Estimated reading time: 5 minutes
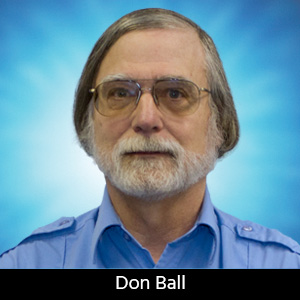
The Chemical Connection: Surface Finishes for PCBs
Writing about surface finishes brings a feeling of nostalgia. You see, one of my first jobs in the industry was providing technical support for surface cleaning processes and finishes to enhance dry film adhesion to copper surfaces. I’d like to take this opportunity to revisit the basics, indulge in my nostalgia, and perhaps provide some insight into why we do things the way we do them in the here and now.
In 1974, most circuit boards were double-sided, plated through-hole panels, although some people were still using eyelets to connect the sides of the board. These were small, hollow copper tubes pushed through the drilled holes and soldered or crimped to the surface copper to provide communications between the sides. Multilayer production was just beginning, mostly limited to three or four layers. Alkaline etchants had just been introduced (an anniversary I do not celebrate except to remind myself that the alternatives were worse). Fully aqueous dry film photoresists were also relatively new and replaced the first solvent-based dry films because, even in 1974, people recognized that the solvents were not good for you. The problem was fully aqueous resists did not adhere to the copper nearly as well as the solvent-based dry films.
Then, as now, copper foil was produced by plating it onto a smooth, stainless-steel roller; the thickness of the foil was controlled by the speed of rotation through the plating bath. The side against the surface of the roller was smooth and shiny while the side away from the roller was rough. The foil was laminated to the substrate with the rough side facing down to provide more surface area for better adhesion to the substrate. This reduced the possibility of the copper delaminating because of heat or environmental conditions, which was not uncommon. Most surface finishing was concerned with preparing the smooth side of the copper for maximum adhesion of fully aqueous dry film resists.
The objective of the surface prep was to remove organics and oxides from the surface that would interfere with the resist adhesion as well as to roughen the smooth surface of the copper to provide more surface area for adhesion. The most common way to accomplish this task was with mechanical scrubbers. Several companies provided conveyorized scrubbers using rotating abrasive brushes with either silicon carbide or aluminum oxide, making it possible to process many circuit panels in a short amount of time. This left a bright surface visibly roughened by the abrasive. Alternatives were pumice scrubbers using a volcanic pumice slurry to scrub the copper surface, and chemical cleaning using a two-step process comprising a basic cleaning solution like a mild sodium hydroxide to remove any organics, followed by an acid rinse (typically a 3–5% sulfuric acid solution) to neutralize the basic cleaner, remove any oxides, and lightly roughen the copper surface. The pumice scrubbers left the best surface for resist, but with an abrasive slurry splashing around inside, the machines tended to self-destruct. They also sometimes left pumice particles embedded in the copper, which led to rejects down the line. Chemical cleaning lines were longer than mechanical scrubbers and required chemical maintenance, which many wished to avoid, so mechanical scrubbers became the surface preparation method of choice in the 1970s.
Panels came out of a mechanical scrubber looking bright, but were they really clean? One problem encountered was the abrasive particles were contained in a nylon matrix, either in a Scotch-Brite type form or in a bristle brush form. Under the right brush pressure, only the abrasive came in contact with the copper. However, too much pressure could bring the nylon in contact and smear on the copper, causing resist adhesion problems. “How clean is clean?” was a constant refrain at PCMI meetings in the ‘70s and early ‘80s.
Thus, the water break test was devised, the bane of my existence. The theory was that after cleaning, the copper surface should be able to retain any water on the surface as a thin sheet for 30 seconds before breaking into beads. If this happened, the panel was clean and ready for resist lamination. Or was it? Most of the time, that assumption was correct but other factors affect water break, so a good water break test didn’t necessarily mean the surface was ideal for resist adhesion. For example, one customer complained he was getting poor resist adhesion despite water break tests that showed the water film was lasting over a minute. It turned out he was adding detergent (Dawn) to his rinse water to guarantee a good water break test. This left a slightly basic surface on the copper that the resist he was using at the time absolutely did not like.
As the industry evolved in the 1990s, other weaknesses in using mechanical scrubbing as surface preparation for resist adhesion became apparent. Scrubbing hardened the copper, making it more brittle with a tendency to crack, which caused problems with flexible circuits. As the number of layers in multilayer boards increased, the substrates became thinner. Engineers discovered the scrubbing process stretched the dimensions of these thinner substrates in the direction of travel through the scrubber, so it became more difficult to correctly line up the layers properly in the multilayer lamination process, especially as the layer count got higher. As a result, mechanical scrubbers gradually fell out of favor, and chemical cleaning became the surface prep of choice. Between 1975 and 1985, we sold more than 600 mechanical scrubbers. Between 2014 and 2024, we sold six.
Dry films and laminates have improved since those early days. Now, I prefer to get reverse-treated foils (RTF) for testing, which are laminated with the rough side out, something that wouldn’t have been considered in the early ‘70s. This provides an excellent roughened surface profile for resist adhesion and is worth the extra cost because no micro-etch is needed, just a simple acidic cleaner to remove any oxide or conversion layers. The panel is then ready to laminate, making it easier than even the old mechanical scrubber. These days we receive very few questions on surface prep for resist adhesion, so maybe we finally have a handle on this type of surface prep.
This column originally appeared in the March 2025 issue of PCB007 Magazine.
More Columns from The Chemical Connection
The Chemical Connection: Sales Organization from a Capital Equipment PerspectiveThe Chemical Connection: Through-glass Vias in Glass Substrates
The Chemical Connection: Reducing Defects in Circuit Board Production
The Chemical Connection: Common Misconceptions in Wet Processing
The Chemical Connection: Earthquakes, Astronauts, and Aquatics—A Lighter Look at the Past
The Chemical Connection: Better Fabs Attract a Better Workforce
The Chemical Connection: Can Changing Spray Nozzles Improve My Etch Quality?
The Chemical Connection: Getting the Best from Your Cupric Chloride Etchant