-
- News
- Books
Featured Books
- pcb007 Magazine
Latest Issues
Current IssueThe Hole Truth: Via Integrity in an HDI World
From the drilled hole to registration across multiple sequential lamination cycles, to the quality of your copper plating, via reliability in an HDI world is becoming an ever-greater challenge. This month we look at “The Hole Truth,” from creating the “perfect” via to how you can assure via quality and reliability, the first time, every time.
In Pursuit of Perfection: Defect Reduction
For bare PCB board fabrication, defect reduction is a critical aspect of a company's bottom line profitability. In this issue, we examine how imaging, etching, and plating processes can provide information and insight into reducing defects and increasing yields.
Voices of the Industry
We take the pulse of the PCB industry by sharing insights from leading fabricators and suppliers in this month's issue. We've gathered their thoughts on the new U.S. administration, spending, the war in Ukraine, and their most pressing needs. It’s an eye-opening and enlightening look behind the curtain.
- Articles
- Columns
- Links
- Media kit
||| MENU - pcb007 Magazine
Estimated reading time: 1 minute
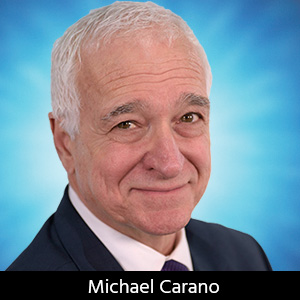
Contact Columnist Form
Copper Discoloration and Other Concerns with OSP
Yes, it is about process. And that includes equipment operating parameters as well as chemistry. Getting the OSP process to perform as it is intended requires attention to both. This month's "Trouble in Your Tank" delves into one of the most irritating issues with respect to OSP: discoloration (read "oxidation") on critical circuit features. Why did this occur? Is there more than one cause? Will solderability be compromised? These are just a few of the questions raised when such a situation occurs. An example of this occurrence is shown in Figure 1.
Discoloration and even oxidation of the copper may occur for one of several reasons. Some of those listed may be more or less obvious than the others (Table 1). Some of these causes can be both equipment and chemistry related.
Figure 2 shows another example of discoloration on the copper pad most likely related to oxidation of the underlying copper. Further analysis of this situation pointed to two possible causes. The first was very low thickness of the OSP coating. In this case the thickness was less than the minimum recommended by the supplier (measured OSP thickness 0.08 micron versus recommended 0.20–0.25 micron). Certainly, the low thickness is cause for concern. With such a low thickness, the OSP would not effectively protect the copper from oxidation. However, what other process variations could be the cause for the low thickness? One possibility is the micro-etch step. It has been stated in the literature that a clean active copper surface is necessary in order to allow for a more uniform deposit of the OSP film. In addition, one should avoid an overly aggressive microetch as there are concerns about insufficient thickness of the organic film in deep crevasses.
Surface roughness does have an impact on OSP film thickness and is directly connected to solderability.
Editor's Note: This article originally appeared in the April issue of The PCB Magazine.
More Columns from Trouble in Your Tank
Trouble in Your Tank: Yield Improvement and ReliabilityTrouble in Your Tank: Causes of Plating Voids, Pre-electroless Copper
Trouble in Your Tank: Organic Addition Agents in Electrolytic Copper Plating
Trouble in Your Tank: Interconnect Defect—The Three Degrees of Separation
Trouble in Your Tank: Things You Can Do for Better Wet Process Control
Trouble in Your Tank: Processes to Support IC Substrates and Advanced Packaging, Part 5
Trouble in Your Tank: Materials for PWB Fabrication—Drillability and Metallization
Trouble in Your Tank: Supporting IC Substrates and Advanced Packaging, Part 5