-
- News
- Books
Featured Books
- pcb007 Magazine
Latest Issues
Current IssueThe Hole Truth: Via Integrity in an HDI World
From the drilled hole to registration across multiple sequential lamination cycles, to the quality of your copper plating, via reliability in an HDI world is becoming an ever-greater challenge. This month we look at “The Hole Truth,” from creating the “perfect” via to how you can assure via quality and reliability, the first time, every time.
In Pursuit of Perfection: Defect Reduction
For bare PCB board fabrication, defect reduction is a critical aspect of a company's bottom line profitability. In this issue, we examine how imaging, etching, and plating processes can provide information and insight into reducing defects and increasing yields.
Voices of the Industry
We take the pulse of the PCB industry by sharing insights from leading fabricators and suppliers in this month's issue. We've gathered their thoughts on the new U.S. administration, spending, the war in Ukraine, and their most pressing needs. It’s an eye-opening and enlightening look behind the curtain.
- Articles
- Columns
- Links
- Media kit
||| MENU - pcb007 Magazine
Estimated reading time: 10 minutes
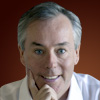
Solving Your DAM Problems: Remove Variation & Your Company Wins
Editor's Note: This article originally appeared in the July 2012 issue of The PCB Magazine.
In my last column, The Reliability Mindset, I demonstrated that the consistency of your downtime matters considerably. Short consistent bursts, such as scheduled downtime, are much better than long inconsistent bursts caused by an equipment or a process breakdown. This law of a better result and better flow with small precise events, which happen on a predictable metronome beat, and last for the same time with no variation, is what the entire Toyota Production System (TPS) is all about. Nothing more, nothing less. Simple.
Somehow in Lean, which was an attempt to translate TPS into our language and culture, this core principle was obscured. Yes, Lean was introduced with the seven forms of waste, but for many of us Lean was about cleaning up the shop and removing the waste of waiting. For example, constraining WIP levels reduces waiting time, allowing product to get through the factory quicker. This is all good stuff; however, when you understand the core principle at the heart of TPS, you move away from reading a recipe in the cookbook to becoming a creative, valuable chef. In other words, you move away from methodology to construct. A company that can do this will outperform a company that can’t. This is the reason why American auto manufacturers, despite their impressive gains, still aren’t performing as well as Toyota. Toyota understands why TPS works. American manufacturers continue to miss it.
The goal of TPS is simple. Anything that interrupts the metronome beat, the precise unvarying movement of materials through the factory, must be identified and fixed. Not only that, this simple metric is the only operational metric you need to know if things are running well or there are problems. It is the only thing that operators need to be focused on to determine if they are doing their job. It is the reason why most Toyota factories can be run with a paper and pencil and a simple Excel spreadsheet. There isn’t much variation. The decisions are simple. It’s all about time management. It is all about Takt Time. Takt Time is how Toyota eliminates DAM variation. It is why, even when they stumble, they make a pot of gold.
I remember, long ago, being at the Narita Airport just outside of Tokyo, waiting to board my bus to the Imperial Hotel. My ticket had a boarding time of 1:17. At 1:10, I asked if the bus sitting in front of me, which said “Imperial Hotel” on it, was mine. Apparently, there are a number of Imperial Hotels in Tokyo. I was told politely to wait. At 1:15 I went to the counter again, pointing at another bus. I was told politely to wait. At exactly 1:17, where there must have been three or four clocks around me, all calibrated precisely and reading 1:17, I was told to board my bus. There were no crowds, but there were a lot of people getting on and off, and everything was in constant motion with busses coming and going, bags moving out of the busses and into the busses, with maybe 10 people (if that) orchestrating the entire operation. Everyone was in a tightly compacted area. You could set your watch to what they were doing.
Why does Southwest Airlines make money? They do things the same way. Their flight schedule rarely changes. Everybody knows what to do, including passengers. The amount of time at the gate is short, with no deviation. Everything, more than any other airline, happens on time. You can set your clock to Southwest Airlines.
How about the PCB industry? We aren’t that precise. Consider the release of product into your factory and the precision of when product moves from one operation to another operation. What we are talking about is called the variation in arrival rate, and this, too, is another form of DAM variation. If you make the arrival rates through the factory more precise, you make a big step to be like Toyota or Southwest.
To see the importance a consistent metronome-like arrival rate has, we are going to use a discrete event model as shown in Figure 1. In the three-step process of Figure 1, product arrives, is processed, and then exits and moves on. For demonstration purposes, we will set the processing time to one hour, with no variation. Bins of material are released and one bin of material gets loaded into Machine 1 instantly, with no variation. The only variation considered is the variation in the arrivals of bins to the staging area.
Figure 1: The simple three-stage discrete event model of 1) arrival of bins; 2) processing of bins with a staging area or queue; and 3) exit of bins.
In Figure 1, there are only two parameters to be considered: the average arrival rate and the coefficient of variation (CV) for arrivals. The coefficient of variation allows us to classify a process as having low variability, medium variability, or high variability. Dividing the standard deviation by the mean defines CV. Low-variability is when the CV is less than 0.75. A medium-variability process would result when the CV is between 0.75 and 1.33. A high-variability process would result when the CV was greater than 1.33.
To understand the effect of the variation in arrival rate to cycle time for a given level of utilization, a DOE was run on the discrete event model shown in Figure 1. The results are shown in Figures 2, 3, and 4.
Figure 2: The Neural Net Model fit from the 4,440 datum derived from the experimental runs on the discrete event model. This shows the average cycle time as a function of the CV for the arrival rate and the utilization level on the equipment.
Figure 3: One way to reduce waiting time on the parts and meet short delivery schedules is to run fewer parts through the factory by reducing the utilization level on the equipment. When you do this you also have fewer total sales for the same product mix. This figure also shows as you decrease the utilization level on equipment, the beneficial effect of consistent arrival times diminishes.
Figure 4: Another way to reduce waiting time on the parts is to keep the utilization at 90%, but reduce the CV for arrivals to 0.75!
The famous utilization curve that stays flat and then soars upwards may be familiar to you, as shown on the right side of each of the charts in all three figures. This is the curve that gets thrown up where you are told as a rule of thumb not to go over 80% capacity or utilization. Such general rules of thumb, even with fancy charts, are dangerous to implement without proper understanding.
For example, if you are tasked with shortening up the cycle time with a highly utilized operation, you would likely reduce the average arrival rate, and not do anything with regards to the variation in arrivals. You would likely improve the cycle time, but you would decrease the throughput, because you are running less product through the operation. Keep in mind, less throughput means less money.
We see in Figure 2, at 90% utilization, with a CV of 1.9 (high-variability case) we are at a 17.1 hour cycle time through the operation. Remember the process time is only 1 hour! Figure 3 shows we can get to a four-hour cycle time if we drop the utilization to about 80%. Figure 3 also shows, as expected, that the effect of the variation in arrivals decreases with lower levels of utilization.
There is another way to get to an average cycle time of four hours and stay at 90% utilization. Looking at Figure 4, if the CV of arrivals is reduced from 1.9 to 0.75, you achieve the target objective. In general, the rule of thumb shouldn’t be to reduce the utilization of equipment first, but instead, reduce the CV of arrivals and other DAM variations such as unscheduled down time first. Typically these are low-cost things to do, but they require discipline, coordination, training, and motivation.
Since these curves could have been drawn up with theoretical formulas, you might ask yourself, why the discrete event simulation? There are many forms of DAM variation, besides arrival rate. For example, what arrival rate do you need, when the coefficient of variation is 0.75, that will give you a six-hour lead time with better than 85% utilization considering other factors such as down time, process time, setup time, worker proficiency, and so on. You can’t find this answer with a formula. You can’t conduct this experiment in the factory without a lot of cost. You figure out answers to these types of questions and develop a honed intuition for this kind of complexity by building, testing, verifying, and analyzing a discrete event model.
Without doing the model building, how can you physically grasp this variation in arrival rate and other DAM variation items in your head? Think of a freeway. What happens when there is an accident? It’s easy to understand: You will be late.
Now you are on the freeway and there are no accidents. When there aren’t many cars on the road you can go pretty fast. As more and more cars start to come onto the freeway, you still can move pretty fast, but you have to be more aware and hit the brake from time to time. At this point you are moving up the flat part of the utilization curve. At the point that the freeway starts to approach full utilization, or maximum capacity, you suddenly can’t move at all. You are now at the steep section of the utilization curve.
The way civil engineers have tried to add more capacity to the freeway so that there is less of a problem at higher levels of utilization (such as in rush hour) is to add those irritating traffic lights on the ramp. (Believe it or not, reducing the coefficient of variation on the arrivals onto the freeway helps. So don’t run the light like some people do.)
What could be done to improve the freeway cycle time with even more cars? Remove the variation in the speed of cars. In the future we may go into a queue, where we no longer have control of our vehicle, we enter the freeway at a precise time, we don’t have any control over the lane or speed. Our only control is what exit we want to take. When we exit, we resume control of our vehicle.
If you understand this, you not only want to have short predictable arrival rates, but also have minimum variation in shutdowns, short and consistent change over times, and minimal variations in process times, among other things.
In Factory Physics by Hopp and Spearman, it states: “The single most neglected factor in capacity analysis, as it is practiced in American industry today, is variability.”
This is true. But I also say that in this industry, the single most important factor that almost every PCB factory misses is optimizing their production schedule to minimize DAM variation. We will talk about this another time, but the main point is that you want to schedule not only to a due date, but also focus on minimizing changeovers, minimizing variation in process times, minimizing arrival rates and so on. And you want to schedule downtime for repair and maintenance of equipment to a precise metronome beat.
Before we end this important topic about running your operation like a Swiss watch, I have this really thick book on my desk called The Toyota Culture: The Heart and Soul of the Toyota Way, by Jeffrey Liker and Michael Hoseus. This is an opus at 562 pages. Despite all of the good things people say about this book and the others in the series, I can’t recommend them, because when I read them I walk away confused. In order for things to stick for me, I need simple ideas I can connect with. One of those connecting ideas in TPS is about eliminating DAM variation--variation that impedes flow. Another connecting idea is that the Toyota Culture is nothing more than people knowing exactly what the right things to do are and doing them, which results in the company winning. It’s when people are confused about what to do, there are mixed messages all over the place, and everyone is frustrated, that a company loses.
It’s all about removing DAM variation. If you do that, you win. Simple.
Gray McQuarrie is president of Grayrock & Associates, a team of experts dedicated to building collaborative team environments that make companies maximally effective. McQuarrie is the primary inventor of the patent, Compensation Model and Registration Simulation Apparatus for Manufacturing PCBs. He has worked for AlliedSignal, Shipley, Photocircuits, Monsanto and others. Contact McQuarrie at gray@grayrock.net.
More Columns from Solving DAM Problems
Solving DAM Problems: Solving a True DAM ProblemSolving Dam Problems: Why Removing Your Bottleneck is a Bad Idea
Change Your DAM Thinking: Do We Need to be More Innovative?
Solving DAM Problems: Can Scrap be Beaten? A Strategy for 2014 and Beyond
Solving Dam Problems: How to Compute Your Plant's DAM Capacity
Solving DAM Problems: Standards are DAM Important!
Solving DAM Problems: What's the DAM Problem with Scheduling?
Solving Your DAM Problems: Examine Your DAM WIP