-
- News
- Books
Featured Books
- pcb007 Magazine
Latest Issues
Current IssueInventing the Future with SEL
Two years after launching its state-of-the-art PCB facility, SEL shares lessons in vision, execution, and innovation, plus insights from industry icons and technology leaders shaping the future of PCB fabrication.
Sales: From Pitch to PO
From the first cold call to finally receiving that first purchase order, the July PCB007 Magazine breaks down some critical parts of the sales stack. To up your sales game, read on!
The Hole Truth: Via Integrity in an HDI World
From the drilled hole to registration across multiple sequential lamination cycles, to the quality of your copper plating, via reliability in an HDI world is becoming an ever-greater challenge. This month we look at “The Hole Truth,” from creating the “perfect” via to how you can assure via quality and reliability, the first time, every time.
- Articles
- Columns
- Links
- Media kit
||| MENU - pcb007 Magazine
Estimated reading time: 1 minute
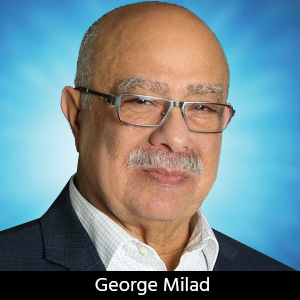
The Plating Forum: ENIG and the Plating Process
Electroless nickel immersion gold (ENIG) continues to gain market share due to its versatility in a wide range of component assembly methods including solder fusing, wave soldering, and wire bonding. The ENIG finish provides a highly solderable flat surface that does not tarnish or discolor. It has a long shelf life and the precious metal topcoat provides excellent electrical continuity. The nickel serves as a barrier against copper diffusion and prevents copper contamination of the solder during wave soldering and rework operations.
The ENIG Plating Process
The plating of ENIG is a complex multi-step process. Each process step is carefully designed and must be well understood and controlled to produce the desired end product.
These can be broken down into the following:
- Preparing the catalyzed surface for Ni deposition
- The Ni deposition step
- The gold deposition step
1. Preparing the Catalyzed Surface for Ni Deposition
The objective is to form a thin immersion uniformly distributed palladium catalyst layer on the copper surfaces to be plated with nickel. Nickel deposition is specific to the catalyzed surface. Nickel will not initiate or deposit on non-catalyzed surfaces like soldermask or laminate. The uniformity is important so that the nickel will initiate at the same time on all areas of the copper surfaces to be plated. This will give rise to an even nickel deposit with no crevices or protrusions in the final plating. An even nickel deposit is not susceptible to corrosion during the gold deposition step.
Achieving a uniformly catalyzed surface begins with bringing a pristine copper surface to the catalyst bath. A pristine copper surface is one that is free of oxidation, organic contaminants, neutral (charge-free) and fairly smooth (low profile). Read the full column here.
Editor's Note: This column originally appeared in the December 2013 issue of The PCB Magazine under George's "The Finish Line" column.
More Columns from The Plating Forum
The Plating Forum: Reduction Assisted Immersion Gold for ENEPIG Surface FinishThe Plating Forum: Surface Finish Evolution from Conventional to Advanced
The Plating Forum: Plating in Electronic Applications
The Plating Forum: How the Pandemic Impacted PCB Manufacturing
The Plating Forum: The Significance of IPC ENIG Specification 4552 Revision B
The Plating Forum: The IPC Surface Finish Specifications
The Plating Forum: An Overview of Surface Finishes
The Plating Forum: DIG—The Next Generation