-
- News
- Books
Featured Books
- smt007 Magazine
Latest Issues
Current IssueSupply Chain Strategies
A successful brand is built on strong customer relationships—anchored by a well-orchestrated supply chain at its core. This month, we look at how managing your supply chain directly influences customer perception.
What's Your Sweet Spot?
Are you in a niche that’s growing or shrinking? Is it time to reassess and refocus? We spotlight companies thriving by redefining or reinforcing their niche. What are their insights?
Moving Forward With Confidence
In this issue, we focus on sales and quoting, workforce training, new IPC leadership in the U.S. and Canada, the effects of tariffs, CFX standards, and much more—all designed to provide perspective as you move through the cloud bank of today's shifting economic market.
- Articles
- Columns
- Links
- Media kit
||| MENU - smt007 Magazine
NEOTech Significantly Improves Wire Bond Pull Test Process
November 25, 2024 | NEOTechEstimated reading time: 1 minute
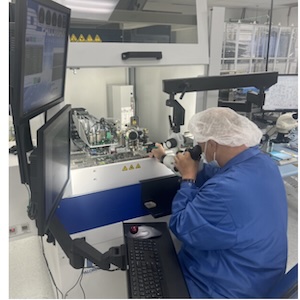
NEOTech, a leading provider of electronic manufacturing services (EMS), design engineering, and supply chain solutions in the high-tech industrial, medical device, and aerospace/defense markets, proudly announces a major advancement in its wire bond pull testing process, reducing manufacturing cycle time by more than 60% while maintaining industry-leading production yields of over 99.99%. This improvement reflects NEOTech’s commitment to continuous process enhancement and operational excellence.
The wire bond pull test is a critical method used to assess the quality and integrity of wire bonds in microelectronics. Leveraging extensive historical data and its exceptional process yield rate, NEOTech’s manufacturing engineers developed a robust random sampling methodology that ensures testing efficiency without compromising quality. The new sampling plan has dramatically reduced average testing time from 2.5 hours per assembly to approximately 1 hour per assembly.
This innovative process is fully compliant with the stringent requirements of MIL-PRF-38534 and MIL-STD-883, ensuring that NEOTech meets the highest quality and reliability standards. The process has been implemented on mission-critical, high-frequency RF assemblies — products recognized in the industry as highly complex and challenging to manufacture. NEOTech’s success in achieving these advancements demonstrates its expertise in addressing the rigorous demands of such sophisticated microelectronics applications.
“Achieving greater than 99.99% production yields is a remarkable milestone,” said Daniel De Haro, General Manager of the NEOTech Chatsworth site. “But our team didn’t stop there. They went above and beyond to implement innovative sampling techniques and streamline testing processes to significantly improve production cycle times. I’m incredibly proud of our engineers, technicians, and manufacturing teams for their dedication to excellence and their commitment to setting new benchmarks in microelectronics manufacturing.”
The transition to a sample-based testing methodology was supported by enhanced data collection and analysis, as well as the development of comprehensive training procedures. These efforts ensured that the NEOTech team could maintain its exceptional yield rates while increasing throughput and efficiency for its customers’ microelectronics circuit assemblies.
At the core of NEOTech’s success is its customer-centric approach. Offering a comprehensive suite of services — from design and prototyping to full-scale production and post-production support — NEOTech tailors its solutions to meet each customer’s specific needs. The company’s ability to provide personalized solutions, while also reducing time-to-market and optimizing costs, has earned it a strong reputation for delivering exceptional value.
Testimonial
"Our marketing partnership with I-Connect007 is already delivering. Just a day after our press release went live, we received a direct inquiry about our updated products!"
Rachael Temple - AlltematedSuggested Items
Coherent Announces Agreement to Sell Aerospace and Defense Business to Advent for $400 Million
08/15/2025 | AdventCoherent Corp., a global leader in photonics, today announced that it has entered into a definitive agreement to sell its Aerospace and Defense business to Advent, a leading global private equity investor, for $400 million. Proceeds will be used to reduce debt, which will be immediately accretive to Coherent’s EPS.
Flexible Circuit Technologies to Host Free Flex Heater Webinar
08/18/2025 | Flexible Circuit TechnologiesGlobal Supplier of flexible circuits, flex design services, and assembly/box-build services, Flexible Circuit Technology will host their latest webinar, "Thermal Precision Meets Flexibility: The Technology Behind Heater Circuits" on Tuesday, August 26th, 2025 at 11 AM EDT.
It’s Only Common Sense: Why Failure Is an Opportunity for Growth
08/18/2025 | Dan Beaulieu -- Column: It's Only Common SenseIt’s only common sense that failure, as painful as it may be, is one of the best teachers. Whether you’re running a business, managing a team, or navigating your personal journey, failure offers an unparalleled opportunity to learn, grow, and emerge stronger. If you’re not failing now and then, you’re likely not trying hard enough or pushing yourself out of your comfort zone. Here’s why failure is not just inevitable but also invaluable, and how to use it as a steppingstone to success.
20 Years of Center Nanoelectronic Technologies (CNT) – Backbone of German Semiconductor Research Celebrates Anniversary
08/14/2025 | Fraunhofer IPMSThe Center Nanoelectronic Technologies (CNT) of the Fraunhofer Institute for Photonic Microsystems (IPMS) is celebrating its 20th anniversary this year. Since its founding in 2005, it has developed into a pillar of applied semiconductor research in Germany and Europe. With its unique research cleanroom and equipment adhering to the 300-mm wafer industry standard, CNT is unparalleled in Germany and serves as a central innovation driver for the microelectronics industry.
Koh Young Showcases Advanced Dimensional Metrology and Inspection Solutions for Semiconductor and Wafer-Level Packaging at SEMICON India
08/14/2025 | Koh YoungKoh Young, the industry leader in True 3D™ measurement-based dimensional metrology and inspection solutions, will present its latest advancements for semiconductor and advanced packaging applications in Hall 1 Booth 1086 during SEMICON India 2025 held September 2-4, 2025, at Yashobhoomi (IICC), New Delhi, India.