Estimated reading time: 5 minutes
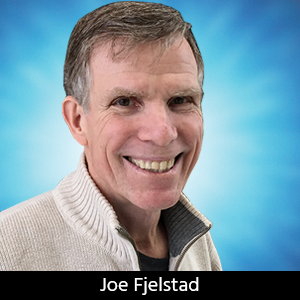
Flexible Thinking: What Matters When Designing Next-generation Products?
Since at least the 1970s, there has been a somewhat fungible mantra in electronics product development that has included two or more of the following descriptive adjectives: smaller, faster, lighter, better, and cheaper (often coupled with more rugged and reliable). Getting all of them simultaneously was not always possible, but if you paid enough, you could probably achieve it. However, it generally required the purchaser to give in to some commonly held “rules of the road” set down by the manufacturing community. When navigating the design process, what happens when the manufacturers want you to follow a road that does not take you where you want to go, or when standard practices are too constraining?
You can certainly decide to leave the path to gain benefits, but you should be aware of the risks and dangers that lie on the road less traveled. Robert Frost’s timeless poem about that road left the reader with the impression that the results of choice were good—or not if you couldn’t see the full length of the road ahead. With that in mind (and current knowledge), let’s try to create a roadmap of sorts to see what might be done to make sure we reach our desired destination in a constantly changing design and manufacturing environment. Full disclosure: This will not serve to map the myriad concerns facing electronic product designers, nor will it detail where all the problems lie. Still, I hope to provide some guidance on important issues facing PCB designers.
First, all PCB designs are typically custom and unique; they are one-of-a-kind products. Unfortunately, they are also considered commodities, making them a “custom commodity” (an oxymoron). That said, the designer can try to comply with the needs of a commodity, which is to attempt to keep the dimensions orthogonal, if possible.
I trust we have all seen odd-shaped PCBs: round, polygonal, and mixtures of the two. Recognize that these boards are produced on rectangular panels and that missing material winds up in the trash. It was paid for, thus the admonishment. Still, it is not uncommon that the board must be designed for a specific product, such as missiles, which are (for ballistic reasons) invariably round. Thus, round circuit boards are designed to fit.
In general, when an odd-shaped board is inescapable, it will be necessary to design it for manufacture using a rectangular piece of laminate of a standard size, which is what the industry is tooled to do. This is true for both PCB manufacture and assembly. Thus the designer’s odd-shaped design will not be manifest until it is freed from the assembled panel on which it was manufactured.
While on the general topic, it is highly advisable that designers invite themselves (or get invited) to visit their PCB provider before locking down their designs. We all read compelling stories about “bleeding edge” high-layer-count PCBs with line and space features of less than 75 mm, but is your vendor capable of such? This brings to mind other concerns relative to circuit performance, including one that has been increasingly important for the past few decades: controlled impedance and signal integrity. Dealing with these companion concerns requires the use of newer software tools that are designed to help address the challenges involving multiple material and feature design factors, including precision line dimensions, laminate dielectric properties makeup, and thickness. Even the “tooth” of the copper foil used can impact results.
Heat generation and its management are also of concern. There has been a tendency to pack more components into smaller spaces. This impacts the signal integrity concerns as well as the thermal density of the assembly. Increasing thermal density has become a higher-order concern for product developers. Thus, heat mitigation has steadily risen in importance because of a known inverse relationship between heat excursions and an electronic product’s reliability. Failure modes include solder joint reliability, plated through-hole integrity, and silicon chips’ longevity. Again, modeling and analysis tools specific to thermal characterization should be desirably included in the design tool software suite.
I’m sure most of you are aware of the continuing evolution of wireless products that are now an indispensable part of our daily lives. With increasing expansion of the electromagnetic spectrum for wireless use, designers must be attentive to the susceptibility of their products to electromagnetic interference (EMI) and its potential to emit electromagnetic radiation that could impact products that surround it. It’s increasingly important to learn how best to mitigate or eliminate these concerns, and the designer must learn the best grounding practices as well as how to employ the best shielding techniques and incorporate EMI filters. In general, they need to follow established electromagnetic compatibility (EMC) guidelines.
My last item on this much-abbreviated list is meeting regulatory compliance requirements, which can determine whether your product can make it to the market. This means that the designer (or someone on the product design team) must stay informed about regulatory standards, perform pre-compliance testing, or, alternatively, involve regulatory experts and consultants early in the design process to ensure all aspects of the relevant laws and regulations are followed.
In summary, it is crucial to approach nonstandard PCB designs systematically, with a careful mindset, and considering all relevant electromechanical and thermal concerns as well as those that are regulatory, to ensure a successful product build. Close collaboration between PCB designers and experienced manufacturers is frequently the key to circumventing problems.
Resources
For more on the subject, read “Flexible Thinking: DFM or Design With Manufacturing?”
Joe Fjelstad is founder and CEO of Verdant Electronics and an international authority and innovator in the field of electronic interconnection and packaging technologies with more than 185 patents issued or pending.
Download your free copy of Fjelstad’s book Flexible Circuit Technology, 4th Edition, and watch his in-depth workshop series “Flexible Circuit Technology.”
This column originally appeared in the January 2024 issue of Design007 Magazine.
More Columns from Flexible Thinking
Flexible Thinking: The Key to a Successful Flex Circuit Design TransferFlexible Thinking: Flexible Circuit Technology—Looking Back and Forward
Flexible Thinking: Mind-tapping into January
Flexible Thinking: Another PCB Design Paradigm Shift in the Works
Flexible Thinking: Rules of Thumb—A Word to the Wise
Flexible Thinking: Musings on High Density Interconnections
Flexible Thinking: Integrated Passive Devices—Design Solutions With Many Benefits
Flexible Thinking: Mechatronics in a Flex World