-
- News
- Books
Featured Books
- pcb007 Magazine
Latest Issues
Current IssueThe Hole Truth: Via Integrity in an HDI World
From the drilled hole to registration across multiple sequential lamination cycles, to the quality of your copper plating, via reliability in an HDI world is becoming an ever-greater challenge. This month we look at “The Hole Truth,” from creating the “perfect” via to how you can assure via quality and reliability, the first time, every time.
In Pursuit of Perfection: Defect Reduction
For bare PCB board fabrication, defect reduction is a critical aspect of a company's bottom line profitability. In this issue, we examine how imaging, etching, and plating processes can provide information and insight into reducing defects and increasing yields.
Voices of the Industry
We take the pulse of the PCB industry by sharing insights from leading fabricators and suppliers in this month's issue. We've gathered their thoughts on the new U.S. administration, spending, the war in Ukraine, and their most pressing needs. It’s an eye-opening and enlightening look behind the curtain.
- Articles
- Columns
- Links
- Media kit
||| MENU - pcb007 Magazine
Estimated reading time: 10 minutes
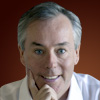
Solving Your DAM Problems: Little Things Have the Power to Break Big DAMs
Editor's Note: This article originally appeared in the September 2012 issue of The PCB Magazine.
In my book, Change Your DAM Thinking, I describe how Glenn Canyon Dam was nearly destroyed by microscopic cavitation bubbles. A simplistic explanation of what the engineers had done wrong was twofold. First, they looked at the likelihood of an average event, such as a very large water flow coming into Lake Powell, and decided that it wouldn’t happen in their lifetime. They were wrong to focus their attention on an average event and should have focused on the contingency planning surrounding the unlikely event. Second, they thought that really large structures of an immense scale were strong and invulnerable to tiny things, like microscopic cavitation bubbles. Again, they were wrong. So wrong, in fact, that they had a crisis on their hands in less than two years after Lake Powell had reached its anticipated ideal water mark (it took about 20 years for the water to build behind the dam).
How far do any of us have to think back to an unlikely event, the thing that wasn’t supposed to happen, that nearly wiped us out? Think of the global economic crisis. How often have we underestimated the impact of a seemingly inconsequential event such as an insignificant late order? If that one late order were placed by a customer who was counting on you to supply product for their major product launch, or that one late order happened when you were trying to get qualified by a major OEM, then your average on-time delivery for the plant is absolutely meaningless. If we are going to be able to identify the true game-changers for our business and take advantage of them, we have to change our DAM thinking and appreciate the power of small things that can change our lives for the better.
A nightmarish DAM problem for our industry is metal finishing, be it ENIG, solder, tin, silver, HASL, OSP, etc… In fact, a great article explaining these coatings and illustrating the scenario is Marissa Oskarsen’s “What is Your PCB IQ? – PCB Final Finishes.”
Our ability to perform metal finishing reliably has become challenging due to RoHS compliancy regulations. When we use a lead-free solder, we are forced to go as high as 260˚C, which means we need a high-performance Tg laminate that is more expensive then the standard laminate that use to work. If we use silver, we have to worry about creep corrosion. If we use LF HASL, we have to worry even more about wetting. If we use immersion tin, we have to worry about whiskers. If we use ENIG, we have to worry about a bunch of BGAs falling off the board and getting hit with valued-added claims because of a black-pad issue we couldn’t measure, predict, or know about until it was too late. And if we use ENEPIG, well, we discover that the more layers we put down, the more strange and unexpected things that can happen, as described in this article by Hitachi Chemical.
What is a better answer to this insanity? The use of the very small: the nanometer-scale coating.
A nanometer is one billionth of a meter. The diameter of a golf ball is 42.67 million nanometers. The smallest thing the human eye can detect is 0.1 mm or 100,000 nanometers. A single skin cell is 30,000 nm and humans can’t see it without a microscope. An E. coli bacterium is about 600 nm long and we can see this with a high-power light microscope. Visible light microscopes are limited by the wave-length of light, which is about 500 nm. An HIV virus is 130 nm, a hepatitis virus is 45 nm, a ribosome is 30 nm, and hemoglobin is 6.5 nm; humans need sophisticated electron microscopes to see things this small. Equipment exists that can coat printed circuit boards with a 60 nm protective layer. Why on earth would we want to do that? How could something so thin and tiny do anything for us? (If you are thinking like that, then you will suffer the same career-damaging fate as the design engineers at Glenn Canyon Dam.)
A great example of how this seemingly insignificant, invisibly-thin coating completely changes the game is by virtually eliminating creep corrosion! It’s a problem with almost any type of metal finish, but it is most apparent with the use of immersion silver. Silver has great solderability properties, but it is affected by tarnishing and is very susceptible to creep corrosion, a serious problem because it induces shorts and opens well after final assembly, leading to the potential of value add claims from your customer.
Possibilities also arise for bonding copper wire to copper pads on the board. This would eliminate several things: the cost of the gold pad and the gold wire; the worry about scrap caused by incorrect gold thickness; and/or a scratch on a wire bond pad, due to a handling mishap. Moreover, a copper-to-copper bond reduces impedance-matching effects, rendering cleaner signals, and possibly reducing power requirements because of the improved efficiency. This results in a lower-cost product that is easier to make, and has better final performance. Companies like Amkor seem to be working in this direction, and an IEEE article about fine pitch wire bonding on copper pad can be found here.
Certain nano-coatings available today, like those from Semblant, don’t require a masking, because you can wire bond or solder right through it. When we engineer by adding steps, by adding layers of metal, by adding overall complexity, we reduce the reliability, quality, and performance of a product. These added complex steps, which are challenging to control and manage at the end of the process, make our business very unpredictable. We can have a total loss of a job happen at just the wrong time, which can do financial damage many times greater than the cost of remaking the lot. I have been witness to this very event where a medium-sized shop lost an opportunity to be a supplier to a very large medical device OEM, because the roll of the dice on their metal finishing turned up deuces, meaning they “crapped out,” to use a gambling term.
So what is the problem with using this new technology? It isn’t free! This means we have to get it past our accounting department, which is fixated on ROI. Sure, we may have budgeted capital expenditures, but accounting is the gatekeeper. In order to get past the gatekeeper, the new technology has to generate enough money so that it matches or exceeds the ROI target. The first thing to look at is the cost of gold, which is expensive. In the last five years, gold has been as low as $650 an ounce, and as high as $1,800 an ounce, approximately. Consider an 18” x 24” panel with 1 um thickness (0.0001 cm) for gold, where there are 80 circuits on a panel with 20 gold pads per circuit with dimensions of 60 mils (0.1524 cm) by 20 mils (0.0508 cm). Using the density of gold at 19.32 g/cm^3, we would have 0.012 grams of gold over the board, or 0.000423 of an ounce. At the time I wrote this article, the price of gold was at $1,617/oz., which amounts to $1.36 per board. If you are building 1,000 boards a week for one year, $70,720 a year could be eliminated if you didn’t need a gold finish. Many of us have CFOs who want a much stronger case than this.
Where would more monetary value come from that could help us build a stronger ROI justification for this new technology? My DAM Scrap column (August 2012) might offer a hint. Scrap kills capacity in the form of restarts. For example, a 20% scrap rate will reduce your available capacity by 25%, because 5% of restarts will be restarted at least one more time. Moreover, in an era where we need premium quick-turn jobs, the scrap rate can have a devastating effect on profits. An improvement of as much as 10% in scrap can have the same economic impact as having your shop located in China, with one tenth of the labor rate. When you add up all of the scrap costs caused by metal finishing it can be as high as 5%, 10% or more. Scrap isn’t just a cost, but it is also a constraint on your plant’s capacity. Significant improvements to scrap need to be understood as a strategic issue with regard to how best to deploy the new capacity for maximizing profit. For example, if there is an 11% improvement in capacity from using a nanometer-scale technology process and you can generate 5% more quick-turn jobs with a high average price per panel, the ROI can be very high.
Here is something else that doesn’t show up on the ROI computation, but it speaks to that one time event that can have devastating consequences to your business, all because of poor timing. Figure 1 shows a discrete event model for a simple (supplier plant/customer plant) supply chain.
Figure 1: The discrete event model for the simple supplier/customer supply chain.
We will be discussing this model in greater detail in next month’s column. For now, a customer decides on the reorder point (ROP) and economic order quantity (EOQ) that will minimize costs and keep its plant building the product they need to sell. Figure 2 shows the inventory fluctuation that you would see for optimized values that were determined for no scrap in the supplier plant. In order to get these results the ROP was 8 and the EOQ was 12.
Figure 2: The typical saw pattern using the optimal settings for the reorder point (ROP) and the economic order quantity (EOQ) derived from the discrete event model.
For a 10% scrap rate at the supplier, where boards are scrapped out at the end of the process, as you would find with gold or any metal finishing operation, you have to restart at the beginning. This inefficiency causes ROP to be 11 and the EOQ to be 14. Figure 3 shows a typical safe result where the maximum inventory was found to be 18 and the days down was 0. The maximum inventory for the no scrap case was 14.
Figure 3: A somewhat unstable saw pattern due to the scrap happening in the supplier plant, resulting in a higher ROP and EOQ, as well as a higher average inventory and maximum inventory.
This may not seem like a great concern, until you consider what the worst-case scenario might be. Figure 4 shows the worst case from 500 runs at the optimum settings for 10% scrap.
Figure 4: Even with the optimum ROP and EOQ derived in the model, you can have worst-case scenarios that cause your customer to be down for days. What is the cost to your business when these worst-case scenarios happen?
For this run, there were a total of 16 days of insufficient inventory, where the customer was shut down! One of these periods of shutdown, which happened just after 75 days, was for seven days straight. True, this was an unlikely outcome, one out of 500 (we will get in a deeper dive with this model in the next article about risk), but the important point is that it did happen! Just like the larger than expected water flow into Lake Powell, which was a low-probability event, it did happen. What are you going to tell your customer when their process has been shut down because of issues with restarts and scrap in your factory? That you filled out a SCAR and reprimanded the responsible operator and it will never happen again? A lie? Will you say that this is a random occurrence and it will happen again and you don’t know when? The truth?
It is a no-win situation for everyone. A possible win/win would be to tell your customer that you are fundamentally changing your metal finishing process, which will drastically reduce the probability of this happening again and provide a huge improvement in your ability to supply your customer consistently.
Gray McQuarrie is president of Grayrock & Associates, a team of experts dedicated to building collaborative team environments that make companies maximally effective. McQuarrie is the primary inventor of the patent, Compensation Model and Registration Simulation Apparatus for Manufacturing PCBs. He has worked for AlliedSignal, Shipley, Photocircuits, Monsanto and others. Contact McQuarrie at gray@grayrock.net.
More Columns from Solving DAM Problems
Solving DAM Problems: Solving a True DAM ProblemSolving Dam Problems: Why Removing Your Bottleneck is a Bad Idea
Change Your DAM Thinking: Do We Need to be More Innovative?
Solving DAM Problems: Can Scrap be Beaten? A Strategy for 2014 and Beyond
Solving Dam Problems: How to Compute Your Plant's DAM Capacity
Solving DAM Problems: Standards are DAM Important!
Solving DAM Problems: What's the DAM Problem with Scheduling?
Solving Your DAM Problems: Examine Your DAM WIP