Estimated reading time: 4 minutes
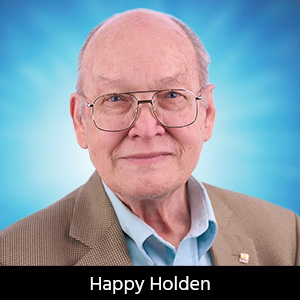
Contact Columnist Form
Happy’s Tech Talk #25: Lab-on-PCBs for Medical Diagnosis
COVID-19 created a rush for simple and quick medical diagnostic tests for the public. Lab-on-PCBs (Figure 1), started in 2000 by Agilent, have evolved to other materials and applications1.
Lab-on-chip (LoC) and lab-on-PCB (LoPCB) are devices that integrate one or several laboratory functions on a single integrated circuit or board. LoC devices are microelectromechanical systems (MEMS) devices (Figure 1) that function as micro total analysis systems (micro-TAS), generally using microfluidics principles to manipulate minute amounts of fluids. In practical terms, microfluidics is about doing chemistry on a tiny scale and trying to emulate nature. Biomedical MEMS (bioMEMS) have emerged as a subset of MEMS devices for applications in biomedical research and medical microdevices, with an emphasis on mechanical parts and microfabrication technologies. Applications include disease detection, chemical monitoring, and drug delivery. There has been rapid market growth for bioMEMS technologies, and many bioMEMS devices are already commercially available; a familiar example is the blood-glucose sensor. There is great potential for large-scale commercialization of microfluidic-based LoC and LoPCB technologies.
Elements of the Lab-on-PCB
The component devices that make up a typical LoC and LoPCB are:
- Electrophoresis fluid movement
- Microfluidics: Channels, valves, pumps, and mixers
- Separation columns
- Heating: Cooling and mixing
- Reaction chambers
- Reagent additions
- Chem-bio detectors and sensors
- UV-VIS/colorimeter sensors
- Microfluidic chips
These units combine into a functioning laboratory (Figure 2) schematic from Agilent.
Materials
Over the years, several materials have been developed for use with LoC and LoPCB. It started in the late 1990s with silicon, as the microelectronics industry developed various methods of MEMS for accelerometers for air bag sensors. From silicon wafers, the materials branched out to glass and then polymers. The most recent interest has been in PCBs and the use of various paper materials.
Silicon and glass have several advantages for fabricating LoC, but they are the most expensive. Polymers and especially PCBs are newer choices because of various available materials and the integration of electronics and types of printing technologies. While some research now focuses on paper, its use is only just beginning. Table 1 lists several characteristics of each of these materials.
Operating Sequences
It is quite remarkable what can be accomplished on a miniaturized scale. Once the technology of MEMS was perfected on silicon wafers using the photolithography, etching, metallization, and lamination processes, it became possible to miniaturize chemical analysis. But it was discovered that certain activities could be achieved in the micro and fluidic arena that did not have an equivalent in the larger real-world, such as electrophoresis (fluid movement by surface tension and applied voltages).
Once a sample has been deposited on the inlet port to a LoC or LoPCB, electro-osmotic fluid movement takes over and various actions are accomplished; the sample can be heated, passed over a stationary bed of reagents, and additional fluids can be added by the external device and mixed. The sample can be reacted in reaction chambers, and then passed to various sensors for analysis.
One of the unique variations is in the Agilent DNA and RNA Analyzer that, after the LoC cell (Figure 3e) has prepared the sample, it is fed into a nano-inkjet cartridge that deposits thousands of nano-drops on a prepared optical slide with thousands of micro-spots to react to the prepared sample. After incubation, a laser scanner records the results and prints out a final report (Figure 3f).
Figure 3 shows several of these sequences and sensors that today offer medical diagnosis in a few minutes. This used to take clinical laboratories weeks to perform, and new techniques like DNA and RNA analysis were not even dreamt about a few years ago.
Examples
In Figure 4, University of Bath researchers started with LoC experiments then progressed to using PCBs. Now LoPCB components are available, like DNA sensors and heater-on-a-PCB (Figures 4a–c). The process is fabricating fluidic channels and sensors/activators and bonding biosensor chip before final sealing (Figure 4d). The performance and illustration of lactose and glucose PCB plated sensors is shown in Figure 4e. Figure 4f shows a polyimide (PI) flexible PCB with copper- (Cu) and gold- (Au) plated sensors, coated with a gel of EDOT on a graphene carrier of AuNPs and GOx (WE).
Figure 5 shows the microfluidic elements of which fluidics/osmatic fluid movement is paramount. The use of photosensitive dry film solder mask is used for forming fluidic networks, as seen in Figure 5a. Figure 5b shows CAD design and actual transparent 3D-printed serpentine mixer. In Figure 5c is a 3D-printed microdevice of a chip featuring a mixing stage and a reaction chamber where a photomultiplier can be integrated for bioluminescence detection. In Figure 5d are 3D-printed multilayer microchannels as small as 32 mm, utilizing a flexible silicone resin and then 3D-printed directly on an unmodified Arduino PCB, demonstrating a fully integrated microfluidic-microelectronic interface (Figure 5e).
Some PCB medical devices are so small they can be swallowed and directed through your intestines to perform 2D optical-coherence tomography (Figure 6) from a tear-down by Portelligent. The endoscopic scanner uses a 2D scanning MEMS mirror only 1 mm in diameter to provide real-time 3D images and video for the physician; the device is only 3 mm square. Future devices have propulsion and steering.
Summary
Advancements in µHDI PCBs and 3D printing for additive manufacturing have led to the new products of smart microfluidic packaging for medical diagnostics. The potential link between microfluidics and multifunctional biosensing can therefore be found in the realization of 3D microfluidic manifolds, propelling lab-on-PCB technology to enable low cost and rapid micro-Total Analysis Systems—micro-TAS (µTAS).
References
- “Advances in Medical Diagnostics Using Lab-on-Chip and Lab-on-PCB Technologies,” by Happy Holden, PCB007 Magazine, April 2020.
- “LoPCB Technology,” by Despina Moschou, AltiumLive, Munich 2019.
- “LoPCB: One step away from the accomplishment of µTAS,” Biomicrofluidics, May 2022.
This column originally appeared in the January 2024 issue of PCB007 Magazine.
More Columns from Happy’s Tech Talk
Happy’s Tech Talk #40: Factors in PTH Reliability—Hole VoidsHappy’s Tech Talk #39: PCBs Replace Motor Windings
Happy’s Tech Talk #38: Novel Metallization for UHDI
Happy’s Tech Talk #37: New Ultra HDI Materials
Happy’s Tech Talk #36: The LEGO Principle of Optical Assembly
Happy’s Tech Talk #35: Yields March to Design Rules
Happy’s Tech Talk #34: Producibility and Other Pseudo-metrics
Happy’s Tech Talk #33: Wet Process Management and Control