-
- News
- Books
Featured Books
- design007 Magazine
Latest Issues
Current IssueShowing Some Constraint
A strong design constraint strategy carefully balances a wide range of electrical and manufacturing trade-offs. This month, we explore the key requirements, common challenges, and best practices behind building an effective constraint strategy.
All About That Route
Most designers favor manual routing, but today's interactive autorouters may be changing designers' minds by allowing users more direct control. In this issue, our expert contributors discuss a variety of manual and autorouting strategies.
Creating the Ideal Data Package
Why is it so difficult to create the ideal data package? Many of these simple errors can be alleviated by paying attention to detail—and knowing what issues to look out for. So, this month, our experts weigh in on the best practices for creating the ideal design data package for your design.
- Articles
- Columns
- Links
- Media kit
||| MENU - design007 Magazine
One Partial HDI Technique: mSAP
November 5, 2024 | Andy Shaughnessy, Design007 MagazineEstimated reading time: 2 minutes
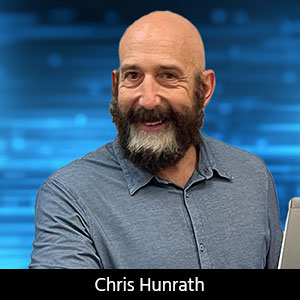
Partial HDI has shown itself to be very useful, allowing designers to escape route tight-pitch BGAs without moving to full HDI and the required sequential lamination. It’s almost the best of both worlds.
Chris Hunrath, vice president of technology at Insulectro, believes that mSAP just might be the trick for designers considering partial HDI. As Chris explains, the materials and equipment required for the mSAP process are easily available, and the process is well established. This could be a great option for designers working with BGAs that have a pitch of 0.5 mm or less.
Andy Shaughnessy: Chris, why would somebody choose to move to partial HDI? When does that process make sense, and when is mSAP the answer?
Chris Hunrath: It’s all about BGA pitch, microvia location, and circuit routing. I've not heard anyone call it partial HDI, but I like that expression because that explains it just right: the rest of that layer or the board might be more, let's say, conventional. But you neck down the traces to be able to do your fan-out. One of the things I've learned in the past couple of years from designers is that it's okay to make the trace narrower—you won’t degrade the signal integrity as long as that neck-down area is a short length. You can get your routing and still have some registration budget where you won't risk having defects like shorts and whatnot.
First, there’s a lot of what we call “head trash” about exactly what mSAP is. It's also really important to remember that pattern plating, which is done in North American PCB shops every day, is a semi-additive process. We're just taking it to the next level with mSAP. A lot of things are converging right now. You have the finer-pitched BGA packages that are being developed for multiple markets. That's another thing. It's one thing to have lots of room, but if the component is made for multiple markets, you're stuck with that pitch. You just can't go to a bigger pitch.
Another point is that exposure units keep getting better and more capable. If your board shop has a direct imaging machine, you likely already have that 25-micron capability. Some of the materials have come together as well, and we supply those materials.
To read this entire conversation, which appeared in the October 2024 issue of Design007 Magazine, click here.
Testimonial
"In a year when every marketing dollar mattered, I chose to keep I-Connect007 in our 2025 plan. Their commitment to high-quality, insightful content aligns with Koh Young’s values and helps readers navigate a changing industry. "
Brent Fischthal - Koh YoungSuggested Items
Calumet Electronics Continues to Advance Domestic HDI Circuit Board and Organic Substrate Capability
07/25/2025 | Calumet ElectronicsCalumet Electronics Corporation, a leading American-made printed circuit board (PCB) manufacturer, today announces another major milestone in its ambitious program to bring advanced high-density interconnect (HDI) and high-density buildup (HDBU) capabilities online.
The Death of the Microsection
06/26/2025 | Bob Neves, Reliability Assessment Solutions, Inc.I got my start out of college grinding and polishing PCB microsections. My thumbs are a bit arthritic today because of the experience (microsection grinders know what I mean). Back then, via structures were rather large, and getting to the center in six steps of grinding and polishing was easy compared to what my team has been doing recently at the lab.
Day 2: More Cutting-edge Insights at the EIPC Summer Conference
06/18/2025 | Pete Starkey, I-Connect007The European Institute for the PCB Community (EIPC) summer conference took place this year in Edinburgh, Scotland, June 3-4. This is the third of three articles on the conference. The other two cover Day 1’s sessions and the opening keynote speech. Below is a recap of the second day’s sessions.
American Standard Circuits to Exhibit at IMS 2025
06/12/2025 | American Standard CircuitsAnaya Vardya, President and CEO of American Standard Circuits & ASC Sunstone Circuits, announced that his companies will exhibit at the IEEE International Microwave Symposium (IMS 2025), taking place June 15-20, 2025, at San Francisco’s Moscone Center.
UHDI Fundamentals: UHDI Drives Unique IoT Innovation—Smart Homes
06/03/2025 | Anaya Vardya, American Standard CircuitsThe combination of UHDI's high-bandwidth capabilities and IoT's real-time data processing can lead to more efficient, immersive, and smarter IoT systems. This convergence of two revolutionary technologies is enabling quantum advancements in some very “unconventional” applications.