-
- News
- Books
Featured Books
- pcb007 Magazine
Latest Issues
Current IssueThe Hole Truth: Via Integrity in an HDI World
From the drilled hole to registration across multiple sequential lamination cycles, to the quality of your copper plating, via reliability in an HDI world is becoming an ever-greater challenge. This month we look at “The Hole Truth,” from creating the “perfect” via to how you can assure via quality and reliability, the first time, every time.
In Pursuit of Perfection: Defect Reduction
For bare PCB board fabrication, defect reduction is a critical aspect of a company's bottom line profitability. In this issue, we examine how imaging, etching, and plating processes can provide information and insight into reducing defects and increasing yields.
Voices of the Industry
We take the pulse of the PCB industry by sharing insights from leading fabricators and suppliers in this month's issue. We've gathered their thoughts on the new U.S. administration, spending, the war in Ukraine, and their most pressing needs. It’s an eye-opening and enlightening look behind the curtain.
- Articles
- Columns
- Links
- Media kit
||| MENU - pcb007 Magazine
Estimated reading time: 3 minutes
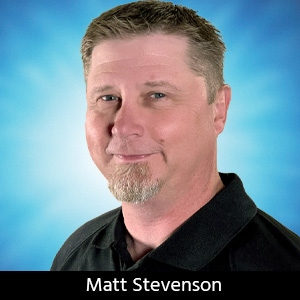
Connect the Dots: Designing for Reality—Lamination and Materials
As many of you have likely figured out, I am quite passionate about the subject of designing PCBs for the reality of manufacturing. I wrote a book about it and I participate in an I-Connect007 On the Line with… podcast series dedicated to the subject.
This companion article will focus on multilayer lamination, keeping the bigger picture in mind: Realistic PCB designs should prioritize manufacturability and reliability of the PCB as well as meet the other design requirements. So, one must account for the production variables associated with individual manufacturing partners.
Why the Lamination Process Is So Important
When designing for manufacturability, understanding the lamination process can prevent many headaches and costly delays. Lamination is a required step in the manufacture of multilayer boards, and preparing for this step requires a basic understanding of the materials and processes used.
So far, this column has covered everything from CAD tools to CAM preparation, as well as materials and imaging. This time, I’ll dive into the specifics and discuss the stacking and lamination process for multilayer PCBs.
Registration and Stacking
The goal of the registration process in PCB manufacturing is to accurately align the drill holes to the copper pads across multiple layers of the board. The correct alignment of these layers is critical because the through-holes must align perfectly to connect the intended paths without creating an unreliable connection or short-circuiting adjacent paths. With most PCB manufacturing processes, registration is done using a heavy-duty steel caul-plate with pins that keep the various layers in place.
Each copper layer of the multilayer PCB is then stacked, bottom to top, on the caul-plate. Between each layer is an insulator that either the core that the copper was processed with (usually processed in pairs like layers 2 and 3) or layers of "prepreg," consisting of a composite of pre-impregnated glass fibers and a partially cured epoxy. The prepreg, which is solid during the layup process, partially liquefies in the press when heat is added. This epoxy layer presents most of the challenges with designing for manufacturability.
Material Considerations and Challenges
The interaction of materials like copper and epoxy is a critical step in the lamination process. Copper is generally smooth, which is ideal for electrical conductivity, but not ideal for getting epoxy to stick. To ensure a robust mechanical and chemical bond, a chemical process is necessary to roughen the copper to help the epoxy adhere better.
One challenge that PCB design software doesn't help with is pressure differentials. If more than 50–60% of the layers have corresponding copper pads, for instance, the alternating stack of copper and prepreg can create a high-pressure area on the PCB. This often causes the prepreg's epoxy to be forced away from this area. Likewise, removal of copper from layers creates low-pressure areas that also tend to attract the flowing epoxy.
This kind of epoxy build-up and uneven distribution can cause a defect called delamination, where the laminate ends up leaving gaps between layers. This can lead to catastrophic failures in the PCB, such as shorts or even fires. One strategy to mitigate this is to avoid creating high pressure areas, i.e., stacking copper pads directly above one another through all layers.
Design, Collaboration, and CAD Tools
Collaboration between design engineers and manufacturers is essential to designing PCBs for manufacturing. Early discussions about stackup and material properties can prevent costly reworks. While modern CAD tools allow and even facilitate intricate designs, they do not necessarily simplify the manufacturing process. Understanding the practical implications of design choices is therefore important.
PCB design for manufacturing is a delicate balance of technological insight, material science, and precision engineering. By understanding and implementing advanced registration techniques, managing material properties effectively, and early collaboration between designers and manufacturers, PCBs can be designed to be manufactured properly the first time around.
For a deeper dive into the lamination process, listen to Episode 4: Lamination of the On the Line with... podcast, where we also discuss in more detail the challenges of heat application and the complexities of sequential lamination for high-density PCB designs.
Download The Printed Circuit Designer’s Guide to… Designing for Reality by Matt Stevenson. You can view other titles in the I-007eBooks library.
This column originally appeared in the June 2024 issue of Design007 Magazine.
More Columns from Connect the Dots
Connect the Dots: Proactive Controlled ImpedanceConnect the Dots: Involving Manufacturers Earlier Prevents Downstream Issues
Connect the Dots: Stop Killing Your Yield—The Hidden Cost of Design Oversights
Connect the Dots: Designing for Reality—Routing, Final Fab, and QC
Connect the Dots: Designing for Reality—Surface Finish
Connect the Dots: Designing for Reality—Solder Mask and Legend
Connect the Dots: Designing for Reality: Strip-Etch-Strip
Connect the Dots: Designing for Reality—Pattern Plating