-
- News
- Books
Featured Books
- smt007 Magazine
Latest Issues
Current IssueIntelligent Test and Inspection
Are you ready to explore the cutting-edge advancements shaping the electronics manufacturing industry? The May 2025 issue of SMT007 Magazine is packed with insights, innovations, and expert perspectives that you won’t want to miss.
Do You Have X-ray Vision?
Has X-ray’s time finally come in electronics manufacturing? Join us in this issue of SMT007 Magazine, where we answer this question and others to bring more efficiency to your bottom line.
IPC APEX EXPO 2025: A Preview
It’s that time again. If you’re going to Anaheim for IPC APEX EXPO 2025, we’ll see you there. In the meantime, consider this issue of SMT007 Magazine to be your golden ticket to planning the show.
- Articles
- Columns
Search Console
- Links
- Media kit
||| MENU - smt007 Magazine
Pad Cratering Susceptibility Testing with Acoustic Emission
July 22, 2015 | B.S. Wong and J. Silk, Keysight Technologies, and R. Nordstrom, Ph.D., Emerson Process ManagementEstimated reading time: 16 minutes
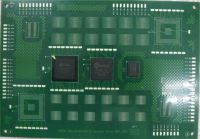
Abstract
Pad cratering test methods have been under development with the emergence of this laminate fracture defect mechanism. In additional to ball shear, ball pull, and pin pull testing methods, the acoustic emission method is being developed to evaluate laminate materials’ resistance to pad cratering. Though the acoustic emission (AE) method has been proven to be able to detect pad cratering, no study has reported which AE parameters are good indicators for the susceptibility of PCB laminates to pad cratering. In this study, six different laminates subjected to three different pre-conditioning (multiple reflow) cycles have undergone the four-point bend testing.
Four AE sensors were used to monitor pad cratering during the bend test. Several AE parameters including amplitude in dB level, the energy, and the location of each AE event under different load levels are recorded. Location analysis shows the majority of AE events are concentrated in the largest BGA package in the test vehicle, which indicates that pad cratering is elevated with the larger size of BGA package due to high stress concentration.
Both the number of AE events and the cumulative energy of AE events at a given applied load show that Laminate F is prone to pad cratering. However, there is no statistically significant difference in the lowest applied load to detectable AE among these six laminates. The ranking of the six laminate materials is different using different test methods. The most effective test method for predicting pad cratering susceptibility is inconclusive from this study.
Introduction
Pad cratering has become more prevalent with the switch to lead free solders and lead free compatible laminates. This mainly is due to the use of higher reflow temperature, stiffer Pb-free solder alloys, and the more brittle Pb-free compatible laminates. However, pad cratering is difficult to detect by monitoring electric resistance since pad cratering initiates before an electrical failure occurs.
Several methods have been developed to evaluate laminate materials’ resistance to pad cratering. Pad-solder level tests include ball shear, ball pull and pin pull [1-3]. The detailed methods for ball shear, ball pull, and pin pull testing are documented in an industry standard IPC-9708 [4]. Bansal, et al. [5-6] proposed to use acoustic emission (AE) sensors to detect pad cratering during four-point bend test. Currently there is an industry-working group working on test guidelines for acoustic emission measurement during mechanical testing [7].
The four-point bend test is one of several test methods used for evaluating the susceptibility of new PCB boards to pad cratering, where cohesive damage can accumulate in the laminate well before electrical failure is affected. The attributes of four point bend testing that differentiate it from other methods (such as drop tests, cold pull tests, etc.) include that 1) the four-point bend can be run over different strain rates, 2) all solder ball joints within the inner span are under the same uniform bend load, and 3) in-test monitoring methods, such as resistance failure and acoustic emission can be added to the test as additional evaluation methods. The rate of strain will change the failure location. At low strain rates, fractures occur in the solder joint. At high rates of strain, pad craters will occur at the highest strain points, typically the corner pads of a BGA. One can consider 1000 microstrains per second a ballpark for the transition, although this simple rule of thumb does not factor in variables affecting the transition.
Both metal and composites will emit transient elastic waves when undergoing localized stress release (i.e., damage); this phenomena being known as Acoustic Emission. In addition to detecting local emissions from single sensors, arrays of sensors can be used to obtain arrival time information from the AE event and locate the origin. It has been speculated that a solder ball failure will emit once, while laminates will generate 4 or more distinct emissions before failure, although this lacks a sufficient level of confirmation.
The goals of this investigation are to compare the susceptibility of various laminates to pad cratering. The results of six different laminates’ resistance to pad cratering using the ball pull, ball shear, and hot pin pull tests have been reported by authors in an earlier paper [8]. This paper presents the results of pad cratering susceptibility of laminates using the AE method under four-point bend and compares the AE results to the pad-solder level testing results.
Experiment
The laminate materials in this study are five Pb-free compatible high Tg laminates plus one dicy-cured non-Pb-free-compatible laminate. Laminate A is a high Tg un-filled dicy FR4, which is used as a control. Laminate B is a high Tg un-filled phenolic FR4; laminate C and laminate D are a high Tg filled phenolic FR4; laminate E is a high Tg filled mid-range-Df phenolic FR4, and laminate F is a high Tg un-filled mid-range-Df phenolic FR4.
The test coupon for this study is shown in Figure 1. The dimensions of the coupon are 7.2” (183mm) by 5” (127mm) with the PCB thickness of 0.059” (1.5mm). It is a 10-layer board with immersion silver surface finishing. Three daisy-chain BGA components assembled in the test vehicle are A-CABGA288-0.8mm-19mm-DC-LF305 (J3), A-PBGA324-1.0MM-23MM-DC-LF-305 (J4), and SDRAM DDR2 512M-bit 667MHz 1.8V 84-FBGA (U3). All test boards were pre-conditioned through a worst case scenario of Pb-free assembly environment, comprising 3, 5, or 7 reflow cycles @260°C peak for 10 seconds.
Bend testing was performed with uniaxial test machine with series controller. The four point bend fixtures were made of hardened steel. Rubbing on the rounded bend rollers was mitigated by use of thin non-slip adhesive tape that prevented direct contact of the steel fixtures with the composite board. The bend test details are shown in Table 1. The bend test setup is shown in Figure 2.
The tests in this study were done at a rate of 5,000 microstrains per second in order to achieve pad craters. This fast rate resulted in tests less than 2 seconds long, so a set level of deflection was used rather than terminating the test once activity is detected. Initial measurements of the printed circuit board without components were done to determine the basic fracture level of the board. Board deflection was recorded by crosshead displacement and translated to load. Initial tests were correlated to strain level, but strain was not measured on every sample.
Figure 1: Test coupon.
Page 1 of 5
Suggested Items
KYZEN to Focus on Aqueous Cleaning and Stencil Cleaning at SMTA Juarez
05/20/2025 | KYZEN'KYZEN, the global leader in innovative environmentally responsible cleaning chemistries, will exhibit at the SMTA Juarez Expo and Tech Forum, scheduled to take place Thursday, June 5 at the Injectronics Convention Center in Ciudad Jarez, Chihuahua.
Koh Young Installs 24,000th Inspection System at Top 20 EMS
05/14/2025 | Koh YoungKoh Young, the global leader in True 3D measurement-based inspection and metrology solutions, proudly announces the installation of its 24,000th inspection system at a Top 20 Global EMS in Thailand.
Indium’s Karthik Vijay to Present on Dual Alloy Solder Paste Systems at SMTA’s Electronics in Harsh Environments Conference
05/06/2025 | Indium CorporationIndium Corporation Technical Manager, Europe, Africa, and the Middle East Karthik Vijay will deliver a technical presentation on dual alloy solder paste systems at SMTA’s Electronics in Harsh Environments Conference, May 20-22 in Amsterdam, Netherlands.
SolderKing Achieves the Prestigious King’s Award for Enterprise in International Trade
05/06/2025 | SolderKingSolderKing Assembly Materials Ltd, a leading British manufacturer of high-performance soldering materials and consumables, has been honoured with a King’s Award for Enterprise, one of the UK’s most respected business honours.
Knocking Down the Bone Pile: Gold Mitigation for Class 2 Electronics
05/07/2025 | Nash Bell -- Column: Knocking Down the Bone PileIn electronic assemblies, the integrity of connections between components is paramount for ensuring reliability and performance. Gold embrittlement and dissolution are two critical phenomena that can compromise this integrity. Gold embrittlement occurs when gold diffuses into solder joints or alloys, resulting in mechanical brittleness and an increased susceptibility to cracking. Conversely, gold dissolution involves the melting away of gold into solder or metal matrices, potentially altering the electrical and mechanical properties of the joint.