SJIT, Solder Joint Integrity Test, To Find Latent Defects in Printed Wiring Board Assembly
April 29, 2015 | Hiroshi Yamazaki, Hioki E.E. CorporationEstimated reading time: 5 minutes
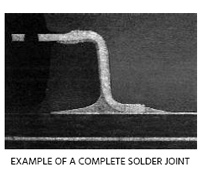
To find defects of solder joint in printed wiring board assembly, quite a few test methods have been developed so far. Capacitance method and IEEE 1149.1 or boundary scan method are often used to find opens between component leads and pads on a printed wiring board. These methods, however, can find complete opens or complete shorts only. Latent defects that can be complete defect after several years have not been found by the conversational method.
We have developed a method to find such latent defects by using 4-wire small resistance measurement technique and have built in a flying-probe in-circuit tester. It measures the resistance between component leads and pads, and checks the volume of the solder. Because the volume of the solder is inversely proportional to the resistance in-between, resistance measurement can be a way to test the solderability.
This technique is industry proven. A lot of manufacturing plants which produce printed board assembly used in automotive have adapted it. The printed wiring board assembly for automotive must endure vibration. Thus if a board assembly has a latent defect, it can bring a serious accident. In my presentation, I would like to introduce the importance of SJIT, Solder Joint Integrity Test, and a technique of SJIT.
Testing Printed Wiring Board Assembly
Printed wiring board assemblies, PWBA, are tested several times after production.The tests are categorized as production test, board-level test and system test.[1]Usually, automatic optical inspection, AOI, is done in process of production and used to not only checks component placements but also monitor the yield of the production.
The Board-level test stage follows in-process inspection at the production stage. In this stage, board assemblies are tested structurally first. Either in-circuit test or boundary-scan method or sometimes both of them are used for structural tests. The structural test, especially in-circuit test, has another purpose. It works as a pre-check for next functional test. In the functional test, power sources should be applied to the board assembly to be tested. Thus if the board assembly is not structurally complete, it can be damaged while the functional test.
The board-level structural test is done, functional tests of board-level and system-level follows.
Carrying out all the tests makes test cost increments. Thus in some cases, board-level tests are skipped and only system test is done. Moreover, in an extreme case, manufacturers do not test their products at all.
Omission of test items should be done as carefully as possible, however. It can be rebounded as a massive cost increment. Assume board-level tests including structural test and functional test are not done, and a defect is found afterwards.
Repair cost will be enormously increases as the production/test stage reaches the shipment. It is called"The 10X rule in PWBA tests."[2]
If a product including a defect comes out to the market, the problem will be much more serious.Think about the case of a car with a defective PWBA. The malfunction of the PWBA may relate to a car accident and give the driver injury. Once a defective PWBA is distributed in the market, its recall cost can be 100000X or much more.
Everyone wants to make test cost as low as possible, but as stated above, the loss will increase if test strategy is wrong. To determine test strategy, the following two factors should be considered.
1. Quality
Required degree of test quality largely depends on the quality that the products needs. A cheap complimentary toy for example does not need board-level test. If it does not work at the system level functional test, it may be thrown away.
2. Volume
How many the products is produced is another important factor to determine test strategy. For small volume production, tester may not be required, but for high volume manufacturing a dedicated tester and jigs may be required otherwise the test process can be a bottleneck.Page 1 of 2
Testimonial
"Advertising in PCB007 Magazine has been a great way to showcase our bare board testers to the right audience. The I-Connect007 team makes the process smooth and professional. We’re proud to be featured in such a trusted publication."
Klaus Koziol - atgSuggested Items
Indium Corporation Promotes Two Leaders in EMEA (Europe, Middle East, and Africa) Markets
08/05/2025 | Indium CorporationWith its commitment to innovation and growth through employee development, Indium Corporation today announced the promotions of Andy Seager to Associate Director, Continental Sales (EMEA), and Karthik Vijay to Senior Technical Manager (EMEA). These advancements reflect their contributions to the company’s continued innovative efforts with customers across Europe, the Middle East, and Africa (EMEA).
MacDermid Alpha Electronics Solutions Unveils Unified Global Website to Deepen Customer, Talent, and Stakeholder Engagement
07/31/2025 | MacDermid Alpha Electronics SolutionsMacDermid Alpha Electronics Solutions, the electronics business of Elements Solutions Inc, today launched macdermidalpha.com - a unified global website built to deepen digital engagement. The launch marks a significant milestone in the business’ ongoing commitment to delivering more meaningful, interactive, and impactful experiences for its customers, talent, and stakeholders worldwide.
KOKI to Showcase Analytical Services and New HF1200 Solder Paste at SMTA Guadalajara 2025
07/31/2025 | KOKIKOKI, a global leader in advanced soldering materials and process optimization services, will exhibit at the SMTA Guadalajara Expo & Tech Forum, taking place September 17 & 18, 2025 at Expo Guadalajara, Salón Jalisco Halls D & E in Guadalajara, Mexico.
Weller Tools Supports Future Talent with Exclusive Donation to SMTA Michigan Student Soldering Competition
07/23/2025 | Weller ToolsWeller Tools, the industry leader in hand soldering solutions, is proud to announce its support of the upcoming SMTA Michigan Expo & Tech Forum by donating a limited-edition 80th Anniversary Black Soldering Set to the event’s student soldering competition.
Koh Young Appoints Tom Hattori as President of Koh Young Japan
07/21/2025 | Koh YoungKoh Young Technology, the global leader in True 3D measurement-based inspection solutions, announced the appointment of Tom Hattori as President of Koh Young Japan (JKY).