-
- News
- Books
Featured Books
- design007 Magazine
Latest Issues
Current IssuePartial HDI
Our expert contributors provide a complete, detailed view of partial HDI this month. Most experienced PCB designers can start using this approach right away, but you need to know these tips, tricks and techniques first.
Silicon to Systems: From Soup to Nuts
This month, we asked our expert contributors to weigh in on silicon to systems—what it means to PCB designers and design engineers, EDA companies, and the rest of the PCB supply chain... from soup to nuts.
Cost Drivers
In this month’s issue of Design007 Magazine, our expert contributors explain the impact of cost drivers on PCB designs and the need to consider a design budget. They discuss the myriad design cycle cost adders—hidden and not so hidden—and ways to add value.
- Articles
- Columns
Search Console
- Links
- Media kit
||| MENU - design007 Magazine
Estimated reading time: 4 minutes
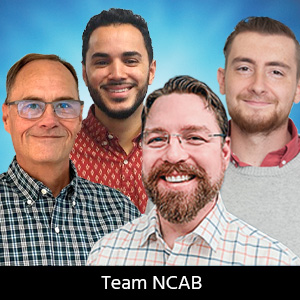
Fresh PCB Concepts: The Critical Nature of Copper Thickness on PCBs
PCBs are the backbone of modern electronics and the copper layers within these boards serve as the primary pathways for electrical signals. When designing and manufacturing PCBs, copper thickness is one of the most critical factors and significantly affects the board’s performance and durability. The IPC-6012F specification, the industry standard for the performance and qualification of rigid PCBs, sets clear guidelines on copper thickness to ensure reliability in different environments and applications.
Let’s delve into why copper thickness is critical on PCBs and how IPC-6012F plays a vital role in defining these requirements.
1. Electrical Conductivity and Current Carrying Capacity
One of the primary reasons for the precise specification of copper thickness is its direct relationship to electrical conductivity. Thicker copper layers can handle higher currents without causing excessive heat. If the copper layer is too thin, the traces may overheat when carrying large amounts of current, which could lead to board failure because of burnt-out traces or degraded components.
IPC-6012F outlines minimum copper thickness requirements depending on the type of PCB (Class 1, 2, or 3) and its intended application. This ensures that the board can handle the electrical load safely, avoiding failures that could occur if the copper is underspecified.
Example: For high-power applications, such as power supplies or industrial electronics, the IPC-6012F specification ensures the copper thickness is sufficient to handle the current without overheating or causing performance degradation.
2. Thermal Management
Copper thickness also plays a significant role in thermal management. A PCB's ability to dissipate heat depends on the thickness of its copper layers. Thicker copper improves heat distribution across the board, preventing hot spots that can damage components or lead to premature failure of the PCB itself.
IPC-6012F recognizes this by setting minimum copper thicknesses corresponding to different operating environments. Boards exposed to higher temperatures or needing enhanced thermal performance require thicker copper layers to dissipate heat efficiently. For high-reliability boards, such as those used in medical, aerospace, or military applications (Class 3), the need for thermal management is even more critical, as failure can have catastrophic consequences.
3. Mechanical Strength and Durability
The mechanical strength of the copper traces is also directly tied to their thickness. Thicker copper increases the robustness of the PCB, making it more resistant to wear, tear, and mechanical stress. This is especially important in environments where the PCB may be subject to vibration, physical shocks, or repeated flexing.
IPC-6012F ensures that copper thickness is suitable for the board’s expected use case. For example, in automotive or industrial applications where the PCB will experience constant vibrations, a thicker copper layer enhances the mechanical durability of the traces, reducing the risk of fracture or disconnection over time.
4. Signal Integrity in High-speed Applications
In high-speed digital circuits, signal integrity is paramount. Copper thickness affects the impedance of the PCB traces, which, in turn, influences signal timing, crosstalk, and noise. Variations in copper thickness can lead to inconsistent signal propagation, which is detrimental to the performance of high-speed circuits.
By adhering to copper thickness guidelines, PCB designers can ensure consistent signal integrity, reducing the risk of data loss or signal distortion, which is crucial for communication systems, computer processors, and other high-frequency applications.
5. Electromagnetic Compatibility (EMC)
Electromagnetic interference (EMI) can disrupt the performance of sensitive electronics. A thicker copper layer can help improve a PCB’s ability to shield against EMI and enhance its electromagnetic compatibility (EMC). In applications where EMC is critical—such as medical devices or communication systems—carefully controlling the copper thickness is necessary to mitigate interference and ensure compliance with EMC regulations.
IPC-6012F specifies copper thickness in such a way that it supports EMC, helping to reduce the risk of interference from external sources and maintain the integrity of the signals carried on the board.
6. Plating for Via Reliability
Vias, which connect different layers of a PCB, require reliable copper plating to ensure electrical continuity. IPC-6012F sets strict standards for the minimum copper plating thickness inside vias. This ensures robust connections between layers, which is essential for long-term reliability, especially in harsh operating environments.
Thin copper plating in vias can lead to failures, such as open circuits or intermittent electrical connections, especially under thermal cycling or mechanical stress. By adhering to the IPC-6012F standards, manufacturers can produce boards with reliable vias that can endure long-term use in demanding applications.
7. Longevity and Reliability
Finally, the thickness of copper directly correlates with the overall longevity and reliability of the PCB. Boards with thin copper layers are more prone to failure, particularly under demanding environmental conditions such as high temperatures, humidity, or mechanical stress. Thicker copper improves the durability and lifespan of the PCB, making it suitable for use in mission-critical applications.
The IPC-6012F specification ensures that PCBs meet the reliability standards required for different industries. For high-reliability Class 3 boards—such as those used in medical devices, aerospace, or defense—the copper thickness must meet stringent requirements to ensure the boards perform reliably over extended periods.
Conclusion
Copper thickness is a critical factor in the performance, durability, and reliability of PCBs.
The IPC-6012F specification provides comprehensive guidelines for minimum copper thickness based on the board’s intended application and class. Whether for thermal management, current carrying capacity, signal integrity, mechanical strength, or a combination of these factors, adhering to these standards ensures that PCBs can meet the rigorous demands of today’s electronic applications.
By following the copper thickness requirements outlined in IPC-6012F, designers and manufacturers can produce robust, high-performance PCBs that offer long-term reliability in even the most demanding environments.
Michael Marshall is a field applications engineer with NCAB Group.
More Columns from Fresh PCB Concepts
Fresh PCB Concepts: The Journey of a PCB—A Tale of Sustainability and CircularityFresh PCB Concepts: The Vital Role of Front-end Engineers
Fresh PCB Concepts: Understanding Your Export-controlled PCBs
Fresh PCB Concepts: Navigating Supply Chain Security and Traceability Through Standards
Fresh PCB Concepts: Fostering Loyal Relationships with PCB Design Engineers
Fresh PCB Concepts: Sustainable PCBs—Raw Materials and Compliance Methods
Fresh PCB Concepts: The Pros and Cons of Gerber, ODB++, IPC-2581
Fresh PCB Concepts: PCBs for Harsh and Extreme Environments, Part 2