-
- News
- Books
Featured Books
- design007 Magazine
Latest Issues
Current IssueAll About That Route
Most designers favor manual routing, but today's interactive autorouters may be changing designers' minds by allowing users more direct control. In this issue, our expert contributors discuss a variety of manual and autorouting strategies.
Creating the Ideal Data Package
Why is it so difficult to create the ideal data package? Many of these simple errors can be alleviated by paying attention to detail—and knowing what issues to look out for. So, this month, our experts weigh in on the best practices for creating the ideal design data package for your design.
Designing Through the Noise
Our experts discuss the constantly evolving world of RF design, including the many tradeoffs, material considerations, and design tips and techniques that designers and design engineers need to know to succeed in this high-frequency realm.
- Articles
- Columns
- Links
- Media kit
||| MENU - design007 Magazine
Material Witness: The Use of Fillers in Composites
August 3, 2015 | Chet GuilesEstimated reading time: 4 minutes
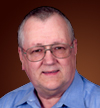
The use of finely divided ceramic fillers in composites intended for use in printed wiring boards has a long history, but most people still associate the idea with reducing the cost of the product by loading it with an inexpensive inert filler. Nothing could be further from the truth. The use of fillers provides the resin formulator with an opportunity to adjust and improve many of the important properties of a resin system. Just a few of the benefits of using a controlled level of micro-disperse ceramic additives include:
- Reduction of shrinkage of resin during cure
- Improvement of drilling quality
- Reduction in registration irregularity
- Increased thermal conductivity
- Improvement in coating quality
- Minimization of formation and propagation of cracks
- Reduction in overall Z-direction expansion
- Modification of electrical properties
Thermosetting resin systems such as those used in PWB laminates and prepregs tend to shrink volumetrically by as much as 4% on curing, due to the formation of regular structures and cross-links. In a laminate structure this creates some built-in stresses, as the shrinking resin is held in place by the glass reinforcement and by copper foil on the surface. When copper is subsequently etched away, the resin tends to relieve stresses to the extent that it can, resulting in some dimensional change in the material that can cause misregistration, warpage and other undesirable phenomena. The use of fillers can mitigate this post-etch shrinkage and make registration more controllable and predictable.
Talc has been used in PWB laminate systems since the 1950s to improve drilling quality, especially in older epoxy systems which have a tendency to smear when being drilled. The soft, platy talc both acts to lubricate at the drill cutting edge and to break up the chip from the material, reducing heat build-up and subsequent smearing. Other fillers also may improve drilling quality and reduce fracturing of the resin at drilled holes, reducing wicking and other anomalies that cause concern during wet process and plating.
Fillers may also be used to boost the thermal conductivity of a resin system. Fillers such as hydrated alumina and boron nitride have high thermal coefficients of heat transfer. Highly filled laminate composites can have Tc values as high as 1-2 W/m-K compared to 0.2- 0.3 W/m-K for unfilled glass-reinforced products.
Cracking of resin during drilling or handling can be significantly reduced by the dispersion of a finely divided filler in the resin system. A crack (which you can picture as a conic section “drilling” into the resin) develops extremes of force at the very tip; as the radius of the cone approaches zero, the force per unit area goes very high. Pressure = Force/Area. When area approaches zero as a limit, the pressure theoretically goes to infinity. What a filler does is to intercept the crack and dramatically increase the effective surface area, resulting in a reduced pressure and stopping the crack from propagating. Figure 1 illustrates this phenomenon.
In structural composites, crack propagation is often controlled by the inclusion of a discrete second phase in the system consisting of particles of a synthetic rubber such as Shell’s Kraton® which serve the same function as we achieve using ceramic fillers in PWB laminates and prepregs.
Crack initiation may be caused by drilling and handling. Radial cracking is often seen when drilling a large clearance hole in a resin-rich area, where resin shrinkage has created built-in stresses. In such cases the filler serves a dual purpose—both to reduce the shrinkage and to help eliminate the formation and propagation of cracks.
Opposite the shrinkage and related phenomena, fillers also tend to reduce the thermal expansion of the material. Most resins expand in the range of 40-50 ppm/oC, resulting in both in-plane and vertical expansion when a PWB is heated either in service or during processes such as solder leveling and reflow. Fillers reduce the resin expansion in all dimensions, but especially the Z-direction. When resins expand they do so isotropically unless restrained (the same in all directions) and are incompressible. The glass fabric in most laminates restrains the X-Y movement and so the resin moves in the Z-direction. That’s why most laminates have XY CTEs of 16-17 ppm/oC and Z-direction CTEs of 50-60 ppm/oC. Filled resins expand less and hence have reduced expansion in all directions.
Finally, we can consider the effect that fillers may have on electrical properties. Several considerations are important.
First, fillers have to be “clean” and free of ionic contaminants that might result in reduced ability to withstand voltage loading. Most laminate specifications want a minimum of 750 volts per mil of resistance to dielectric breakdown, and a “dirty” filler can reduce that substantially.
Second, fillers must have electrical properties that are desirable for the application. Commonly used is pure silica (SiO2) because it has a low dielectric constant as well as a low coefficient of thermal expansion. Combined with nonpolar resin systems, low controlled dielectric constants are possible in cost-effective systems for microwave and RF applications requiring Dk of 3.5 or less and loss values of 0.002-0.004.
The bottom line: Fillers are not simply dumped into a resin system to cheapen it, but they are usually engineered and tightly controlled to modify and improve specific properties that are of interest to the designer and user of PWBs.
For now, this is the Material Witness wishing you a happy summer.
Suggested Items
Driving Innovation: Direct Imaging vs. Conventional Exposure
07/01/2025 | Simon Khesin -- Column: Driving InnovationMy first camera used Kodak film. I even experimented with developing photos in the bathroom, though I usually dropped the film off at a Kodak center and received the prints two weeks later, only to discover that some images were out of focus or poorly framed. Today, every smartphone contains a high-quality camera capable of producing stunning images instantly.
Hands-On Demos Now Available for Apollo Seiko’s EF and AF Selective Soldering Lines
06/30/2025 | Apollo SeikoApollo Seiko, a leading innovator in soldering technology, is excited to spotlight its expanded lineup of EF and AF Series Selective Soldering Systems, now available for live demonstrations in its newly dedicated demo room.
Indium Corporation Expert to Present on Automotive and Industrial Solder Bonding Solutions at Global Electronics Association Workshop
06/26/2025 | IndiumIndium Corporation Principal Engineer, Advanced Materials, Andy Mackie, Ph.D., MSc, will deliver a technical presentation on innovative solder bonding solutions for automotive and industrial applications at the Global Electronics A
Fresh PCB Concepts: Assembly Challenges with Micro Components and Standard Solder Mask Practices
06/26/2025 | Team NCAB -- Column: Fresh PCB ConceptsMicro components have redefined what is possible in PCB design. With package sizes like 01005 and 0201 becoming more common in high-density layouts, designers are now expected to pack more performance into smaller spaces than ever before. While these advancements support miniaturization and functionality, they introduce new assembly challenges, particularly with traditional solder mask and legend application processes.
Knocking Down the Bone Pile: Tin Whisker Mitigation in Aerospace Applications, Part 3
06/25/2025 | Nash Bell -- Column: Knocking Down the Bone PileTin whiskers are slender, hair-like metallic growths that can develop on the surface of tin-plated electronic components. Typically measuring a few micrometers in diameter and growing several millimeters in length, they form through an electrochemical process influenced by environmental factors such as temperature variations, mechanical or compressive stress, and the aging of solder alloys.