-
- News
- Books
Featured Books
- smt007 Magazine
Latest Issues
Current IssueThe Path Ahead
What are you paying the most attention to as we enter 2025? Find out what we learned when we asked that question. Join us as we explore five main themes in the new year.
Soldering Technologies
Soldering is the heartbeat of assembly, and new developments are taking place to match the rest of the innovation in electronics. There are tried-and-true technologies for soldering. But new challenges in packaging, materials, and sustainability may be putting this key step in flux.
The Rise of Data
Analytics is a given in this industry, but the threshold is changing. If you think you're too small to invest in analytics, you may need to reconsider. So how do you do analytics better? What are the new tools, and how do you get started?
- Articles
- Columns
Search Console
- Links
- Media kit
||| MENU - smt007 Magazine
Estimated reading time: 3 minutes
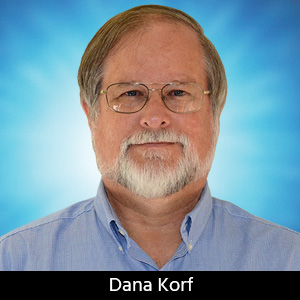
Dana on Data: Merging 2D Electrical, 3D Mechanical Worlds
Imagine the day when placing components and routing signal traces and power planes are not constrained by 2D PCB fabrication processes and materials. Astronauts working on the space station have equipment mounted on all axes. They are not constrained by having to stand on a flat surface. They already have a 3D printer at the space station. Why can’t we create PCBs in a 3D space?
With additive manufactured electronics (AME) and printed electronic (PE) technologies, reviewing the schematic and component placement routing strategies can utilize all three X, Y, and Z axes. Components can be additively formed using the interconnect materials. Traces and power distribution can be configured with unique shapes and routs on any angle, with the cross-section varying along its path, if required. Die and packaged components could conceptually be mounted on or under non-planar surfaces. Multiple conductor and dielectric materials are simultaneously being deposited to create the PCB. There are several additive manufacturing (AM) generic processes available and a multitude of potential hybrid approaches. New techniques are developed every year, being driven by 3D-minded designers and researchers.
2/2.5D vs. 3D PCB Interconnect
System packaging designers and architects work in a three-dimensional space. Their role is to pack all the mechanical and electrical parts into a defined volume while complying with their design, performance, environmental, and regulatory requirements/constraints. Rigid PCB designers must place and connect their components, restrained by horizontal layers using pads to connect to vertical holes for connectivity. Flexible PCBs provide three-dimensional layer shapes via bending, using 2D layout methods. Rigid-flex designs provide the ability to add multiple rigid interconnect layers to the flex PCB in the Z-axis, while still being constrained by vertical via technology. People are trained to think using these constraints. eCAD tools, in general, provide excellent algorithms and software for this environment.
Currently, mechanical CAD software can create 3D shapes, interconnect, and formed components. AME manufacturers have CAM software that can merge Gerber 2D data with the 3D files, though the electrical information has not been transferred yet. It’s a good option to merge the 2D PCB electrical and 3D mechanical worlds together.
3D interconnect requires designers to replace many existing techniques and replace them with mechanical 3D techniques. Here are a few examples:
- Replace vias with 3D traces (3DTs): Existing vertical interconnect creates pads on layers, separates them with dielectric, removes material by drilling (aligning to larger pads), cleans, then plates to create the interconnect. This hole is required to be the same diameter and thickness on the Z-axis. AME 3D interconnects eliminate the drilled/plated hole and the larger pad, replacing it with a trace that can travel at any Z-axis angle. This trace can change its shape along the way. BGA via-in-pad connections do not require a capture pad, or via. The 3DT can just connect into the bottom of the surface pad (eliminating laser drilling, VIPPO processing, etc.). Stacked, buried, and blind vias are replaced by a 2DT trace, potentially eliminating existing reliability issues.
- Form factor: The AME does not need to be flat and have edges. It can replace sides with surfaces that can be curved. Current manufacturing technologies require one flat surface on the bottom side. This can potentially be solved using other AM processes.
- Impedance traces: Today, integrated controlled impedances are formed with microstrip and stripline configurations. AME offers embedded twisted pairs and coaxial lines in addition to stripline configurations. One technique creates an airline from the surface.
- Unique formed surface components: Microware antennas often extrude from the surface. A vertical wall can be formed between pads/holes to provide a longer creepage distance.
- Elimination of solder mask and legend: The dielectric can be printed over the surface conductor to provide insulation. A secondary solder mask may not be required. Nomenclature can be printed using a conductor under the surface dielectric, the dielectric can be raised higher to create lettering, or the nomenclature and be inset into the outer dielectric layer. Think differently.
The industry is diligently collaborating with high schools, colleges, and universities to train the next generation of engineering workforce to start thinking using AM processes and materials. Higher volume production is being developed and PCB prototype companies will be able to use this technology for quick-turn PCBs that could be easily converted to traditional laminate-based PCBs soon. It is important for the existing workforce to become aware of AME technology and drive the new applications. IPC and ASTM standards are currently being developed/defined in readiness for these new applications.
Dana Korf is the principal consultant at Korf Consultancy LLC.
More Columns from Dana on Data
Dana on Data: Resurrecting IPC Class 1Dana on Data: The Evolution of Fabrication Drawing
Dana on Data: The Insane PCB DFM Process
Dana on Data: eCAD PCB Design Deficiencies
Dana on Data: Nuke the Netlist
Dana on Data: Simplify PCB Documentation
Dana on Data: IPC AME Standards Development Launched
Dana on Data: Filling the Gap When Tribal Knowledge Runs Out