-
- News
- Books
Featured Books
- pcb007 Magazine
Latest Issues
Current IssueThe Hole Truth: Via Integrity in an HDI World
From the drilled hole to registration across multiple sequential lamination cycles, to the quality of your copper plating, via reliability in an HDI world is becoming an ever-greater challenge. This month we look at “The Hole Truth,” from creating the “perfect” via to how you can assure via quality and reliability, the first time, every time.
In Pursuit of Perfection: Defect Reduction
For bare PCB board fabrication, defect reduction is a critical aspect of a company's bottom line profitability. In this issue, we examine how imaging, etching, and plating processes can provide information and insight into reducing defects and increasing yields.
Voices of the Industry
We take the pulse of the PCB industry by sharing insights from leading fabricators and suppliers in this month's issue. We've gathered their thoughts on the new U.S. administration, spending, the war in Ukraine, and their most pressing needs. It’s an eye-opening and enlightening look behind the curtain.
- Articles
- Columns
- Links
- Media kit
||| MENU - pcb007 Magazine
Estimated reading time: 1 minute
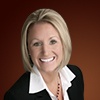
The Short Scoop: Stencil Printing in PCB Cavities
December’s Short Scoop presented results from the first part of a study to determine if a 3D electroform stencil, in just one printing step, could be used to print both levels of a two-level board with cavities. The study explored two different printing modes: step print and reservoir. In the first part we examined the step mode. The results confirmed that a 3D electroform single thickness stencil could indeed print solder paste for a .3 μm μBGA with pads on two levels of the PCB separated by 7 mils (175 μm). It also showed that the squeegee blade used in the printer makes a significant difference in the application of the solder paste and the results obtained.
Here we explore whether a single-thickness electroform stencil can print flux or solder paste into a recessed area on a PCB for an embedded flipchip with a cavity depth of 14 mils (350 μm), which is becoming a requirement for many components.
Normally, to print on both levels requires special stencil and squeegee blade designs. A two-step stencil process is often used. We wanted to see if one stencil could be used instead. Using just one stencil to print both levels at the same time saves time, money, and resources.
Board, Stencil, and Squeegee Blade Set-Up To test whether we could print into a recessed area, a reservoir was created on the front side of a PCB by gluing a 356 μm (14 mil) thick shim on the flex circuit. Flip-chip pads were embedded in the cavity. The shim was pin registered to the flex and then glued in place.
For the stencil, we used a 2 mil (50 μm) thick 3D electroform stencil with a 14 mil (355 μm) deep pocket and apertures consisting of 10 mil (250 μm) circles.
The stencil was grown on a mandrel with pocket walls that were machined at 45°. The stencil had three separate flux reservoir cavities with different aperture sizes: zone 1 had 4 mil (100 μm) apertures, zone 2 had 4.5 mil (112 μm) apertures, and zone 3 had 5 mil (125 μm) apertures.
For reservoir printing, the squeegee blade of choice is either a contained head pump-print system or a pump-print rubber blade. Our tests tried a 90° rubber blade, a metal blade, and a pump-print rubber blade.
Editor's Note: This article originally appeared in the January 2015 issue of SMT Magazine.
More Columns from The Short Scoop
Adapting Stencils to Manufacturing Challenges in 2015The Short Scoop: Printing Two-level PCBs in One Step with a 3D Electroform Stencil
The Short Scoop: Improving Stencil Printing Results
The Short Scoop: More Stencil Questions (and the Answers!)
The Short Scoop: Selecting a Stencil Frame
The Short Scoop: Screen Printing Solutions for Small Die & Precision
The Short Scoop: 10 Common Stencil Questions
The Short Scoop: Electroformed Stencils