-
- News
- Books
Featured Books
- design007 Magazine
Latest Issues
Current IssueShowing Some Constraint
A strong design constraint strategy carefully balances a wide range of electrical and manufacturing trade-offs. This month, we explore the key requirements, common challenges, and best practices behind building an effective constraint strategy.
All About That Route
Most designers favor manual routing, but today's interactive autorouters may be changing designers' minds by allowing users more direct control. In this issue, our expert contributors discuss a variety of manual and autorouting strategies.
Creating the Ideal Data Package
Why is it so difficult to create the ideal data package? Many of these simple errors can be alleviated by paying attention to detail—and knowing what issues to look out for. So, this month, our experts weigh in on the best practices for creating the ideal design data package for your design.
- Articles
- Columns
- Links
- Media kit
||| MENU - design007 Magazine
Estimated reading time: 4 minutes
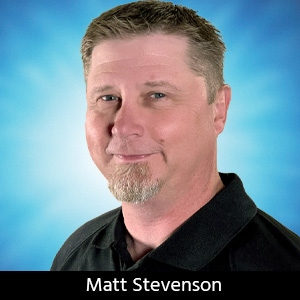
Connect the Dots: Designing for Reality—Outer Layer Imaging
Welcome to the next step in the manufacturing process—the one that gets the chemical engineer in all of us excited. I am referring to outer layer imaging, or how we convert digital designs to physical products. On a recent episode of I-Connect007’s On the Line with… podcast, we explained how the outer layer imaging process maps the design’s unique features onto the board.
At this point, the boards have gone through the electroless copper process. They are primed and ready for us to apply the photo image to the external layers, physically transferring the digital copper image of the design to the outer layer. Every component of the design layout—from pads to through-hole pads, trace routes, and ground fill—goes onto the manufacturing panel.
This transition from digital to physical is where the designer’s IP meets the board.
Dry Film vs. Liquid Photoimageable (LPI)
Once the surface is prepped, we apply the photoresist to the board. It is the mechanism that will accept the digital design and physically create it on the panel. There are two application methods available: dry film, and imaging using an LPI polymer that is like a solder mask.
Dry film is a thin layer of polymer, usually blue or purple. It comes in rolls like Saran wrap, and it’s applied with heat and pressure. When unwinding the roll, it physically laminates on the surface of the panel. This results in a uniform—usually a 2.3 mil—photoresist.
Dry film is more forgiving and more uniform in thickness, but that thickness can limit some of the fine line capabilities. Dry film is preferable to a certain point, depending on how small your design features are. Dry film can be a very effective choice in the hands of a crafty, experienced manufacturer. However, once you reach a certain point, LPI offers a better solution. If we use dry film below 2.5 mils, yield and quality can degrade a little. The classic dry film creates even more of a yield problem when traces and spaces get down to 2.25 mils.
Though it may seem counterintuitive, materials do not generally have an impact on the imaging process, even when we are talking about advanced applications like RF. Materials might present some challenges during etching depending on how the copper is adhered to the laminate, but all copper is essentially created equal, and the imaging process is agnostic when it comes to materials.
Ready For Imaging
So, we have a board with a blue or purple layer on both sides. Now what?
Since the photoresist on the panels can be sensitive to light—not just high-intensity light but any white light in the room—the imaging process takes place under yellow lights. The concept is the same as using red light in a darkroom to avoid triggering the film exposure process.
We use laser direct imaging (LDI) to apply the design pattern to the board. It functions like a laser printer. The laser scans an entire side of the panel, turning off for traces and turning on when there should be an absence of copper on the outer layer. This creates channels where we want copper to remain, so we can add more copper later for a more desirable thickness.
Now that we have identified what to keep and what to get rid of, we remove from the outer layer the photoresist from the features we want to keep. We remove it by developing it the way we used to develop photographs. We spray a mildly caustic solution on the back and front of the panel, which dissolves the stuff we don't want.
This creates channels where the copper traces go and clears the way for fun stuff like putting copper in the channels and electroplating. Having fun doesn’t mean we don’t need to be careful. There are a lot of microscopic effects that can snowball, leaving you with a board that differs from what you expected and your intended design.
Every process has some type of variation. In this process, we often see some level of variation in placement, size, or thickness. We avoid these issues by considering the placement of the drill hole on the pad, the placement of the pad relative to the drill hole during imaging, and the etching of that pad. This helps us meet our annular ring requirements down the road.
It is also an example of why it’s important to collaborate with your fabricators. When they say to be as conservative as possible or reasonable in your design, I recommend taking their advice. Doing so improves the manufacturing process, improves yield, and drives down costs.
To learn more about outer layer imaging, check out episode 7 of I-Connect007’s On the Line with…ASC Sunstone: Designing for Reality podcast.
Read Matt’s book, The Printed Circuit Designer’s Guide to Designing for Reality, or listen to his podcast here.
This column originally appeared in the September 2024 issue of Design007 Magazine.
More Columns from Connect the Dots
Connect the Dots: The Future of PCB Design and ManufacturingConnect the Dots: Proactive Controlled Impedance
Connect the Dots: Involving Manufacturers Earlier Prevents Downstream Issues
Connect the Dots: Stop Killing Your Yield—The Hidden Cost of Design Oversights
Connect the Dots: Designing for Reality—Routing, Final Fab, and QC
Connect the Dots: Designing for Reality—Surface Finish
Connect the Dots: Designing for Reality—Solder Mask and Legend
Connect the Dots: Designing for Reality: Strip-Etch-Strip