Accurate Circuit Engineering on Passion and Pushing the Envelope
December 3, 2024 | Andy Shaughnessy, Design007 MagazineEstimated reading time: 3 minutes
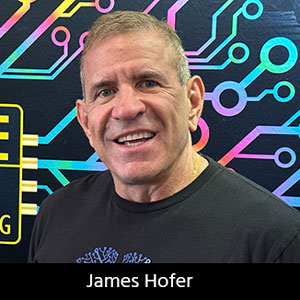
In this interview at PCB Carolina in November, James Hofer, general manager of Accurate Circuit Engineering (ACE), shares insights into the company’s innovative approach to component embedding and highlights the passion and dedication driving his team’s commitment to quality and innovation in PCB manufacturing. James is still having fun as they push boundaries and do some pretty cool things in the process.
Andy Shaughnessy: James, I understand you're working on some pretty cool stuff, doing things that haven't been done much before.
James Hofer: That's correct. As a leading prototype manufacturer, Accurate Circuit Engineering has consistently been at the forefront of quality, technology, and innovation. Recently, there has been significant interest in embedding components within printed circuit boards, and I am pleased to share that we have successfully completed a large, highly innovative project in this area. For this project, we embedded resistors of varying values directly into the PCB. Our capabilities can extend to integrating capacitors and other component chips seamlessly into the circuit board as well. There are several applications that can benefit from this technology. One purpose could be for space hardening, but there are a lot of other opportunities as well.
Shaughnessy: These are active components?
Hofer: Yes, they are active components directly placed onto an internal layers.
Shaughnessy: It seems like it would open a big of cans of worms.
Hofer: It can indeed, but when done correctly, it also opens new avenues of opportunity for exploration. Whether this approach evolves into a long-term, viable alternative to radiation hardening or ruggedizing printed circuit boards remains to be seen. However, this is precisely what Accurate Circuit Engineering excels at—being at the forefront of innovation, experimenting, and pushing boundaries to uncover new possibilities. I am incredibly proud of our success and of the strides we continue to make not only in this new approach, but many others as well.
Shaughnessy: Of course, it potentially frees up a lot of real estate.
Hofer: That's correct. While this does use some interior space and may introduce challenges with thickness due to the need to encapsulate components within active layers, proper engineering can overcome these obstacles. When executed effectively, it not only conserves valuable real estate on the board but also enhances protection for the embedded components.
Shaughnessy: Congratulations on that achievement. What else are you working on that you can discuss?
Hofer: We are working with some interesting milling techniques and I'm happy to say that we recently passed extended D coupon testing on six stacked microvias per side on a 26-layer board.
Shaughnessy: I know the industry has been saying we need to get away from stacking vias because of weak vias and too much pressure in one spot, but there are workarounds.
Hofer: That is correct and copper filling the vias is the best solution when you must directly stack. Additionally, the industry is adding some innovative laminates and prepregs that will aid in the reliability of stacked vias. Further, with the advancements in D coupon testing, which accelerates the time to delamination, we can now rigorously test these Stacks and materials to validate their long-term reliability.
Shaughnessy: James, you really seem to love your job.
Hofer: I do love it and I am passionate about what I do. Most of our team at the shop are also passionate about what we do, and that's why we make some of the best boards out there. It’s why we can do what other people refuse to or are unable to do. When you love something, you find a way to make it happen.
Shaughnessy: Thank you, James. It’s always great to talk to you.
Hofer: Thank you, Andy.
Suggested Items
Merlin Circuit Technology Achieves Prestigious JOSCAR Accreditation
01/14/2025 | Merlin Circuit TechnologyMerlin Circuit Technology is proud to announce it has been awarded the coveted Joint Approvals Group for Industry (JAG) Standard 001 (JOSCAR) accreditation.
Happy’s Tech Talk #36: The LEGO Principle of Optical Assembly
01/14/2025 | Happy Holden -- Column: Happy’s Tech TalkDr. Steven Case of Avanti Optics Corporation once advocated a new approach to photonic assembly, based on the LEGO principle. He compared today’s erbium-doped fiber amplifier (EDFA) technology to the crude point-to-point wiring of early model circuit boards, which gave way to modern circuit boards that could be considered prefabricated interconnects.
Expansion, Retirement, and New Leadership at FCT
01/09/2025 | Marcy LaRont, PCB007 MagazineIn the dynamic landscape of interconnect solutions, Flexible Circuit Technology (FCT) is making waves through significant leadership changes and expansion initiatives. Vice President Carey Burkett, newly appointed executive vice president Ray Cottrell, and marketing director Abby Meyer share their vision for steering the company toward innovative growth. FCT has a robust focus on diverse markets such as medical, automotive, consumer electronics, and HDI (high density interconnect). They are accelerating FCT’s mission to provide exceptional value and service to customers throughout the product lifecycle.
Flexible Thinking: Another PCB Design Paradigm Shift in the Works
01/09/2025 | Joe Fjelstad -- Column: Flexible ThinkingWe all read from the same technology scriptures and sing from the same design hymnals that serve the global congregation of printed circuit manufacturers and users, though there are still a few iconoclasts and heretics to challenge them in the service of largely positive change. Even subtle changes are hard to effect. People, especially those in manufacturing, do not like change because it disrupts the manufacturing floor routine. However, change, as even the ancient philosophers knew, is constant and required for continued growth and evolution.
Designers Notebook: Impact of Advanced Semiconductor Packaging on PCB Stackup
01/07/2025 | Vern Solberg -- Column: Designer's NotebookTo accommodate new generations of high I/O semiconductor packaging, printed circuit board fabrication technology has had to undergo significant changes in both the process methods and the criteria for base material selection and construction sequence (stackup). Many of the new high-function multi-core semiconductor package families require more terminals than their predecessors, requiring a significantly narrower terminal pitch. Interconnecting these very fine-pitch, high I/O semiconductors to the PCB is made possible by an intermediate element referred to as an interposer.