-
- News
- Books
Featured Books
- smt007 Magazine
Latest Issues
Current IssueThe Rise of Data
Analytics is a given in this industry, but the threshold is changing. If you think you're too small to invest in analytics, you may need to reconsider. So how do you do analytics better? What are the new tools, and how do you get started?
Counterfeit Concerns
The distribution of counterfeit parts has become much more sophisticated in the past decade, and there's no reason to believe that trend is going to be stopping any time soon. What might crop up in the near future?
Solder Printing
In this issue, we turn a discerning eye to solder paste printing. As apertures shrink, and the requirement for multiple thicknesses of paste on the same board becomes more commonplace, consistently and accurately applying paste becomes ever more challenging.
- Articles
- Columns
Search Console
- Links
- Media kit
||| MENU - smt007 Magazine
Save Your Design by Understanding Fab Processes
January 16, 2024 | Andy Shaughnessy, I-Connect007Estimated reading time: 7 minutes
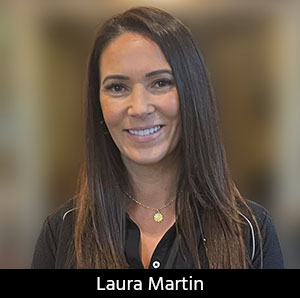
At PCB Carolina, I met with Laura Martin, director of applications engineering for Summit Interconnect. Laura has been at Summit for about a year, moving into the role from a similar position at Insulectro. She has now become Summit’s go-to design for manufacturing (DFM) expert, and she’s working to move DFM further up in the design cycle, eliminating unpleasant surprises at CAM.
Many DFM issues stem from designers not understanding all the steps in the manufacturing process. I asked Laura to share her thoughts on this situation, and she had several pointers for designers. As she notes here, many fab variables can put your board on hold, so it’s best to be prepared.
Andy Shaughnessy: What are some of the most important things a designer should know about fab?
Laura Martin: One of the most common DFM findings is the via or plated through-hole pad size is designed too small to meet the specified annular ring requirements. I don’t think it’s well understood how to calculate the correct pad size, and IPC documents don’t include some of the manufacturing caveats. We did a webinar on this topic recently, and one of the things we covered is how the type of final finish impacts the drill diameter. We compensate the drills differently for HASL and ENIG finishes. We also consider the aspect ratio of the board, and the total thickness or thickness of each sub being drilled.
If a copper plating thickness beyond IPC requirements is specified, that additional plating can impact the drill diameter we choose. So, it's not as easy as using the IPC formula to calculate the minimum pad size. Unless you know what the fabricator will choose for a drill diameter, then you might be off on your pad size calculation, which is why partnering with a fabricator when you're beginning your design is very important. The last thing you want to do is complete your entire layout, release it, send it to get fabricated, and suddenly the fabricator says, “You have to change the pad size.” That can have a major impact on your layout, and you may have to allow exceptions to your annular ring requirements if you can’t update your design.
Another common DFM finding is copper spacing. Most people know how to design for half-ounce, one-ounce, or two-ounce copper on print-and-etch layers, but internal and external plated layers are not as simple. Plating and fabrication processes can vary when there are multiple hole structures like buried vias, microvias, plated through-holes, or epoxy-filled holes. These features can impact the minimum spacing needed on the plated layers. Oftentimes, internal and external plated layer design requirements are not straightforward because they depend on the way the board will be fabricated. Is it getting planarized? Is it getting button-plated? How much copper will end up on each plated layer after processing? Not having enough spacing for fabrication can result in electrical shorts and low yield, so collaborating with the fabricator from the get-go is crucial. Frontloading this communication can prevent major hiccups down the line.
Shaughnessy: That's interesting. Even if the designers are following IPC specs, it's still possible to get things wrong if you don't work with your fabricator, because you may not be aware of their capabilities or limitations.
Martin: Exactly. Boards are becoming so complex that you have to work with the fabricator now. On a simple single lamination, with only plated through-holes, the fabrication process is pretty straightforward. But when you start getting into multiple lamination cycles, internal plated layers, and multiple-hole structures, it becomes more complex to fabricate.
Shaughnessy: Fabricators joke about how designers get all the matched impedance stuff right, but they’ll put a connector too close to an edge or a component in the bend zone of flex. It seems like these little board-level errors put many jobs on hold.
Martin: Yes, there are many things that can put a board on hold. That's why having DFM up front is becoming so important. Many customers just expect it because they know that will catch most of the issues before they go into fabrication. So, we're trying to rise to that occasion and offer multiple solutions. Some customers just want a quick DFM, and that's good enough for them. Other customers want an in-depth review. By offering multiple solutions, we can provide that extra service.
Shaughnessy: Laura, I saw you last year at PCB Carolina, and since then you’ve moved into a new job at a new company. Tell me about your past year.
Martin: Shortly after last year’s show I transitioned to Summit Interconnect as director of applications engineering. It's been an exciting journey as I assumed the responsibility of leading a department focusing on recruiting and training field application engineers. Our mission is to excel in technical support and customer service. Over the past year, I've enjoyed the process of establishing a department, introducing new processes, and innovating the way we approach DFM for our customers.
Traditionally, DFM has been a somewhat ambiguous concept in the industry. Designers often toss their designs over the wall and request a DFM without a clear understanding of what it entails. Many perceive it as a tooling department activity, involving running scripts, planning the job, and identifying issues in a technical query. While this is valuable, it consumes front-end engineering resources and may result in prolonged back-and-forth exchanges with the customer on design updates.
To address this, my team intervenes at the initial stages of the design process, even before it reaches the CAM department. One innovative solution we offer is called “preliminary DFM.” This involves a semi-automated review where we thoroughly examine all design requirements. The ensuing report allows us to provide valuable insights, such as assuring designers that their design is manufacturable or identifying potential design rule violations. In cases where adjustments are needed, such as increasing pad sizes to meet annular ring specifications or addressing challenges in etching small spaces on specific copper weights, we can intervene proactively.
This approach ensures that potential issues are tackled before the design is released or sent into manufacturing, preventing the common cycle of revisions and updates. Designers benefit from a personalized, one-on-one interaction with our team, leveraging our expertise in design for manufacturing and our in-depth knowledge of each of our shops’ capabilities. Essentially, we aim to provide customized solutions that address a variety of needs.
Shaughnessy: With preliminary DFM, you’re getting designers and fabricators to communicate, which isn’t always the case. What are customers saying about this?
Martin: It’s been received very well by customers. They appreciate the quick and insightful assessment of their designs, giving them confidence before committing to a full tooling DFM. It's a win-win situation. We avoid using up our front-end engineering resources on designs that might need extensive revisions, and designers get a more efficient, one-on-one interaction that addresses their specific design.
Shaughnessy: At last year’s PCB Carolina, you were teaching a class on fabrication for designers.
Martin: Yes, that was my PCB 101 class. It delved into the basics of board fabrication, all the way from raw material to laminating, drilling and plating, and final finishes.
Shaughnessy: Are you an electrical engineer?
Martin: My academic background is in industrial engineering with a focus on manufacturing. It turned out to be a perfect fit for my journey. I started as a technician at an OEM, learning hands-on board building without a degree. After transitioning into front-end engineering, I pursued my engineering degree part-time. By the time I graduated, I had already gained a deep understanding of DFM and board fabrication. It was a seamless integration of knowledge and experience.
Shaughnessy: What are your plans for 2024?
Martin: The past year has been a whirlwind, and there's so much opportunity at Summit. Our focus on automation, customer obsession, and making the design-to-manufacturing handoff seamless are driving positive changes. I'm excited about the future and the chance to continue serving our customers in the best possible way. I feel like I'm just getting started, and there's so much more to accomplish in this dynamic and enjoyable industry.
Shaughnessy: It is a great industry. Thanks for speaking with me, Laura.
Martin: Thank you, Andy.
This article originally appeared in the January 2024 issue of Design007 Magazine.
Suggested Items
PCB Designers: Enhance Your Listening Experience With New Companion Download to the DFR Podcast Series
11/11/2024 | I-Connect007Exciting news for listeners of On the Line With... Designing for Reality, the popular podcast series hosted by I-Connect007. A 10-page companion guide featuring insights from ASC Sunstone’s expert Matt Stevenson is now available for download.
BOOK EXCERPT: The Printed Circuit Designer’s Guide to... DFM Essentials, Introduction
10/16/2024 | I-Connect007 Editorial TeamDesign for Manufacturing (DFM) is defined as the practice of designing printed circuit boards that meet not only the capabilities of the customer’s assembly manufacturing process, but also the capabilities of the board fabrication process to provide the highest reliability at the lowest possible cost.
Routing, Final Fab, and QC: Don’t Miss the Final Episode of On the Line With… Designing for Reality
09/23/2024 | I-Connect007Don't miss the final episode of "On the Line With… Designing for Reality," in which ASC Sunstone General Manager Matt Stevenson wraps up his deep dive into the PCB manufacturing process with a discussion of Routing, Final Fabrication, and Quality Control.
ASC Sunstone Circuits to Exhibit at the Anaheim Electronics & Manufacturing Show (AEMS) 2024
09/16/2024 | ASC SunstoneAmerican Standard Circuits | ASC Sunstone will be exhibiting at the Anaheim Electronics & Manufacturing Show 2024 to be held October 2-3 at the Anaheim Conventions Center in Anaheim, California.
Surface Finish: Tune in to the Latest Podcast Episode of On the Line with… ASC Sunstone
09/04/2024 | I-Connect007Don't miss the latest episode of "On the Line with… ASC Sunstone: Designing for Reality," in which ASC Sunstone’s General Manager, Matt Stevenson, discusses the critical topic of surface finishes in PCB manufacturing.