-
- News
- Books
Featured Books
- design007 Magazine
Latest Issues
Current IssueProper Floor Planning
Floor planning decisions can make or break performance, manufacturability, and timelines. This month’s contributors weigh in with their best practices for proper floor planning and specific strategies to get it right.
Showing Some Constraint
A strong design constraint strategy carefully balances a wide range of electrical and manufacturing trade-offs. This month, we explore the key requirements, common challenges, and best practices behind building an effective constraint strategy.
All About That Route
Most designers favor manual routing, but today's interactive autorouters may be changing designers' minds by allowing users more direct control. In this issue, our expert contributors discuss a variety of manual and autorouting strategies.
- Articles
- Columns
- Links
- Media kit
||| MENU - design007 Magazine
Estimated reading time: 3 minutes
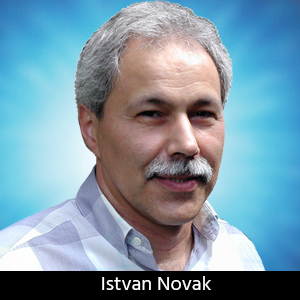
Why S11 VNA Measurements Don't Work for PDN Measurements
At the beginning of the previous column, we compared the one-port and two-port vector network analyzer (VNA) measurement setups for PDN measurements and said that one-port VNA measurements don't work well for PDN applications. Our argument was that the one-port scheme (shown in Figure 1), unless the DUT is connectorized, requires an extra connection beyond the calibration plane to reach the DUT.
Figure 1: Connection discontinuity in one-port VNA PDN measurements.If we want to measure very small impedances, this extra discontinuity, Zconnection, usually a small series resistance and inductance, becomes detrimental even at very low frequencies. By hand-soldering, we may be able to get the extra connection as short as 1 mm (40 mils), which may represent, say, 1 nH inductance and 1 milliohm resistance.
If we need to measure PDN impedances at or below 5 milliohms values, we will be limited by the inductive reactance of Zconnection above 1 MHz and by the resistance of Zconnection below 100 kHz. This is illustrated in Figure 2, where we also show on the same plot the 50-ohm reference impedance value and our 5-milliohm target impedance. In the usual high-frequency VNA measurements, where we want to measure DUTs with impedances close to 50 ohms, the same 1 nH series inductance would create minimal error anywhere below 1 GHz.
Note that this error due to the series discontinuity is not the characteristic of the VNA; this limitation is inherent to any measurement setup where only one cable or one pair of wires connects to a low-impedance DUT and we have extra connection beyond the calibration plane.
We can eliminate the series discontinuity, even if the DUT is not connectorized, by using wafer probes calibrated to their tips. This may be the subject of a future column.
Figure 2: Comparing the 50-ohm VNA impedance and a 5-milliohm PDN impedance target to the impedance magnitude of a 1-mOhm 1-nH Zconnection discontinuity.
However, there is yet another, even bigger problem when we measure low impedances with a one-port VNA setup. To understand this, we need to look at how the VNA works. In one-port connections, the VNA measures the outgoing wave, called incident wave, because this is the wave entering the DUT and the backward-travelling wave, called reflected wave. The complex ratio of these waves is called the voltage reflection coefficient, commonly denoted by capital gamma (Γ). Γ has a direct relationship to the impedance connected to the VNA port, as shown in Equation 1. If we invert the voltage reflection coefficient formula, we get the complex unknown impedance:
In these expressions Z0 is the nominal connection impedance of the VNA, usually 50 ohms. Γ becomes identically -1 when the unknown impedance is zero. Since the reference is the 50-ohm VNA impedance, Γ becomes close to -1 for any impedance much smaller than 50 ohms. For instance, if the impedance is 5 milliohms, Γ = -0.9998. And here comes the problem: VNAs are not prepared to measure Γ with this accuracy; they are optimized to measure accurately Γ for impedances close to 50 ohms. When |Γ| approaches one, VNAs will have an error in the order of 1%, which will prevent us from measuring impedances lower than a few hundred milliohms.
We have to note that this is not an issue when we simulate the circuit, because in a simulator we can afford to have much higher precision of calculations.
The above problem can be illustrated by Figure 3. The figure shows measurement results generated by simulations, when we can accurately control the errors. We assume a single capacitor to be measured: a 10 uF capacitor with 5 mOhm ESR and 1 nH ESL. The top graph shows the result assuming we measure with 1-port setup, where the VNA has a 0.05% scaling error and a noise floor approximately 10-5 times below the full scale.
Figure 3: Comparing one-port and two-port VNA setups when we assume to measure a 10 uF 5 mOhm 1 nH capacitor.
The thin green line is the ideal result, the thick blue line shows what the instrument would report and the red line shows the percentage error between the two. The error at the series resonance frequency is 250%. In contrast, when we assume the same scaling error and noise floor, but instead use two-port shunt through connection, the error stays below 5% over the entire frequency range.
About the author
Istvan Novak is a distinguished engineer at SUN Microsystems working on signal and power integrity designs. He can be reached at istvan.novak@att.net.
More Columns from Quiet Power
Quiet Power: An Evolution in PCB Design CostsQuiet Power: The Effect on SI and PI Board Performance
Quiet Power: 3D Effects in Power Distribution Networks
Quiet Power: Noise Mitigation in Power Planes
Quiet Power: Uncompensated DC Drop in Power Distribution Networks
Quiet Power: Ask the Experts—PDN Filters
Quiet Power: Friends and Enemies in Power Distribution
Quiet Power: Be Aware of Default Values in Circuit Simulators