-
- News
- Books
Featured Books
- smt007 Magazine
Latest Issues
Current IssueWhat's Your Sweet Spot?
Are you in a niche that’s growing or shrinking? Is it time to reassess and refocus? We spotlight companies thriving by redefining or reinforcing their niche. What are their insights?
Moving Forward With Confidence
In this issue, we focus on sales and quoting, workforce training, new IPC leadership in the U.S. and Canada, the effects of tariffs, CFX standards, and much more—all designed to provide perspective as you move through the cloud bank of today's shifting economic market.
Intelligent Test and Inspection
Are you ready to explore the cutting-edge advancements shaping the electronics manufacturing industry? The May 2025 issue of SMT007 Magazine is packed with insights, innovations, and expert perspectives that you won’t want to miss.
- Articles
- Columns
- Links
- Media kit
||| MENU - smt007 Magazine
Henkel's Temperature Stable Solder Paste Living Up to its Promise
September 14, 2015 | HenkelEstimated reading time: 3 minutes
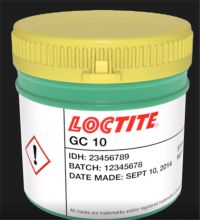
Earlier this year, Henkel Adhesive Technologies introduced the electronics market to the first-ever temperature stable solder paste, LOCTITE GC 10. Since its official debut in February, over 1,000 sample requests of the material have been fulfilled and customers who have qualified the game-changing solder paste are singing its praises.
Matt Polak, owner of Valley View, Ohio-based Raven Systems Design, describes his experience with LOCTITE GC 10. “We have always had issues with paste drying out prematurely and clogging fine-pitch apertures, even during the course of a daily production run,” he explains. “Because of the fine-pitch, high density nature and the reliability requirements of the products we are producing, re-using paste has always been out of the question and we expect to discard a minimum of 1/3 of the unused paste of every jar we open.
LOCTITE GC 10 has completely changed our traditional working models. The paste has given us nothing but perfect, consistent results with no refrigeration. In our evaluation, LOCTITE GC 10 came out of the jar perfect and the printing results at 60 hours were just as good as they were an hour after opening the jar. It printed and reflowed flawlessly and we achieved very close to 100% yield. In addition, we didn’t experience any aperture clogging, the stencil cleaned up easily and the paste didn’t dry out. The cost savings for our business are substantial and far outweigh any incremental cost differential versus competitive pastes. LOCTITE GC 10 is absolutely the ‘game changer’ it claims to be!”
LOCTITE GC 10’s value proposition is extensive, with benefits throughout the logistics and operations chains. Temperature stable at 26.5°C for one year and stable at temperatures of up to 40°C for one month, LOCTITE GC 10 overcomes the processing and performance challenges experienced by conventional solder paste products. Whereas traditional materials have abandon times ranging from 1 to 4 hours on average, LOCTITE GC 10 has abandon times of up to 24 hours, a stencil life of up to 72 hours and zero startup time. The formulation of the material delivers stabilized and consistent print transfer efficiency, an expanded reflow window and increased activity for better results with soak temperatures between 150°C and 200°C.
In addition to its proven performance and in-process cost-efficiency advantages, LOCTITE
GC 10 also provides substantial cost reductions for transport and storage. The temperature stability of the material eliminates the requirement for cold packing and overnight shipping and, once at the factory, can be stored at room temperature. Transportation costs are reduced and energy consumption at the facility is decreased.
When it comes to the logistics benefits of LOCTITE GC 10, Morey Corporation’s Technical Steward, Chris Murphy, enthusiastically shares his satisfaction. “Outside of its excellent process performance, which is always our top priority, the sheer simplicity and cost savings realized by LOCTITE GC 10’s hassle-free material management are incredible,” notes the 30-year veteran of Woodridge, Illinois-based EMS firm. “There is no taking it out of the refrigerator hours before a shift, no complex labeling and, best of all, start-up time is zero. We just take it off the shelf, put it on the stencil and start printing boards. We’ve left LOCTITE GC 10 on the stencil for more than eight hours and it was as creamy as when we first opened the jar – no kneading required. Plus, we can do away with expensive overnight shipping of solder paste and the worry about temperature exposure. With LOCTITE GC 10, we have a lot more latitude and that translates to a more efficient operation.”
More than four years in development, LOCTITE GC 10 has quickly become one of the most significant breakthroughs in solder materials in recent years. “The broad development process and multi-tiered beta testing LOCTITE GC 10 underwent gave us extreme confidence in its performance,” says Henkel Americas Sales Director, Brian Betti. “But, the market reception and incredibly fast adoption have been beyond our expectations. LOCTITE GC 10 is proving to be the game-changer manufacturers need for today’s demanding processes.”
All marks used above are trademarks and/or registered trademarks of Henkel and its affiliates in Germany and elsewhere.
About Henkel
Henkel operates worldwide with leading brands and technologies in three business areas:
Laundry & Home Care, Beauty Care and Adhesive Technologies. Founded in 1876, Henkel holds globally leading market positions both in the consumer and industrial businesses with well-known brands such as Persil, Schwarzkopf and Loctite. Henkel employs about 50,000 people and reported sales of $21.8 billion and adjusted operating profit of $3.4 billion in fiscal 2014. Henkel’s preferred shares are listed in the German stock index DAX.
Suggested Items
Driving Innovation: Direct Imaging vs. Conventional Exposure
07/01/2025 | Simon Khesin -- Column: Driving InnovationMy first camera used Kodak film. I even experimented with developing photos in the bathroom, though I usually dropped the film off at a Kodak center and received the prints two weeks later, only to discover that some images were out of focus or poorly framed. Today, every smartphone contains a high-quality camera capable of producing stunning images instantly.
Hands-On Demos Now Available for Apollo Seiko’s EF and AF Selective Soldering Lines
06/30/2025 | Apollo SeikoApollo Seiko, a leading innovator in soldering technology, is excited to spotlight its expanded lineup of EF and AF Series Selective Soldering Systems, now available for live demonstrations in its newly dedicated demo room.
Indium Corporation Expert to Present on Automotive and Industrial Solder Bonding Solutions at Global Electronics Association Workshop
06/26/2025 | IndiumIndium Corporation Principal Engineer, Advanced Materials, Andy Mackie, Ph.D., MSc, will deliver a technical presentation on innovative solder bonding solutions for automotive and industrial applications at the Global Electronics A
Fresh PCB Concepts: Assembly Challenges with Micro Components and Standard Solder Mask Practices
06/26/2025 | Team NCAB -- Column: Fresh PCB ConceptsMicro components have redefined what is possible in PCB design. With package sizes like 01005 and 0201 becoming more common in high-density layouts, designers are now expected to pack more performance into smaller spaces than ever before. While these advancements support miniaturization and functionality, they introduce new assembly challenges, particularly with traditional solder mask and legend application processes.
Knocking Down the Bone Pile: Tin Whisker Mitigation in Aerospace Applications, Part 3
06/25/2025 | Nash Bell -- Column: Knocking Down the Bone PileTin whiskers are slender, hair-like metallic growths that can develop on the surface of tin-plated electronic components. Typically measuring a few micrometers in diameter and growing several millimeters in length, they form through an electrochemical process influenced by environmental factors such as temperature variations, mechanical or compressive stress, and the aging of solder alloys.