-
- News
- Books
Featured Books
- pcb007 Magazine
Latest Issues
Current IssueThe Hole Truth: Via Integrity in an HDI World
From the drilled hole to registration across multiple sequential lamination cycles, to the quality of your copper plating, via reliability in an HDI world is becoming an ever-greater challenge. This month we look at “The Hole Truth,” from creating the “perfect” via to how you can assure via quality and reliability, the first time, every time.
In Pursuit of Perfection: Defect Reduction
For bare PCB board fabrication, defect reduction is a critical aspect of a company's bottom line profitability. In this issue, we examine how imaging, etching, and plating processes can provide information and insight into reducing defects and increasing yields.
Voices of the Industry
We take the pulse of the PCB industry by sharing insights from leading fabricators and suppliers in this month's issue. We've gathered their thoughts on the new U.S. administration, spending, the war in Ukraine, and their most pressing needs. It’s an eye-opening and enlightening look behind the curtain.
- Articles
- Columns
- Links
- Media kit
||| MENU - pcb007 Magazine
Estimated reading time: 8 minutes
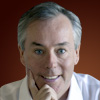
Solve Your DAM Problems: No DAM Extras…Like, Ever!
Editor’s Note: This article originally appeared in the October 2012 issue of The PCB Magazine.
You have two choices regarding how you manage scrap events in your shop; your choice could be the difference between your business thriving or dying. The most popular option for managing scrap events is to start extra material so that you have enough to ship at the end, but this option can drive your business into the ground.
The least popular option is to restart jobs in which you start absolute-lot quantities--no extras--but this requires disciplined execution and a tightly timed and reliable production process. This option could make your operation extremely profitable--if you can do it. Let’s explore what it would take to make this work.
Figure 1 shows the simple discrete event model we used in last month’s article, Little Things Have the Power to Break Big DAMs,showing a result of 16 days down with 10% scrap in the supplier process. In this model we are the supplier and we don’t want to cause our customer to keep too much inventory, but we also don’t want them to have such a low inventory that they run out of parts. Our goal is to come up with the optimum order quantity (EOQ) and optimum reorder point (ROP) that keeps our customers’ costs at a minimum.
Figure 1: Simple discrete event supplier/customer model.
The optimum shown in Figure 1 was derived using the objective function in Equation 1 that includes shutdown costs, inventory holding costs, and shipping costs.
The result in Figure 1 happened using an optimum ROP and EOQ derived from the model! What went wrong? To answer this we need to look at our supplier plant more closely.
Figure 2 shows a simple block diagram pictorial of our plant where all of our operations have been reduced to a simple conveyor that provides surprisingly detailed insights. For example, in a conveyor process activity, items exit in a precise timed sequence or spacing. This mimics the delay caused by electrical test, which is an important part of detecting a scrap event, because it will trigger the need for a restart using our no extras policy.
Figure 2: Restart loop caused by scrapped panels occurring in the supplier factory.
Table 1 shows the result of the model, where the time it takes for one panel to travel the conveyor is five days with panels spaced or delayed by half a day. This data represent one simulation run of 300 days repeated 500 times.
Table 1: Data showing the lack of correlation between number of restarts at the supplier and days down because of lack of material at the customer.
What is astonishing about Table 1 is that the customer’s number of days down was as high as 15. How can this happen?
The answer rests with the behavior of the conveyor. If you had a lot size or EOQ of four items, it would take 6.5 days to complete the lot: part 1 = day 5, part 2 = day 5.5, part 3 = day 6, part 4 = day 6.5. You can see that multiple restarts, with larger lot sizes or a larger EOQ, increase the spread in the time to complete a lot. Notice that in Table 1 there is a wide range of number of restarts or scrap events for zero days down at our customer. In fact, there is no numerical correlation to the number of scrap events and days down at the customer!
To make this idea easier to understand, think of a scrap event as a number of turns at a roulette wheel. You don’t know what number the ball is going to land on that will tell you when you will detect the event. As you play more times you are going to get a wider range of results. It’s the position on the conveyor that triggers when the restart will happen; when this happens determines how long it will take to complete the lot.
As it stands, even at the optimized levels for ROP and EOQ, you will be so late with deliveries that 40% of the time your customer will run out of material. You will be lucky to keep the business for this level of performance. There will be an enormous incentive to abandon this approach and just launch extras. Don’t do it!
In my October 2011 column, “Don’t Shoot the Messenger: Make Your Quality Meetings Fun,” we saw how the variation in scrap (and this was real data, by the way) can vary greatly between part numbers. What this means is that in order to ensure that you have sufficient material to prevent the need for the restart you will have to release extras in excess of the average scrap rate of 10%. To understand this, ask yourself this question: How often on a given day is the temperature below average and above average? About 50% of the time you will have processed too much material and about 50% of the time you will have processed too little material. This isn’t good, because it is the absolute singular result repeated again and again that a customer cares about--not the average event. In order to improve your 50% result of having enough material to ship, you will have to start a huge amount of excess material. The over-processing will cause your costs to skyrocket. A shop that understands this fact and does just the opposite--a no extras policy--has the opportunity to compete on cost with any shop in the world.
So what can you do to improve the risk issue seen in Table 1? What if we kept the conveyor going at the same speed (five days for a panel to go from beginning to end), but decreased the spacing from one-half a day or 12 hours, to 0.1 days or 2.4 hours while keeping the ROP and EOQ levels the same? Table 2 shows the results.
Table 2
Table 2: Data showing the benefit of reducing the wait time between panels, or spacing of panels, on the production conveyor.
The improvement in Table 2 shows what can happen by decreasing the spacing or delay between parts. What this means in a board shop is that you want the electrical test, final routing, and final inspection to go as fast as possible. When a scrap event is detected, immediately launch a restart. This may mean doing things differently than what you do today. Here are some recommendations to consider:
1) Instead of doing ET after final routing, you might want to do ET before final routing so that you can launch a restart panel as soon as possible.
2) If you do the above, then you will have to ET the panel instead of the individual circuits.
3) There might be issues of equipment cost and testing cost for a given panel size if you are going to test panels and not parts. And there may have to be a rethinking as to the optimum number of different panel sizes, and the size of panels themselves.
4) As soon as you detect a single bad circuit in a panel, you need to relaunch a panel. You might want to relaunch a second panel prior to getting enough circuits to justify a second panel restart.
5) Avoid jobs that have extremely advanced final routings that take a very long time. Work with the customer to use a different process and technology or redesign the board or make sure pricing reflects the added cost presented from the constrained product flow created by the part. Also make it clear that delivery schedules will be erratic and you will not accept penalties for being late. Each intricate route will have to be examined, likely using an advanced optical tester of limited capacity, and inspected carefully by hand. This is going to produce a significant panel-to-panel spacing or delay for detecting a scrap event.
6) Make sure the final inspection process is streamlined, operators are well trained, and that it has adequate optimized man power so that you keep any delay in detecting scrap events as short as possible, and costs in line.
7) Train process operators to look for the same things people are looking for in final inspection. Have operators report out the scrap they see and launch an appropriate restart. This should reduce the need for inspectors at the end of the process.
8) Never punish people on the floor for scrap, because you will not get the information you need for a no extras policy to work. Initiate a process for review and retrain operators as required. Remove operators based on inspection of how they are doing their work on the job, but never for a specific event that happens on the line. If you get just this part right, forgetting everything else, your shop will make dramatic improvements (this will be a subject of a future article).
9) Figure out how ET, final routing, and final inspection can become a work cell that is fast and efficient with minimal delays and everyone working as a team.
10) Determine the number of ET testers you need to keep the detection of scrap at the speed you need.
Just because all of the real processing work has been done, you aren’t home free. There are huge benefits for you and your customer to make the final operations of ET, final routing, and final inspection coordinated and fast. The benefits are huge to you and your customer. By doing it well, you will have a consistency of delivery to your customers that will be very difficult for your competitors to match.
Gray McQuarrie is president of Grayrock & Associates, a team of experts dedicated to building collaborative team environments that make companies maximally effective. McQuarrie is the primary inventor of the patent, Compensation Model, and Registration Simulation Apparatus for Manufacturing PCBs. He has worked for AlliedSignal, Shipley, Photocircuits, Monsanto, and others. Contact McQuarrie.
More Columns from Solving DAM Problems
Solving DAM Problems: Solving a True DAM ProblemSolving Dam Problems: Why Removing Your Bottleneck is a Bad Idea
Change Your DAM Thinking: Do We Need to be More Innovative?
Solving DAM Problems: Can Scrap be Beaten? A Strategy for 2014 and Beyond
Solving Dam Problems: How to Compute Your Plant's DAM Capacity
Solving DAM Problems: Standards are DAM Important!
Solving DAM Problems: What's the DAM Problem with Scheduling?
Solving Your DAM Problems: Examine Your DAM WIP