-
- News
- Books
Featured Books
- design007 Magazine
Latest Issues
Current IssueProper Floor Planning
Floor planning decisions can make or break performance, manufacturability, and timelines. This month’s contributors weigh in with their best practices for proper floor planning and specific strategies to get it right.
Showing Some Constraint
A strong design constraint strategy carefully balances a wide range of electrical and manufacturing trade-offs. This month, we explore the key requirements, common challenges, and best practices behind building an effective constraint strategy.
All About That Route
Most designers favor manual routing, but today's interactive autorouters may be changing designers' minds by allowing users more direct control. In this issue, our expert contributors discuss a variety of manual and autorouting strategies.
- Articles
- Columns
- Links
- Media kit
||| MENU - design007 Magazine
Estimated reading time: 7 minutes
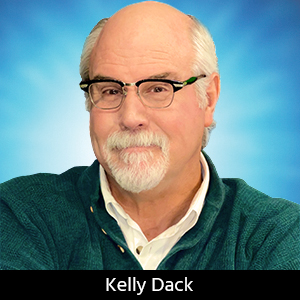
Contact Columnist Form
Target Condition: Taking the Stand at Your Own Design Review
It can be risky to take the stand in your own defense during a trial. You never know what could get brought up, and you might not be prepared. In PCB design, ignorantia juris non excusat (“ignorance excuses no one”). No one is above the laws set by the “court” of design for performance, manufacturability, and test (DFX).
Let’s lay out some of the facts of this case. First, the PCB design industry is constantly changing, as new designers don’t know what they don’t know, and old-timers think that no one knows as much as they do. How can this range of PCB designers operate under the PCB design system I’ve suggested?
While everyone makes mistakes, perfection in the PCB design and manufacturing industry is found within our industry standards, which provide the foundation for measurable producibility. These standards define what is acceptable and non-conforming regarding material, process, part, or assembly performance and have been developed by a wide cross-section of industry representation.
Yet, we’ve all had experiences when people break the rules. I’ve broken my fair share as well. We admit our mistakes, learn the rules, and move on. However, some are unwilling to learn and admit error. They just don’t care about established standards and expect the entire industry to adjust and revolve around them. In their own eyes, their designs are perfect. They don’t break the design rule checks (DRC) because they never set them. That’s a big difference.
Sins of Commission
Can you imagine a designer selfishly releasing a PCB layout and CAM data solely to meet a schedule without having incorporated all the requirements defined by a project team? This could be considered a sin of commission: unconcerned with robbing fellow project stakeholders of their capability to perform their project steps for success.
Then imagine a PCB designer making concessions to a fab supplier—perhaps due to a design error—without informing the rest of the team. After working for many decades in the PCB design and manufacturing industry, I’ve seen this happen a lot.
When a manufacturing stakeholder sends an engineering query to a PCB designer stating that features on a design are impossible to manufacture in volume without some re-design, it’s not a hoax or because the system is rigged. It is because very advanced systems of CAM auditing have compared the layout geometry and details to established capabilities calibrated to common standards (design laws) set up in established manufacturing communities.
What would you think about a PCB designer responding to a supplier with such arrogance, exclaiming that these omissions happen all the time and, thus, the claims are invalid? They might even maintain there is nothing wrong with the design. Would you want to add someone like this to your PCB design development team? Of course not.
Sins of Omission
If you’re like me, you’ve had many opportunities to learn by doing dumb things, then finding out later that you screwed up and who was affected by it. One thing that comes to mind was about 30 years when I created an edge card pattern only to get the “A” and “B” side numbering reversed. The rework is so painful that you only make this mistake once. The engineers made me cut the erroneously flipped edge card connector of the PCB and build an adapter to reverse the connections on the prototypes so they could continue testing the entire system.
My point is that we admit our failures or omissions, learn from them, and move on. It’s not always easy, though. I work for an EMS provider, and our VP of engineering likes to ask engineering candidates about one of their major design failures, what it affected, and what they learned. It’s refreshing when a job candidate is transparent about being human and humble enough to admit errors and share lessons learned. We’ve often followed up those interviews with healthy discussions about how the implementation of formal team design reviews provides an opportunity to seek out peer review and compare notes prior to blowing something up.
The Formal Design Review: Be Transparent and Forthcoming
Best practices in PCB design methodologies show us that the best way to avoid the legal pitfalls of non-conformance challenges is to perform a design review with all project stakeholders. Soliciting buy-in and concurrence prior to design release is a proven method for success as it allows all stakeholders a respectful opportunity to accept or reject the project outputs as deliverables. The practice spreads accountability across the entire project team. Most importantly, a formal design review prior to investing large sums of money for manufacturing services and tooling is insurance that all phases of development have been reviewed by appropriately qualified subject matter experts.
Not everything goes perfectly at a formal design review, so just be open. It can be an opportunity to gain more insight or ask for help before proceeding. Transparency is key. In a courtroom, prosecutors are known to make mincemeat of defendants whose stories don’t add up, who demonstrate incompetence, are full of excuses, and blame others for failures.
However, if you’ve done your best to ensure your PCB layout has met the design and manufacturing constraints, you don’t believe you’ve broken any rules, and you’ve consistently stayed in touch with your project stakeholders throughout the course of the layout, you are ensuring you won’t be put “on trial” for negligence or coverups.
So, be transparent: Show the status of your layout and how it meets the identified design constraint criteria.
The Defense Rests
The ideal PCB project stakeholder is a subject matter expert of “sound mind and character,” worthy of their title and pay. You want to be known as a communicative, collaborative team member who is always learning and evolving, sometimes inventing, and able to lead by experience but willing to follow. When called upon for a PCB design review, you can eloquently defend the design decisions made without insulting others or undermining the process. You easily articulate the detailed steps taken to ensure that the needs of every project stakeholder have been met. You present sound evidence, showing concurrence with each stakeholder along the process steps of the design. You will defer to other teammates for explanations on issues that are outside your own expertise but acknowledge ownership of the entire completed layout.
The Verdict
How was your last PCB design review? If you only reviewed the design with yourself or maybe another EE, there’s a good chance your layout may be subject to a future indictment for DFX non-conformance, negligence, or worse, by the time your project manager releases it to production. When your team of project stakeholders wants to know why so many competitive production facilities cannot build your printed circuit board and assembly—or why it continues to fail in the field—will you have the means to defend your layout?
Please take early identification of design constraints and manufacturing capability buy-in seriously. If you need to, turn over a new leaf. The only time a PCB designer should ever hear the term “lock ‘em up” is at the conclusion of the final, formal design review. “Locking” or “freezing” is part of formal design protocol, ensuring the critical features won’t inadvertently change after each stakeholder has been thoroughly convinced the PCB rules of DFX “law” have been followed.
On a good day, the final PCB design review with your peers should conclude something like this:
Program manager: “Project stakeholders, you have heard the evidence and have been informed of the project timeline, costs, risks, and design and manufacturing expectations. What is your verdict?”
Fabrication supplier: “Materials, fab, and inspection documentation easily meet DFM requirements. Lock ‘em up!”
Test engineers responsible for ICT: “We have 100% accessibility to all nets with adequately sized and spaced test points. Lock ‘em up!”
EEs responsible for performance and signal integrity: “Lines look great and simulate within spec. Lock ‘em up!”
MEs responsible for package form and fit: “Mechanical attributes meet all interface requirements; no interference. Lock ‘em up!”
Supplier management responsible for BOM sourcing: “All parts on order, no shortages. “Lock ‘em up!”
Program manager: “Congratulations PCB designer. This jury of your project peers has found your layout in total conformance on all counts pertaining to the laws of DFX. You are free to begin your next design after locking up your approved design data attributes and outputting and releasing fresh CAM data.”
Let us all perform our PCB engineering duties with character, integrity, and respect and make every effort to consider the needs of our valuable project stakeholders in parallel with our own.
This column originally appeared in the July 2024 issue of Design007 Magazine.
More Columns from Target Condition
Target Condition: Floor Planning Without a FloorTarget Condition: The 5 Ws of PCB Design Constraints
Target Condition: Are Autorouters Friend or Foe?
Target Condition: From Dream House to Drill Files
Target Condition: Designing vs. Inventing
Target Condition: ‘Boomer to Zoomer: Do You Copy?’
Target Condition: Advanced Packaging Technologies—Look Before You Leap
Target Condition: My Anti-venom to PCB Cost Adders