Estimated reading time: 3 minutes
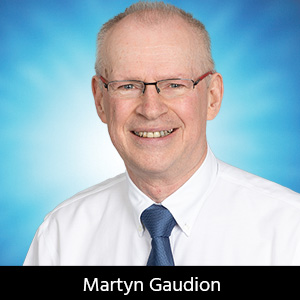
The Pulse: Commonsense Cost Cutting
One difference between engineering and pure science is that engineers (in most situations) are looking for cost-effectiveness. They do so by designing the most appropriate level of technology to maximize profitability with acceptable levels of application functionality.
One area that is often overlooked is the energy cost of PCB production. At a recent EIPC conference, Dr. Maarten Cauwe of IMEC in Belgium presented a combined study of the lifecycle impact (LCI) of electronics systems and subassemblies1. The study looked at the supply chain as well as the energy impact of HDIs, the power consumption of repeated plating cycles, and the energy impacts of different metal finishings.
One side point was the move to lead-free soldering, which has raised energy consumption across the board. I wonder if legislators will hear this message and, at some point, cause a U-turn in the industry where the lead-free project, once deemed worthy, no longer seems like a good idea. Half a century ago, CFCs were miracle chemicals. Now, not so much. Changing times and emphasis, with effects that take decades to emerge, mean that ideas that once seemed sensible can, with the benefit of hindsight, seem not so good. The study is interesting because it attempts to put together a whole-of-life model for the electronics ecosystem rather than looking at individual items in isolation.
Detail Matters
While IMEC studies are effective from a top-down standpoint of the whole energy cost of electronics and subsystems, at the day-to-day level, it is down to individuals and teams to make a difference. Additionally, the cost of PCB design is not solely down to energy, though that plays a part at every point. The fact that the type of build alone can impact the cost should be considered, as well as the material choices.
When considering materials for high-speed boards, especially those intended for volume use, it is wise to assess whether each layer needs high-speed materials. The savings can be considerable if basic materials can be used in layers where speeds are low or moderate. Clearly, a different approach is required for low volume. However, if the volume is low because of a prototype application, it’s worth exploring the same material choice used in volume to pre-empt any surprises should you prototype in an exotic material and back off the specs on less critical layers in final production quantities.
Short, Slim, and Smooth
Per my recent column on high-speed designs, you can reduce the need for exotic materials if you have the luxury of keeping the high-speed lines as short as possible. Losses are directly proportional to line length. If a compact design is viable, you can save on both the cost of materials and the consumption of square meters.
Panelise With Waste Minimization in Mind
Designing with panel size in mind can save on material costs. The late Martin Cotton was a firm believer in optimising the total design to maximise the use of standard panel size. While panelisation software helps with optimisation, the designer can make life easier for the fabricator by considering the panel size when designing the entire system. It is also worth noting that PCB fabricators have made large strides in optimising panel use and being able to fabricate closer to panel edges.
Simulate Where You Can
Simulation reduces the number of prototype turns and simulates how a design may respond to normal component variation in production. Monte Carlo simulations for electronics design allow you to see how much variation to expect over typical production runs. Monte Carlo tools add a dose of realism to the engineering process, as it’s easy to be seduced by the multi-digit precision of modeling tools and circuit simulators. Tools with the ability to run simulations with expected parametric variations add confidence to the design process and give the designer more confidence in the finished yield, reducing the need to run extensive and expensive physical prototype turns.
Conclusion
Always keep an open mind and look for cost savings from different angles. My opening note on energy costs is interesting for fabricators because, with energy costs being high, saving energy for the same functionality by choosing an alternate stackup is a win all around. There are many ways to save costs, so it pays to keep your eyes open for innovative solutions.
References
1. “A parametric approach to quantifying the environmental impact of PCB manufacturing,” by Cauwe, Willems, and Geerinckx (IMEC/IMEC/ACB), CMST IMEC Research Group, Ghent University BE.
This column originally appeared in the August 2024 issue of Design007 Magazine.
More Columns from The Pulse
The Pulse: Design Constraints for the Next GenerationThe Pulse: Ultra Upgrade Unknowns—What’s Coming for UHDI?
The Pulse: Overconstraining: Short, Slim, and Smooth
The Pulse: Drilling Down on Documentation
The Pulse: New Designer’s (Partial) Guide to Fabrication
The Pulse: Simplest Stackups Specified
The Pulse: Rough Roughness Reasoning
The Pulse: Industry Organizations Keep Knowledge Alive