-
- News
- Books
Featured Books
- pcb007 Magazine
Latest Issues
Current IssueSales: From Pitch to PO
From the first cold call to finally receiving that first purchase order, the July PCB007 Magazine breaks down some critical parts of the sales stack. To up your sales game, read on!
The Hole Truth: Via Integrity in an HDI World
From the drilled hole to registration across multiple sequential lamination cycles, to the quality of your copper plating, via reliability in an HDI world is becoming an ever-greater challenge. This month we look at “The Hole Truth,” from creating the “perfect” via to how you can assure via quality and reliability, the first time, every time.
In Pursuit of Perfection: Defect Reduction
For bare PCB board fabrication, defect reduction is a critical aspect of a company's bottom line profitability. In this issue, we examine how imaging, etching, and plating processes can provide information and insight into reducing defects and increasing yields.
- Articles
- Columns
- Links
- Media kit
||| MENU - pcb007 Magazine
Estimated reading time: 5 minutes
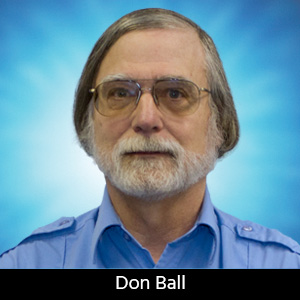
The Chemical Connection: Chemical and Equipment Control of High-density Circuits, Part 2
In my June column, I discussed how much control was needed for high-density circuits rather than what was thought necessary. I concentrated on cupric chloride and alkaline etch issues and equipment, since the etching step in the circuit board manufacturing process is one of the most critical areas where small changes in etchant parameters can have a large effect on the final product. The intention was to continue in the July issue with less critical process steps, such as developing and stripping. However, I got distracted by a specific control issue for alkaline etch, specifically controlling your alkaline etch process when you’re not etching a lot of copper. So, this month, I’m picking up where I left off in June.
I had mentioned that an oxidation/reduction potential (ORP) monitor could be useful with alkaline etchant, but I ran out of column space. The ORP of an alkaline etch solution is the ratio of Cu+2 ions to Cu+1 ions, just as it is with cupric chloride etchant. However, the ratio of +2 ions to +1 ions is close to 1:1 in an alkaline etch bath, so the working ORP in a healthy bath is closer to 0 mv instead of the upper 500 mv for a cupric bath. You can expect a new alkaline bath to have an ORP of about 130 mv, dropping quickly to between -10 mv and +10 mv as the copper etching process begins. How can knowing the ORP of your alkaline etch bath be useful? If the ORP drops below the -10 mv range and continues to drop, it’s a warning sign that there may be these potential problems:
It may be that the ventilation system is not drawing enough air into the etch chamber for the regeneration reaction. This usually happens when etching a high volume of copper in a short period of time.
If the ORP comes back up after stopping the etching, this is an indication of the problem. The etch rate slows down as the ORP drops, so this warning might prevent under-etched product. ORP readings have indicated the need to open air spargers at the bottom of the etch sump to provide extra air for high-volume etching systems.
Low ORP values in an alkaline etch bath can also indicate that the chloride levels in the bath are low, and there’s not enough ammonium chloride to react with the oxygen in the air to re-oxidize the Cu+1 ions. Here, it might be a good idea to check the chloride levels in the etchant. ORP monitors are relatively inexpensive, and ORP probes are very reliable, so it might be worth considering this as an add-on.
Developing your panel after exposure is one of the most forgiving steps in the whole circuit board production process. For instance, the manufacturer of the dry film etch resist I use recommends setting the conveyor speed for the developing process so the clean resist breakpoint (the percentage of distance through the developing chamber where the unexposed resist is visually gone), is between 50–60%. For my developer, if I set the conveyor speed to a 55% breakpoint, I can have a ±5 inch per minute speed variation without affecting my developing quality. Etch testing has shown that panels developed at 40, 50, 60, and 70% breakpoints have no difference in etch uniformity or etch rate, so there is even more room for variance than the manufacturer suggests.
The same is true for developing temperature. The manufacturer recommends a process temperature between 80–90°F (27–32°C). Again, etch testing has revealed no difference in etch uniformity or etch rate for test panels developed at different temperatures within this range. This allows a ±5°F (±2.5°C) variation from an 85°F setpoint without affecting the development quality.
There are similar wide process windows for solution strength and spray pressures, so expensive upgrades to the developer equipment manufacturer’s standard temperature, pressure, and speed controls aren’t necessary. Some opt for a pH monitor or controller to more efficiently determine when to put a new bath in or to extend the bath life to reduce the time lost changing the bath. A newly mixed bath will have a pH range of 11.3 to 11.4. The pH will drop rapidly to around 10.8 when the developing process begins, then drop more slowly until the pH reaches about 10.5. At this point, it is a good idea to change the bath. Using the pH to control a dosing unit to add water and fresh developer solution will extend the life of the bath and allow longer times between bath changes. A pH setpoint of 10.7 for adding fresh developer will keep the pH between 10.6 and 10.8. This is good enough to maintain a steady conveyor speed and development rate.
Some things need to be checked even with a pH controller. Most people are unaware that the developer solution can buffer after a while, which means it will read the same pH no matter what state the bath is in. The only sign of this will be undeveloped resist on the panel, even though the pH appears to be in the correct operating range. To prevent this, one should check the pH often with an independent meter and the probe recalibrated if the divergence is too high (although a person with one pH meter always knows what the pH is; a person with two pH meters is never sure). Running a breakpoint panel daily before use is also necessary, regardless of the pH meter reading.
Like the developing process, the stripping process has generous working windows for most process parameters. Most dry film suppliers recommend a 50% breakpoint for clean resist removal, but ±10% makes little difference. Minor deviations in conveyor speed, spray pressure, or bath temperature have little effect within the 40-60% breakpoint range, so the standard controls with most stripping equipment are adequate for the process.
One can use pH control to extend the time between stripping bath changes, but this has caused maintenance problems in the past; pH is now used mainly to monitor the bath. Most opt for a simple panel counter to add fresh stripper to the bath every few panels. As with the developer, make sure to check the pH probes daily with an independent meter, and run breakpoint panels every day before use.
The takeaway is that you don’t need to spend much time worrying about super-tight controls for developing and stripping equipment. The working windows for the process parameters are wide enough that the standard controls with the equipment will provide all the necessary control.
This column originally appeared in the August 2024 issue of PCB007 Magazine.
More Columns from The Chemical Connection
The Chemical Connection: Through-glass Vias in Glass SubstratesThe Chemical Connection: Reducing Defects in Circuit Board Production
The Chemical Connection: Common Misconceptions in Wet Processing
The Chemical Connection: Surface Finishes for PCBs
The Chemical Connection: Earthquakes, Astronauts, and Aquatics—A Lighter Look at the Past
The Chemical Connection: Better Fabs Attract a Better Workforce
The Chemical Connection: Can Changing Spray Nozzles Improve My Etch Quality?
The Chemical Connection: Getting the Best from Your Cupric Chloride Etchant