challenge of speeding up component handling accurately and efficiently for the surface mount technology (SMT) placement lines. The overall handling is simple: fulfilling the BOM that is typically 250–300 different components on 10 to 15 changeovers a day on time and accurately. The complexity comes from equipment for medical, aerospace, and others to have complete lot tracking and moisture controls on components.
At Matric Group, those requirements have a combination of 3,750 reels, trays, tubes, and strips being picked and set up daily; 3,700 more staged in front on the SMT lines or actively consumed; and the final 3,750 are being actively removed from the equipment with remaining quantiles being a stock return. If the CFO is reading this and feeling uneasy, it is because there are 5.6 million components hanging out in the work-in-process. Solution: We partnered with Juki Storage Systems as well as Nordson's Assure X-ray counter to meet our requirements, which are also seamlessly expandable. This project reduced labor by 85%, and we completed the ROI in less than one year.
What strategies do you employ to ensure the timely availability of components and materials for the assembly line, reducing downtime and production delays?
Stimpert: The onset of COVID and the two-year international supply chain disaster have realigned my vision and the practicability of just-in-time inventory. The “ready” and “set” seem way more important than the “go.” One of the biggest misleading statements is “all parts here” (APH). This doesn't mean you can release and build.
Every ERP system has known programming faults that can hold up the job release. I have always deployed visual management boards to overcome the trapdoors and create a robust material review program (MRP) with one standard rule: No one gets to just come to the meeting and report the news. The program must require all bottlenecks to be solved by the key shareholders in each department. The weekly meeting needs to be with customer service, sales, scheduling, QA, manufacturing engineers, and top-level leadership. The second lesson learned in the last three years is to control your destiny. Internal and external sourcing are preferable to dual external sourcing, but both are better than external single sourcing.
How do you assess and minimize defects or errors in the assembly process, and what tools or methodologies do you use for quality control?
Stimpert: Most importantly, in any manufacturing process, set and enforce a culture that, “No one is allowed to pass on bad quality.” To improve our first-pass yield and final yield, we needed to slow down and have proper gates and guardrails. It seems counterproductive to make a margin, but the alternative is rework.
The speed of today's technology can produce two things: a large amount of high-quality electronics or a quickly produced “rework mountain.” Our learned lesson came from having to buy more racks to stack up the avoidable margin erosion. To solve this problem, a safety gate was created for first-piece inspections with AOIs, X-ray, and flying probe inspections. Yes, we run the first few PCBs to get to the golden board condition before we release the complete run. We also repeat this process between shifts. We found that we can outperform standards for the entire build by getting to and maintaining a 99.95% or higher SMT yield.
Can you discuss any experience you have with Lean manufacturing principles or continuous improvement methodologies in the context of electronics assembly optimization?
Stimpert: Individual ownership of the process ignites enthusiasm, which is contagious in a manufacturing building. We use our GEMBA daily meetings for feedback and encourage using our suggestion ECM (engineering change management) program. We found that when an associate has easy access to documents and tracks the progress of their suggestions, it sets in motion a robust continuous improvement program that maintains its momentum. The recommendations ECM submits are reviewed by the manufacturing engineers, who are also responsible for giving feedback to the associates.
How do you stay up to date with advancements in electronics assembly technology and manufacturing best practices? Can you give an example of how you have applied this knowledge to improve an assembly process?
Stimpert: The Toyota Production System has a core fundamental: learn by sharing ideals. My lesson learned is to listen before you speak. The amount of free educational opportunistic training is overwhelming right now. The quality of podcasts and interviews with my peers is a mountain of treasures. Take the time each week to learn something and encourage learning in your company uncomplicatedly. Ask your leaders each Friday in a group: This week, what went right, what went wrong, and what did you learn? Manufacturing needs levity; today's problem is not tomorrow's problem, and people need to vent and mostly have fun.
References
1. Gemba is a Japanese word meaning “the actual place.” In Lean practices, it refers to the place where value is created. In manufacturing, for example, Gemba is the factory floor.
This column originally appeared in the December 2023 issue of SMT007 Magazine.
More Columns from The Knowledge Base
The Knowledge Base: A Conference for Cleaning and Coating of Mission-critical ElectronicsThe Knowledge Base: Building the Workforce of Tomorrow With EMAC
The Knowledge Base: Beyond the Badge—Why Membership Matters More Than Ever
The Knowledge Base: Unlocking the Invisible—The Critical Role of X-ray Technology
The Knowledge Base: At the Forefront of Electronics Manufacturing
The Knowledge Base: Challenges and Considerations of Harsh Environments
The Knowledge Base: My 2025 Industry Wish List
The Knowledge Base: The Era of Advanced Packaging