-
- News
- Books
Featured Books
- smt007 Magazine
Latest Issues
Current IssueSupply Chain Strategies
A successful brand is built on strong customer relationships—anchored by a well-orchestrated supply chain at its core. This month, we look at how managing your supply chain directly influences customer perception.
What's Your Sweet Spot?
Are you in a niche that’s growing or shrinking? Is it time to reassess and refocus? We spotlight companies thriving by redefining or reinforcing their niche. What are their insights?
Moving Forward With Confidence
In this issue, we focus on sales and quoting, workforce training, new IPC leadership in the U.S. and Canada, the effects of tariffs, CFX standards, and much more—all designed to provide perspective as you move through the cloud bank of today's shifting economic market.
- Articles
- Columns
- Links
- Media kit
||| MENU - smt007 Magazine
Estimated reading time: 5 minutes
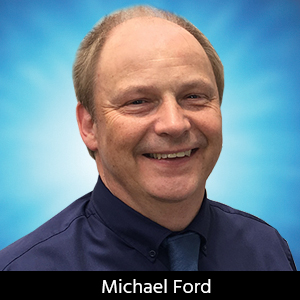
Smart Factory Insights: Making Rework a Smart Business Opportunity
Rework in manufacturing can bring waste, unplanned responses to an error, or too much variation. You also have to retain specialist skills to perform the work. Since rework cannot always be completely eliminated, let’s consider how we can create a new business opportunity.
The strive for zero defects has been going on forever and will perhaps always remain elusive. There will always be a risk for mistakes to be compounded in the market. Thus, inspection and test are that all-important filter to assure (to a reasonable extent) no immediate defects leave the factory. Analyses of inspection and test data, as well as machine performance, can detect the root causes of potential defects, and provide automated closed loops.
The Smart Approach to Quality in Management
The main role of inspection and test in the Smart factory is no longer just to discover defects but is an active part of quality management in preventing defects. In some cases, as the rate of defects lowers, it may become more cost-effective to scrap defective units rather than repair or rework them, while building extra units into the work order to compensate. This is the state of the art for many, but not perfect, certainly in terms of material waste.
In most cases, defective products will need rework at some point, so you must prepare. But the cost of skilled engineers does not decrease with the reduced number of defects. Instead, these key people have more free time and it’s challenging to utilize them effectively as other jobs in manufacturing don’t require their specific skills. When there’s not enough work to do, engineers become bored and search elsewhere for challenges. That’s when you need to look for a new solution.
What We Can Learn
Most of us today have grown to value the data in manufacturing in terms of how to understand the root causes of inspection and test failures, and help resolve weaknesses in manufacturing processes, including material choices and handling.
Learning from repair and rework is our final opportunity in manufacturing to gain a higher-level understanding of the health of the product design and production process. Though the design passes traditional design-rule checks, conditions remain that may be sensitive to the effects of variation and simple mistakes.
Subtle changes in design may avoid creating those conditions. Intelligence is required to expose design improvement opportunities, going well beyond the root causes of specific defects. Such determinations depend on complex contributors, for example, the capabilities of machines and manual processes, not just to execute the assigned work, but to understand how “comfortable” the work is. This can be quantified and measured, for example, by the amount of variation created in product completions, which increases as machines are pushed to their limits.
Some machines may place a certain component with ease, while another struggles. The mix of material sourcing for a specific component also plays its part, as slight deviations in shape and size from different vendors, or even different lots, become significant in terms of a cause for the variation. In times like these, where supply is constrained, there is a strong likelihood that materials selected and purchased may not match the original design intent. Whether such variation implies a problem or is a benign function of the material change, requires intelligence to assess. Many analyses differentiate the responsibilities of manufacturing operations, machine or operator performance, design, or material-influenced variation. Association and analysis of such variation in turn helps improve design, manufacturing planning, machine selection, material purchasing, and more.
It has been proven statistically that reliability rates for products in the market are directly related to defect opportunities in manufacturing. The dwindling opportunities for feedback from repair and rework in manufacturing, therefore, represent only the start of this opportunity.
In today’s design-for-demand driven economy, repairability is not a high priority. Products under warranty are simply replaced or a major component is swapped out. Beyond that, the product is usually discarded. Very little effort goes into troubleshooting what actually failed. Information about unknown and endemic weaknesses in products, which could have been addressed by subtle design changes, processes, or material choices, are lost to the designer and manufacturer who are simply told instead that the product performance did not achieve its design intent.
As our culture shifts from consumption to sustainability, the right to repair is emerging and receiving more support through government legislation. Sustainability advocates are pushing for products that last a lifetime, and have materials that can be recovered, recycled, and reused. The remanufacturing industry is predicted to grow and exceed that of original manufacturing. Designers need to start planning their future designs with this in mind, facing the prospect that some design information—for an uncontrollable number of third-party repair, recycling, or recovery operations, all of which have a legal right to obtain certain portions of the product design IP—will need to be shared. Rather than let this market opportunity develop at random, designers and their manufacturers should plan the part they will play and whether it will be beneficial to replace original manufacturing in terms of their growth with more managed market-based product repair, recovery, and recycling.
A growing and tangible opportunity exists for design and manufacturing partners to plan their remanufacturing operations. Their first step would be to create a business plan that uses existing and underutilized rework experts in manufacturing to create an in-house business for repairs, returns, and material recovery. Access to the original design and MES manufacturing data allows the streamlining of many maintenance, repair, and overhaul (MRO) activities. These can range from repairs, servicing for extended life (product as a service), repurposing into another product, recovery of key materials and modules, and the ultimate recycling of materials.
The advantage of taking a simple first step into in-house repair allows the discovery of what has contributed to the need for repair, in terms of usage, abuse, accidental damage, or product weakness caused by manufacturing or materials defects that could have been improved by design. It allows designers to refine the reliability of products and life expectancies based on real product usage. The result will be more reliable products in the market, reduced costs, and less need to share design information with third parties.
The concept of needless rework reduction is clear to those in manufacturing today, and potentially represents a forward-thinking business opportunity to those in the business chain. For some, this practice has been successful for many years. Advanced MES tools include MRO support, achieving the benefits of understanding design and manufacturing the original product in context with the need for repair or reuse. The remainder of the industry has not been so driven to follow suit, but that is changing.
This column originally appeared in the January 2024 issue of SMT007 Magazine.
More Columns from Smart Factory Insights
Smart Factory Insights: The Sustainability Gold RushSmart Factory Insights: Today’s Manufacturing Jobs Require a New Skill Set
Smart Factory Insights: Compose Yourself, Mr. Ford
Smart Factory Insights: The Smart Business Case for Local PCB Manufacturing
Smart Factory Insights: Manufacturing Digital Twin—Spanners in the Works
Smart Factory Insights: Machines, People, and AI
Smart Factory Insights: Is Sustainability in Manufacturing a Benefit or Burden?
Smart Factory Insights: Manufacturing Meets the Flintstones