-
- News
- Books
Featured Books
- design007 Magazine
Latest Issues
Current IssueShowing Some Constraint
A strong design constraint strategy carefully balances a wide range of electrical and manufacturing trade-offs. This month, we explore the key requirements, common challenges, and best practices behind building an effective constraint strategy.
All About That Route
Most designers favor manual routing, but today's interactive autorouters may be changing designers' minds by allowing users more direct control. In this issue, our expert contributors discuss a variety of manual and autorouting strategies.
Creating the Ideal Data Package
Why is it so difficult to create the ideal data package? Many of these simple errors can be alleviated by paying attention to detail—and knowing what issues to look out for. So, this month, our experts weigh in on the best practices for creating the ideal design data package for your design.
- Articles
- Columns
- Links
- Media kit
||| MENU - design007 Magazine
Bridging the Gap: Re-engaging Design and Manufacturing with Downstream
June 27, 2024 | Andy Shaughnessy, Design007 MagazineEstimated reading time: 10 minutes
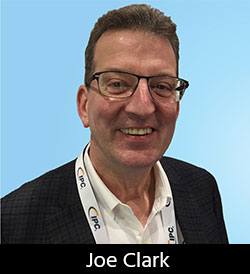
At PCB East in Boxborough, Massachusetts, I caught up with Joe Clark, co-founder of DownStream Technologies. In this interview, Joe walks us through how we got into our current situation, with design, fab, and assembly functioning in separate silos, and how DownStream and the IPC-2581 data format can help bridge this gap. He also discusses what we lost by moving from the captive model, and what we stand to gain by knocking down the walls between design and manufacturing.
Andy Shaughnessy: How are things going at DownStream?
Joe Clark: Our core philosophy and where we see ourselves playing in the process remain the same. This goes back to our beginnings, when we spun out of Innoveda with CAM350 when that product line was being “end of lifed” because at that time it was not seen that verifying designs for manufacturing was a “must do” step, but rather a “nice to do.” This was okay when we had design and manufacturing under one roof, but that all changed beginning in the ’80s when electronic product manufacturing was outsourced. When there was design and manufacturing under one roof, one had essentially a collaborative new product introduction (NPI) process: information flowed in both directions between product design and product manufacturing. The unique challenges of each phase were understood by all. Discrepancies or problems could be resolved by basically walking down the hall. There was a “shared knowledge” throughout the company.
Beginning in the mid- to late-1980s, electronic product companies began outsourcing manufacturing to gain economies of scale. This was driven by a desire to gain economies of scale as well as a strategy of focusing on core competencies: We do what we do best (design) and you do what you do best—manufacturing. There is nothing new about outsourcing. There are examples of this as far back as the Middle Ages. In the 1950s and 1960s, outsourcing really gained traction in the U.S. The electronics industry was a late entrant to the game.
Because electronic product manufacturing was now external to the OEM, this inadvertently created process “silos.” We broke the link between design and manufacturing. While there was a huge gain in economies of scale, there was a downside, which was a “dumbing down” of our knowledge and understanding of manufacturing. That “shared knowledge” was lost. At DownStream, this trend was clear to us. It was equally clear to us that design for manufacturing (DFM) analysis needed to be done upstream at the OEM, not at the very end of the process, and it needed to become a must-do part of the overall process. That was our vision, this is why we started DownStream, and we’ve stuck to that vision.
There has been much research in this area which supports our vision. For example, in their analysis on re-engaging the NPI, the Aberdeen Group points out that three of the top five issues that cause problems in the manufacturing arena involve documentation. But the reality is that most electronic product companies produce very poor documentation, primarily because the tools that have been available do such a poor job at creating PCB documentation.
The research also shows that successful electronic product companies—and by successful we mean companies that meet their time to market and cost goals—implement a design for manufacturing (DFM) strategy in their process. Our tools tie both together. In the PCB East Lunch-and-Learn I led, I highlighted DownStream and our tools, but the core of what I will present really boils down to, “Why does DownStream even exist?” I wanted the audience to think differently about the process. When I first came into the industry, it was very common for electronic product companies to fabricate and assemble their own boards. This is what we now call the captive model. This is no longer the case, and in many ways, companies are realizing they must “relearn” manufacturing and take more responsibility for this phase, i.e., improve the handshake.
Shaughnessy: You do that because you really want to solve problems early in the process before you add all that value of the processes, components, labor, and time?
Clark: Right. Companies really need to re-engage with manufacturing and, to do so, make some changes.
Shaughnessy: So, in moving to the outsourcing model to improve the process, we wound up setting up two or three independent silos and pretty much screwed it up.
Clark: Well, we didn't screw it up necessarily. We still got the job done, but the result, as I say, was that a silo mentality was created because now the design side was completely broken away from the manufacturing side. It really did become the proverbial “throwing it over the wall.” There was no longer that shared knowledge, that connection with the downstream processes, and those downstream partners were worried about filling their capacity. So, they would take in any data that they got and figure out how to make it work. There were a lot of errors and delays, adding extra cost and reducing product ROI.
Regarding the Aberdeen Group, they talk about the successful companies that they've analyzed and what they did that resulted in this success. What they discovered is that the successful electronic product companies had a common thread: They each recognized the need for re-engagement with the NPI process, which really means re-engagement between design and manufacturing. Further, these companies implemented three key things in their process. First, they each adopted the use of an intelligent design exchange format, in particular IPC-2581. Second, they each adopted a DFM strategy; third, they have focused on providing detailed documentation to ensure that these products can be manufactured and built right the first time.
Shaughnessy: Since you mentioned it, why does DownStream exist?
Clark: As we envisioned, companies need to re-engage with the NPI process and we are the company to help them do this. I would classify DownStream as the NPI analysis company. We are the company with tools that are geared toward ease of use, priced appropriately, rich in functionality, that the design community can use earlier in the process to make sure that what they send to their manufacturer, captive or external, can be built the first time. That is a constant challenge as technology advances and changes. Some good examples of this are designs with embedded components or rigid-flex designs. We are working with major companies now to develop advanced DFM for flex and rigid-flex. There's a whole new set of challenges with flex designs
I believe the center of gravity has shifted. Back in the day, we had a CAD tool binary database, and you were at the mercy of your EDA vendor’s tools, good or bad. The center of gravity has shifted now from that to this neutral IPC-2581 format, which different tools can read and write from to streamline the process. That's what we see companies adopting.
Shaughnessy: I'm glad you’re seeing more buy-in with 2581 now. It must be frustrating sometimes that 98% of boards are still done on Gerber. It's a mystery, but we like what we like.
Clark: I have a theory on that. When you have a concept for a new product, there's a starting point and an ending point. We schedule all the parts of the process between the start and end points: the specifications, electrical design, PCB layout , etc. What ends up happening, though, is that only the end point tends to be really locked down, and all the intermediate schedules tend to change. The people that get squeezed the most are on the manufacturing side. When a designer has something that works, they're very reluctant to change. That's the problem with making design very fluid. You had six weeks to do it, but it took 10. But we do not adjust and allow any more time on the back end of the process. I'm generalizing here, but the further downstream you go, the more reluctant companies are to change. “If it works, don’t break it.” That’s the classic definition of risk averse.
Shaughnessy: Why don’t contract manufacturers push back and say, “It’s in your best interest to give us the ODB++ or IPC-2581. It won’t cost you anything.”
Clark: That’s a very good question. We know that manufacturers are risk averse and are focused on capacity utilization. So, they always have a fear that the “other guy” will get the job if one refuses because of the data quality. The pushback we constantly hear is, “You take my Gerber data or the guy down the street will.” The good news is that this is changing. There are several manufacturers that are beginning to offer a discount if they are provided IPC-2581 or ODB data, and the charge is more if you hand off Gerber data.
A couple of contract manufacturers stopped by the IPC-2581 booth today. It was somewhat disappointing, and surprising to me, that a few of these manufacturers claimed to have never heard of 2581. How could anyone not have at least heard of 2581 in 2024? There's not a CAD tool today that doesn't export both 2581 and ODB++. I am a little biased, of course.
Shaughnessy: Even great ideas and processes take time to be adopted, but it is happening.
Clark: That is no doubt the case. When we were at PADS, we were also pretty visionary. We acquired HyperLynx when we were at PADS. At that time, the signal integrity tools were big, heavy, and expensive, which meant it was the purview of the big companies, the “early adopters.” The tools typically had to be customized for each company’s analysis, and the analysis was done at the “end of the line.” You do your design, send it to the “back room,” and the witch doctor back there with one of these big expensive tools would bless it or fail it. If there was a problem, then you had to go back to the beginning. I am exaggerating here to make my point about the inefficiencies in the flow.
Our vision was that signal integrity analysis had to become part of the standard mainstream process and that you don't want to wait until the end to do your signal integrity. You need a tool that you can use in line, but it has to be a “lighter” tool. By this, I mean it has to be easy to use and cost-effective so that the designer can pick it up and put it down. If they're using the CAD tool 100 times a week, they're using the signal integrity tool twice a week. Hyperlynx “crossed the chasm” for many companies. Adoption didn’t happen overnight in the case of signal integrity tools. However, use of signal integrity tools in the design process is pretty standard practice today.
Renewed focus on the NPI process is an analog to the signal integrity tool adoption. But you need enablers. You need the new platforms, algorithms, design exchange formats, etc. These are available today. But the key is you need a willingness to change, and this may be the hardest part.
Shaughnessy: Wasn’t the netlist another example where this dynamic came into play for DownStream?
Clark: Yes. When we created DownStream in 2002, we traveled the world and re-engaged with customers. One of the most eye-opening discoveries we made back then was that customers were not sending separate IPC-D-356 netlist files with their Gerbers. This has since changed, but it’s a good example of the “silo” problem we created. Companies didn't understand that if you did not send the netlist along with the Gerbers, the only choice the fabricator had was to extract the netlist from a “golden” board to create bare board testing. So, if the Gerbers were bad to begin with, the manufactured boards would still pass the bare board test, and you’d get bad boards as a result. It's that whole disconnect that occurred because of outsourcing.
Shaughnessy: There’s still a big disconnect.
Clark: That’s right. Going back to my original idea, the real point here is that by breaking that connection long ago and contracting out manufacturing, even though there were huge economic gains, there were some real negatives that have only recently been recognized by companies acknowledging that they need to re-engage and recreate that handshake between design and manufacturing. But that re-engagement is happening.
Shaughnessy: Thanks for talking with me, Joe.
Clark: Always a pleasure, Andy.
Suggested Items
I-Connect007 Editor’s Choice: Five Must-Reads for the Week
07/11/2025 | Andy Shaughnessy, Design007 MagazineThis week, we have quite a variety of news items and articles for you. News continues to stream out of Washington, D.C., with tariffs rearing their controversial head again. Because these tariffs are targeted at overseas copper manufacturers, this news has a direct effect on our industry.I-Connect007 Editor’s Choice: Five Must-Reads for the Week
Infineon Advances on 300-millimeter GaN Manufacturing Roadmap as Leading Integrated Device Manufacturer (IDM)
07/10/2025 | InfineonAs the demand for gallium nitride (GaN) semiconductors continues to grow, Infineon Technologies AG is poised to capitalize on this trend and solidify its position as a leading Integrated Device Manufacturer (IDM) in the GaN market.
The Global Electronics Association Releases IPC-8911: First-Ever Conductive Yarn Standard for E-Textile Application
07/02/2025 | Global Electronics AssociationThe Global Electronics Association announces the release of IPC-8911, Requirements for Conductive Yarns for E-Textiles Applications. This first-of-its-kind global standard establishes a clear framework for classifying, designating, and qualifying conductive yarns—helping to address longstanding challenges in supply chain communication, product testing, and material selection within the growing e-textiles industry.
SMT007 Magazine July—What’s Your Competitive Sweet Spot?
07/01/2025 | I-Connect007 Editorial TeamAre you in a niche that’s growing or shrinking? Is it time to reassess and refocus? We spotlight companies thriving by redefining or reinforcing their niche—what are their insights? In the July 2025 issue of SMT007 Magazine, we spotlight companies thriving by redefining or reinforcing their niche and offer insights to help you evaluate your own.
TRI Unveils New Multi-Camera AOI, TR7500 SIII Ultra
06/27/2025 | TRITest Research, Inc. (TRI), the leading test and inspection systems provider for the electronics manufacturing industry, proudly introduces the new TR7500 SIII Ultra.