-
-
News
News Highlights
- Books
Featured Books
- design007 Magazine
Latest Issues
Current IssueAll About That Route
Most designers favor manual routing, but today's interactive autorouters may be changing designers' minds by allowing users more direct control. In this issue, our expert contributors discuss a variety of manual and autorouting strategies.
Creating the Ideal Data Package
Why is it so difficult to create the ideal data package? Many of these simple errors can be alleviated by paying attention to detail—and knowing what issues to look out for. So, this month, our experts weigh in on the best practices for creating the ideal design data package for your design.
Designing Through the Noise
Our experts discuss the constantly evolving world of RF design, including the many tradeoffs, material considerations, and design tips and techniques that designers and design engineers need to know to succeed in this high-frequency realm.
- Articles
- Columns
- Links
- Media kit
||| MENU - design007 Magazine
Estimated reading time: 7 minutes
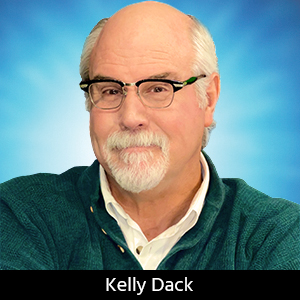
Contact Columnist Form
Target Condition: My Anti-venom to PCB Cost Adders
As a kid, I remember long, hot, cross-country trips to the Midwest with my grandparents to visit relatives. Riding in the backseat of a 1970s station wagon without air conditioning, the only thing I had to look forward to was stopping at Stuckey’s in Oklahoma, which had a snake farm right next door. As luck would have it, after a hundred miles of passing signs advertising “Ramona’s Snake Farm,” Grandpa pulled in and made my trip come alive. I’d never seen a poisonous snake up close, and there were hundreds of them.
Snake pits, snake handlers, and venom-milking demonstrations garnered lots of oohs, ahs, and applause from the motor-tourists, including me. The handlers explained the snakes' habitats and unique characteristics and, most importantly, how to avoid getting bit. I left the snake farm with a greater understanding of snakes, and I’m proud to say I’ve never been bit.
One fairly benign species is Vipera berus, known as the common European adder, a venomous snake that isn’t particularly aggressive, nor is its bite fatal. However, PCB designers risk getting bit by “adders” of another kind: Serpens addit nimium pretium, or simply, cost adders. Often coiled up in product development teams' brainstorming sessions or lurking inside the unexplored settings of our PCB design tools, these dangerous critters are of the profit-killing species.
In my walkabouts through the PCB design and manufacturing jungles, I’ve met many PCB designers who have suffered painful bites from these cost adders. These critters are particularly dangerous when a PCB designer steps naively into unfamiliar areas and does not know where to look. I have been bitten many times by the cost adder, but I’ve learned from my mistakes.
Now, I’m offering a few free doses of cost adder anti-venom.
Species: Serpens Materia (Material Cost Adders)
While most think of PCB material as simple glass-epoxy sheet stock or FR-4, PCB laminates have expanded into very advanced, brand-name, trademarked product lines that target specific performance and operational requirements for advanced PCBs.
When a PCB design layout goes to production, be wary of Serpens materia. Fabrication drawing notes must contain a material specification through which the PCB is made. Global PCB fabrication suppliers prefer simple glass/resin or polyimide laminates that can be readily procured from multiple sources. But often, PCB designers make the mistake of specifying brand-name materials or part numbers when it is not required. Other designers even declare “no substitutions.” Designers who proceed in this manner without advanced understanding and justification are reaching dangerously into the den of Serpens materia. When their design moves to volume quantities, they will most certainly experience a painful strike from this adder with swelling of cost and necrotic product profit margin to follow.
The anti-venom for Serpens materia is modest but powerful. It must be injected directly into the design fabrication note-specifying material. After dosing, a basic material note’s brand name, cost swollen specification can heal by stating: “Materials: Laminated, glass base, epoxy resin type FR-4 series or equivalent per IPC-4101 with Tg >/= 130°C and a Td >/= 300°C electro-deposited copper foil. Nominal base (starting) copper thickness for all layers shown on stackup detail.”
Species: Serpens Processus (Process Cost Adders)
There are many ways to process a single feature on a PCB. For example, a board edge can be routed out, punched out, V-scored, laser cut, or even cut with an abrasive water jet. The way the designer lays out the shape of the board geometry will allow or eliminate many of the available processes. If a board outline maintains a rectangular shape, it can tolerate almost any process and allows the supplier to use V-scoring, which can be very cost-effective.
But rounding the corners to eliminate a sharp edge means an additional process step of routing to form the rounded edge. With rounded corners and straight edges, a PCB can be processed with a combination of V-scoring and routing at a cost for the additional process. Rounded features on a PCB outline are notorious hiding places for Serpens processus because of the additional process of routing and associated machine time or shifting the processing to a tab-route solution requiring mouse bites.
Mouse bites can cause localized stress on the PCB edge and lead to component cracking. Serpens processus is a wily species, often cohabiting with other, beneficial process species. To avoid being bitten, designers must focus on design constraints, keep them simple, and be aware of design features that add processing. Common lairs for process cost adders are PCB outlines, hole definitions, unique sizing, finishing, or coatings, especially ones requiring extended cure times.
The anti-venom is applied topically and serves mostly as a repellent; PCB designers must apply heavily during times of early project planning and treat fellow stakeholders who might be unaware of the dangers. Signs of an early bite, however, will materialize via stakeholder team suggestions describing oversized, curvy-shaped PCB designs with both plated and unplated countersunk mounting holes. In rare cases, wild visions of PCB stackups capable of carrying 80 amps and running down an ordinary soldering line must be treated immediately. In these cases, the venom of the process cost-adder has reached the brain tissue of this stakeholder and must be stopped before reaching the project budget and swelling it until it pops.
Species: Serpens Apparatus (Machinery and Equipment Cost Adders)
The safest way to avoid the bite of Serpens apparatus is to stay on the high ground, making quick hops between the machine stations that do the work of manufacturing the PCB. If a designer can clearly see and understand what it takes to hop to the next machine station without falling to the adder-infested jungle floor, the chances of being bitten by Serpens apparatus decrease greatly. But many PCB designers fail to study the equipment and capabilities of the fab and EMS providers, relying only on the PCB design software as a GPS guide.
We see news stories about travelers not researching their destination and winding up in dangerous situations by relying solely on GPS. Unfortunately, designers often suffer the same metaphorical fate. PCB design software can convert almost any geometric feature into a process machine language. Via padstacks are not only identified as drilled and plated holes, but our layout tools now invite designers to select from several filling and capping options without identifying the added cost or equipment needed.
Just last week, I had to rescue a designer who had fallen to the jungle floor in this manner. He’d pressed some via definition buttons and unknowingly stirred up a nest of Serpens apparatus. In the nick of time, I yelled, “Cost adder, watch out!” Once we scrambled back up on the DFM observation platform for a design review, we could clearly scope out the equipment that would have been required for the unnecessary filled and capped vias. We were lucky enough to avoid being bitten by Serpens apparatus and lived to tell the story.
The anti-venom for Serpens apparatus does not yet exist. The best prevention for this type of bite involves traveling to PCB design and manufacturing trade shows and taking frequent tours of PCB and EMS manufacturing facilities. There is simply no better way to get in touch with the equipment and the people who run it. To remain above the manufacturing jungle canopy and to know where to jump next, PCB designers must become familiar with the following equipment and their respective capabilities and design requirements:
- Drilling machines
- Photoimaging equipment
- Plating and etching tanks
- Wet coating machines
- Laser direct imaging machines
- Printing machines
- Flying probe test equipment
- Solder printing machines
- Pick-and-place equipment
- Conveyers and pallets
- Reflow ovens, wave and selective soldering equipment
- Optical inspection equipment
- Routing, nibbling, and v-scoring equipment
- Functional and in-circuit test equipment
- Know Your Cost Adder Species
As PCB designers, we cannot wander blindly and naively within our PCB design layout tools—clicking buttons and assigning values—without the ability to count the cost of such actions. Whenever we guess what is needed to form a PCB feature without understanding, we are, in effect, sticking our appendages into the cost adder’s den. If you’re like me, you are a PCB designer who learns in person. You need to get a tactile understanding of the subject matter at hand. To educate yourself with the excitement of a kid in a snake farm, you need to make every effort to tour a PCB manufacturing facility and/or attend a trade show displaying lots of materials, processes, and equipment. There, you can safely wander the aisles and view many PCB manufacturing cost equivalents to rattlesnakes, water moccasins, vipers, and all the various types of adders safely behind the glass or yellow lines painted on the concrete floors.
Before it’s too late, slowly and cautiously step away from your PCB design laptops. Do not make any sudden moves. Turn and run to the closest PCB manufacturer or trade show to learn more about what it takes to keep PCB project costs low.
This column originally appeared in the August 2024 issue of Design007 Magazine.
More Columns from Target Condition
Target Condition: From Dream House to Drill FilesTarget Condition: Designing vs. Inventing
Target Condition: ‘Boomer to Zoomer: Do You Copy?’
Target Condition: Advanced Packaging Technologies—Look Before You Leap
Target Condition: Taking the Stand at Your Own Design Review
Target Condition: Designing Unconventional Geometries
Target Condition: What the Heck? A PCB Tech Spec Check
Target Condition: Keeping Your Design on the Road