-
- News
- Books
Featured Books
- design007 Magazine
Latest Issues
Current IssueProper Floor Planning
Floor planning decisions can make or break performance, manufacturability, and timelines. This month’s contributors weigh in with their best practices for proper floor planning and specific strategies to get it right.
Showing Some Constraint
A strong design constraint strategy carefully balances a wide range of electrical and manufacturing trade-offs. This month, we explore the key requirements, common challenges, and best practices behind building an effective constraint strategy.
All About That Route
Most designers favor manual routing, but today's interactive autorouters may be changing designers' minds by allowing users more direct control. In this issue, our expert contributors discuss a variety of manual and autorouting strategies.
- Articles
- Columns
- Links
- Media kit
||| MENU - design007 Magazine
Traditional Materials, High-Frequency Boards?
June 18, 2024 | I-Connect007 Editorial TeamEstimated reading time: 2 minutes
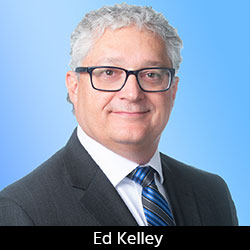
Not long ago, high-frequency and RF boards required specialized laminates, which tend to be costly and difficult to manufacture. But now, high-frequency designers use traditional PCB laminates for certain high-frequency boards. How is this possible?
For some insight, we asked Ed Kelley, founder of Four Peaks Innovation and former CTO of Isola, to discuss how traditional materials have improved and what this means to PCB designers and design engineers today.
Andy Shaughnessy: Kris Moyer at IPC is teaching designers how to avoid overconstraining their board materials. There are ways to build high-frequency boards, even RF boards, without using high-frequency materials. What are your thoughts?
Ed Kelley: If we look back in history, there was a great divide between FR-4 materials and what people used for RF/microwave applications, which really boiled down to Dk and Df properties. If you look back at the loss range, or dissipation factors, and the typical types of polymers that were used in those applications, FR-4s back then would fit into the high-loss and standard-loss categories of today’s material sets. Even back then, the products used in RF applications were in today's ultra- or extremely low-loss categories.
The two markets were separate and there wasn't a lot in the middle. But as digital applications began to require more speed and higher frequencies, those of us involved in developing materials decades ago began to introduce lower Dk, lower-loss materials, with GETEK being one of the first. Material manufacturers created competing products and these other categories—mid-loss and low-loss material segments. We began using different resin chemistries to get to the electrical performance requirements in these materials. When you get down into the very-low, ultra-low, and extremely low-loss categories, the laminate suppliers are beginning to use resins that look more like what had always been used in RF microwave materials.
There were also other differences with RF microwave materials. Historically, they used a lot of fillers that were designed to maintain Dk stability over temperature, humidity, and frequency. One of the participants in that market had patents that limited others from developing similar products. Most of those patents have now expired.
Marcy LaRont: Because of these different polymers, adhesives, and blends, we can now potentially consider “FR-4” material as another option to traditional RF material.
Kelley: Yes, historically FR-4 was virtually all epoxy resins. But you just can't get to the Dk requirements for high-speed digital applications using only epoxy. So, the first step was blending them with other resins, be it PPO, BT, SMA, etc. Eventually, you get to the lowest-loss materials used today in high-speed digital, which usually use a resin called polyphenylene ether (PPE), and blends of PPE and other resins. Over the years, conventional copper-clad laminate (CCL) suppliers, particularly when lead-free assembly came on the scene, began to use a lot of inorganic fillers to control CTE properties. So, you've had this convergence. The RF guys almost always used fillers. Then, the conventional CCL suppliers became familiar with incorporating inorganic fillers into these other resin systems. Even the manufacturing processes look similar, with the exception of PTFE-type RF materials.
To read this entire conversation, which appeared in the May 2024 issue of Design007 Magazine, click here.
Testimonial
"Our marketing partnership with I-Connect007 is already delivering. Just a day after our press release went live, we received a direct inquiry about our updated products!"
Rachael Temple - AlltematedSuggested Items
Polar Instruments Announces Additive Transmission Line Support for Si9000e
08/20/2025 | Polar InstrumentsTransmission lines embedded into the PCB surface are a feature of UHDI constructions. The 2025 fall release of Polar's Si9000e PCB impedance & insertion loss transmission line field solver incorporates eight new single ended, differential and coplanar transmission line structures.
Imec Unveils Record-Low Loss 300mm RF Silicon Interposer for Sub-THz Systems
05/27/2025 | ImecAt the IEEE ECTC 2025 conference, imec – a world-leading research and innovation hub in nanoelectronics and digital technologies – highlights the exceptional performance and flexibility of its 300mm RF silicon interposer platform.
indie Semiconductor Reports Q1 2025 Results
05/13/2025 | BUSINESS WIREindie Semiconductor, Inc., an automotive solutions innovator, today announced first quarter results for the period ended March 31, 2025. Q1 revenue was up 3.3 percent year-over-year to $54.1 million with Non-GAAP gross margin of 49.5 percent. On a GAAP basis, first quarter 2025 operating loss was $38.9 million compared to $49.6 million a year ago.
Keytronic Announces Results for Q3 of Fiscal Year 2025
05/12/2025 | KeytronicKey Tronic Corporation, a provider of electronic manufacturing services (EMS), announced its results for the quarter ended March 29, 2025.
Spirit AeroSystems Reports First Quarter 2025 Results
05/02/2025 | Spirit AeroSystems, Inc.Spirit's revenue in the first quarter of 2025 decreased from the same period of 2024, primarily due to lower production activity on most Boeing programs, particularly the Boeing 737 program.