-
- News
- Books
Featured Books
- pcb007 Magazine
Latest Issues
Current IssueThe Hole Truth: Via Integrity in an HDI World
From the drilled hole to registration across multiple sequential lamination cycles, to the quality of your copper plating, via reliability in an HDI world is becoming an ever-greater challenge. This month we look at “The Hole Truth,” from creating the “perfect” via to how you can assure via quality and reliability, the first time, every time.
In Pursuit of Perfection: Defect Reduction
For bare PCB board fabrication, defect reduction is a critical aspect of a company's bottom line profitability. In this issue, we examine how imaging, etching, and plating processes can provide information and insight into reducing defects and increasing yields.
Voices of the Industry
We take the pulse of the PCB industry by sharing insights from leading fabricators and suppliers in this month's issue. We've gathered their thoughts on the new U.S. administration, spending, the war in Ukraine, and their most pressing needs. It’s an eye-opening and enlightening look behind the curtain.
- Articles
- Columns
- Links
- Media kit
||| MENU - pcb007 Magazine
Estimated reading time: 1 minute
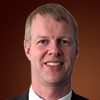
Goodbye to Trial and Error?
All the time you spend at the production line for trial-and-error runs, just to get your production board right, takes away from your real production time. It comes on top of the time spent for trial and error at the screenprinter, and any other equipment in the line. All this can take an hour or more for each production board but, with all the tools now available, it can easily be significantly reduced. In addition, though, there are time-consuming actions (like loading all the feeders) to get right before the first error-free board comes out of the machine.
So, how do you minimize the whole trial-and-error process to ensure that, when a program starts up and feeders and toolbits are already on the system, the first board coming out of the machine is immediately good?
A perfect first board would mean that the correct components were all picked from the correct feeder and placed on the correct location at the correct placement angle. Guaranteeing this means ensuring that all the many pre-defined variables are correct: enough paste, exact board positioning, precise artwork, correct components picked by the correct toolbits and placed exactly. The more variables that are incorrect, the longer the ramp-up will take. The more programs each shift that require correcting, the shorter your effective production time and thus fewer boards produced. And during ramp-up, it’s better that the system stops to signal a fault than finding it out at the end during board test. It also helps save ramp-up time if all components are actually picked to get the program started immediately without false starts.
Read the full column here.
Editor's Note: This column originally appeared in the January 2014 issue of SMT Magazine.
More Columns from SMT Trends & Technologies
SMT Trends and Technologies: What is Your Real Output?SMT Trends & Technologies: Goodbye to Trial and Error?
SMT Trends and Technologies: Pick and Paste
SMT Trends and Technologies: Doing More Than One Thing at a Time
SMT Trends & Technologies: Clash of Clans - The New Expansion of PCB Assembly Equipment
What is Your Real Output?