-
- News
- Books
Featured Books
- smt007 Magazine
Latest Issues
Current IssueSupply Chain Strategies
A successful brand is built on strong customer relationships—anchored by a well-orchestrated supply chain at its core. This month, we look at how managing your supply chain directly influences customer perception.
What's Your Sweet Spot?
Are you in a niche that’s growing or shrinking? Is it time to reassess and refocus? We spotlight companies thriving by redefining or reinforcing their niche. What are their insights?
Moving Forward With Confidence
In this issue, we focus on sales and quoting, workforce training, new IPC leadership in the U.S. and Canada, the effects of tariffs, CFX standards, and much more—all designed to provide perspective as you move through the cloud bank of today's shifting economic market.
- Articles
- Columns
- Links
- Media kit
||| MENU - smt007 Magazine
Estimated reading time: 5 minutes
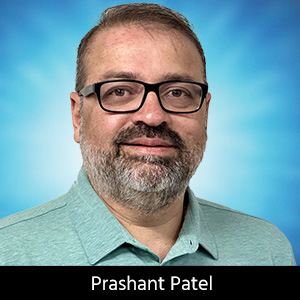
Facing the Future: Time for Real Talk, Early and Often, Between Design and Fabrication
There has always been a subtle but significant divide between those who design and those who build printed circuit boards. It’s not a hostile gap, but it is a real one, and in today’s high-speed, high-complexity, high-stakes environment, that gap is costing us more than time and yield. It’s costing us innovation.
PCB designers are brilliant problem-solvers, as are fabricators. Yet too often, they’re solving distinct problems on separate timelines, with different sets of constraints. The result? Economically unfeasible designs, builds that don’t meet the original intent, and a lot of back-and-forth that delays everything from prototyping to production. It can’t be this way if we’re serious about tackling next-generation challenges, whether it’s AI hardware, 5G systems, or life-saving medical devices. Bridging the gap between design and fabrication is essential and starts with changing how we collaborate. To bridge the design-fab divide, collaboration needs to start sooner and be more deliberate.
Designers are under pressure to deliver complex boards at warp speed. They’re balancing impedance constraints, thermal profiles, signal integrity, miniaturization, and a dozen other specs. Even the most perfectly simulated design can hit a wall if the fabricator can’t build it efficiently or at all because of a lack of material availability, tooling limits, or process tolerances.
Fabricators, on the other hand, are experts at translating ideas into reality. They understand the physical limits of copper, prepreg, laminate, plating, and drill technology. They understand lab successes and production realities, but their input arrives after crucial design choices are finalized.
Bringing these two sides together earlier sparks innovation, encourages joint decision-making, and aligns the product vision with the production capability from day one. The design-to-fabrication process is easily misunderstood:
- Material mismatches: A designer specifies an exotic material based on theoretical performance, only to discover it’s not in stock, or can’t meet UL requirements
- Layer stackup confusion: Miscommunication around copper weights, impedance targets, or dielectric spacing can throw off the whole design intent
- Overly tight tolerances: Designers sometimes specify tolerances tighter than the shop can guarantee, leading to unnecessary yield loss or costly revisions
- Gerber file gaps: Incomplete or outdated fabrication notes still plague the industry, especially in prototype hand-offs
- Version control breakdowns: When revisions aren’t tracked or shared consistently, the fab shop may build the wrong rev, costing both time and trust
The root of these problems is the lack of consistent, structured dialogue between the people building and designing the boards. Fortunately, technology has the tools to bridge this communication divide. From AI-driven design assist tools to real-time DFM (Design for Manufacturability) checkers, we’re entering a new era of intelligent collaboration:
- AI-assisted layout tools: Can recommend trace routes, via placements, and even stackups based on historical manufacturing data and fab feedback
- Cloud-based DFM platforms: Allow designers to upload their layouts and receive instant manufacturability feedback from specific fabricators
- Shared dashboards and secure design portals: Make it easier than ever for engineers and fabricators to collaborate without endless email chains or FTP sites
However, tools alone don’t fix relationships. They support them. What matters is how people use these tools to build trust, clarify intent, and streamline handoffs. In a recent case, a medical device startup partnered with their PCB fabricator before they completed the layout. They had a novel design—fine-pitch BGAs, tight impedance constraints, and high-speed differential pairs across multiple layers. Rather than tossing over a completed design, they engaged the fabricator’s CAM team early to co-develop a stackup strategy and validate material availability. The result? They avoided multiple re-spins, met their timeline, and cut costs by simplifying the via design thanks to the fabricator’s suggestions.
In another example, an aerospace client with demanding thermal constraints brought their board house into the thermal modeling phase. Together, they tested different copper weights and bonding options to ensure durability under flight conditions. That collaboration not only met the requirement, it unlocked a better-performing product.
These examples aren’t flukes. They’re proof that when designers and fabricators act as partners—not just vendors and clients—they create a better product. Bridging the gap starts with changing our habits and culture. Here are five ways to make it happen:
- Talk before layout. Don’t wait until the files are ready to engage your fabricator. Get their input on stackups, materials, and capabilities while you’re still drafting.
- Share your intent. Don’t just send files. Explain the why behind your design. What’s critical? What’s flexible? This helps fabricators prioritize and troubleshoot.
- Standardize your documentation. Clear, consistent fab notes and drawings save everyone time. Don’t make your fabricator guess.
- Create feedback loops. Ask your fab partner what could have been better and listen. Use that insight to improve future designs.
- Invest in relationships. Build long-term partnerships with fabricators you trust. The more they know your team, the better their input becomes.
We’re entering a new era in electronics. Designs are more complex, product lifecycles are shorter, performance, reliability, and compliance expectations are higher. Yet, we’re still treating the handoff from design to fab like a cold transaction. That’s not only inefficient; it’s unsustainable.
The future belongs to teams who collaborate by design and treat fabrication not as a finish line, but as a co-creative process that begins on the whiteboard. It belongs to fabricators who lean in, offer guidance, and become trusted design allies.
We don’t need to reinvent the wheel; we simply need to pick up the phone earlier, open the design file sooner, and start talking like we’re on the same team, because we are.
In our connected, fast-moving, high-reliability world, bridging the gap between design and fabrication is the foundation of building boards that work, products that ship, and partnerships that last.
Prashant Patel is the founder and president of Alpha Circuit.
More Columns from Facing the Future
Facing the Future: Challenges and Opportunities in Reshoring PCB ManufacturingFacing the Future: Investing in R&D to Stay Competitive
Facing the Future: The Role of 5G and Beyond in Shaping PCB Demand
Facing the Future: Successfully Navigating the Uncertain Path Ahead
Facing the Future: Technology Trends Shaping the PCB Market
Facing the Future: The Evolution of the North American PCB Industry
Facing the Future: Charting the Path Forward for the American PCB Industry